Key Takeaways
- Streamline Operations: BOM software centralizes product data, automates processes, and enhances collaboration for improved efficiency.
- Boost Accuracy and Compliance: Minimize errors and ensure regulatory compliance with real-time updates and version control.
- Support Business Growth: Scale operations seamlessly, reduce costs, and stay competitive with advanced integration and customization features.
In the world of modern manufacturing, the efficient and accurate management of materials is a cornerstone of successful production processes.
One of the key elements in ensuring that every product is built to specification, on time, and within budget, is a tool called the Bill of Materials (BOM).
A BOM is a comprehensive list that outlines all the raw materials, components, sub-assemblies, and other essential items required to manufacture a product.
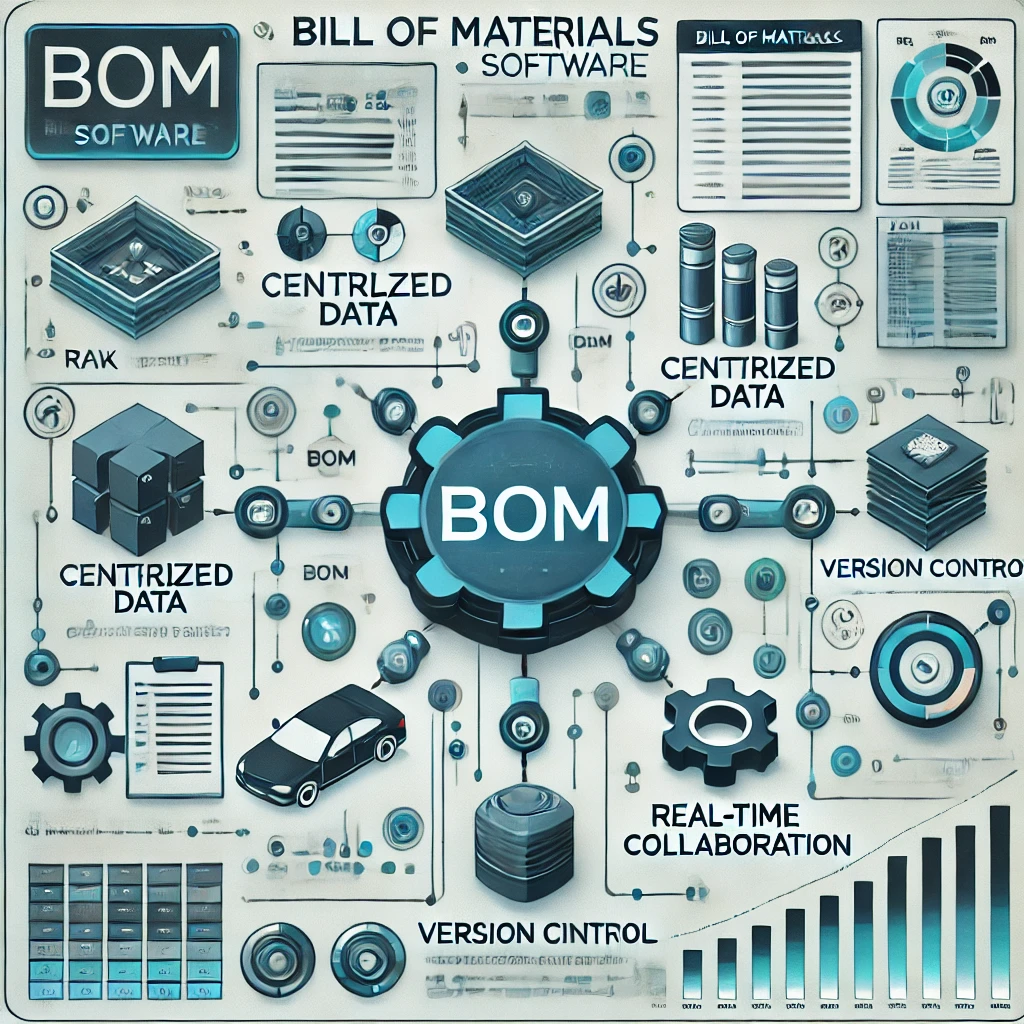
It serves as the blueprint for the production process, enabling manufacturers to streamline their operations, minimize errors, and maintain control over their inventory and supply chain.
Traditionally, creating and managing a BOM was a complex and time-consuming task, often relying on manual processes that were prone to human error.
In today’s fast-paced manufacturing landscape, however, these traditional methods are increasingly being replaced by specialized software solutions—BOM software—that automate and simplify the entire BOM management process.
BOM software helps manufacturers maintain accurate, real-time data, track changes, and ensure that all involved teams—from engineers and procurement to production and logistics—are working with the most up-to-date and precise information.
The importance of BOM software cannot be overstated. It serves as a critical tool not only for product development but also for effective cost management, compliance tracking, and coordination across multiple departments.
As products become more complex and supply chains more global, the role of BOM software in maintaining operational efficiency becomes even more crucial.
Through automation, real-time updates, and seamless integration with other enterprise software systems, BOM software offers manufacturers an indispensable solution to handle the growing demands of modern production processes.
In this blog, we will delve into the essential aspects of BOM software, exploring its functionality, benefits, and the pivotal role it plays in optimizing the manufacturing workflow.
From the basic concept of what a Bill of Materials is to a comprehensive look at how BOM software works, we’ll break down everything you need to know to understand why BOM software is now considered a fundamental tool for businesses in the manufacturing industry.
Whether you’re a small manufacturer or part of a large-scale enterprise, this guide will help you recognize the value that BOM software brings to your operations and why investing in it can significantly enhance your bottom line.
Before we venture further into this article, we would like to share who we are and what we do.
About 9cv9
9cv9 is a business tech startup based in Singapore and Asia, with a strong presence all over the world.
With over nine years of startup and business experience, and being highly involved in connecting with thousands of companies and startups, the 9cv9 team has listed some important learning points in this overview of What is Bill of Materials (BOM) Software and How It Works.
If your company needs recruitment and headhunting services to hire top-quality employees, you can use 9cv9 headhunting and recruitment services to hire top talents and candidates. Find out more here, or send over an email to [email protected].
Or just post 1 free job posting here at 9cv9 Hiring Portal in under 10 minutes.
What is Bill of Materials (BOM) Software and How It Works
- What is Bill of Materials (BOM)?
- How Does BOM Software Work?
- Benefits of Using BOM Software
- Choosing the Right BOM Software
- Common Challenges in BOM Management
1. What is Bill of Materials (BOM)?
A Bill of Materials (BOM) is a comprehensive, structured list that defines all the materials, components, sub-assemblies, and parts required to manufacture a product. It serves as a critical document for the manufacturing process, providing all the necessary details to create a final product, ensuring consistency, quality control, and cost management.
In essence, a BOM outlines what, how much, and how components are used to build a product. It acts as a guide that links design specifications with the production process, providing essential information for procurement, assembly, and quality control. Without an accurate BOM, manufacturers risk errors in product specifications, delays in production, and potential financial losses.
Key Components of a Bill of Materials
- Part Numbers and Descriptions:
- A unique part number assigned to each component or material.
- A brief description of each part for easy identification.
- Quantities:
- The exact quantity of each part required for manufacturing.
- For example, a car engine may require 4 spark plugs, 1 engine block, and 12 screws.
- Materials and Specifications:
- The specific material used for each component (e.g., steel, plastic, copper).
- Material specifications, such as grade, size, and other relevant characteristics (e.g., grade A steel for structural parts).
- Assembly Instructions:
- Detailed instructions on how to assemble the various components.
- Can include notes on the order of assembly, assembly time, and tools required.
- Supplier Information:
- Details of the suppliers of each material or component.
- Includes lead times, part numbers from suppliers, and pricing details.
- Costing Information:
- A breakdown of the costs for each component and the overall product.
- Helps in budgeting and tracking expenses during production.
Types of Bill of Materials
There are several types of BOMs, each serving a different purpose in the manufacturing process. The most common types include:
Engineering Bill of Materials (EBOM)
- Purpose: Created by engineers during the design phase to define the product structure.
- Content: Includes detailed information about the components, materials, and specifications used to design the product.
- Example: In a smartphone, an EBOM would list the screen, battery, camera module, motherboard, and other electronic components, along with their specifications.
Manufacturing Bill of Materials (MBOM)
- Purpose: Used by the manufacturing team for actual production and assembly.
- Content: Lists all the parts, assemblies, and sub-assemblies, including any part that needs to be manufactured or sourced for the assembly.
- Example: In an automotive factory, an MBOM would include every component required to assemble a car, such as doors, seats, tires, electrical components, and fluid systems.
Sales Bill of Materials (SBOM)
- Purpose: Used to define the product from a sales and marketing perspective, often related to configurable products.
- Content: Focuses on the customer-facing configuration of the product.
- Example: A computer manufacturer’s SBOM may include various customizable options, such as processor type, RAM size, and hard drive capacity, allowing customers to build their own systems.
Service Bill of Materials (SBOM)
- Purpose: Utilized by service teams for maintenance and repairs.
- Content: Includes details about parts and components that might need replacement or repair after the product is sold.
- Example: A home appliance service technician may use an SBOM to identify replacement parts for a dishwasher, such as the pump motor, hoses, or filter.
Importance of Bill of Materials in Manufacturing
- Cost Estimation and Budgeting:
- BOMs provide a clear overview of the material costs, allowing manufacturers to estimate production costs accurately and stay within budget.
- Example: A company manufacturing bicycles uses BOM to list each part—frame, wheels, handlebars, brakes, etc.—and calculate total production cost per unit.
- Procurement and Inventory Management:
- Helps ensure the necessary materials are available before production begins by specifying quantities and suppliers.
- Example: A toy manufacturer uses BOM to ensure that all raw materials like plastic, paint, and small fasteners are ordered ahead of time for assembly.
- Product Consistency and Quality Control:
- By using a BOM, manufacturers can ensure that each product is made with the same components and materials, maintaining consistency and quality across production batches.
- Example: In the production of a medical device, a BOM ensures that each unit is assembled with the same sterilized components, maintaining quality standards.
- Compliance and Regulatory Requirements:
- BOMs help manufacturers comply with industry regulations by documenting part specifications and supplier information, ensuring traceability.
- Example: The aerospace industry requires strict documentation of materials and parts for regulatory compliance. A BOM helps meet these requirements, reducing the risk of non-compliance.
Real-World Examples of Bill of Materials in Use
- Electronics Manufacturing:
- For a company that builds a laptop, the EBOM might specify components such as the motherboard, processor, RAM, and display screen. Each part would have detailed specifications, and quantities would reflect the number of units needed for production.
- Automotive Manufacturing:
- An MBOM for a car manufacturer would include everything from nuts and bolts to complex systems like the engine, transmission, and braking systems. This ensures that the assembly line has everything it needs to complete the vehicle.
- Furniture Manufacturing:
- A furniture manufacturer uses a BOM to list materials such as wood, fabric, screws, and nails, and outlines the quantities and suppliers for each. This helps them manage inventory, minimize waste, and maintain production efficiency.
By understanding the key components, types, and importance of a BOM, manufacturers can better manage their production processes, reduce errors, and ensure that products are consistently delivered to customers on time and within budget.
2. How Does BOM Software Work?
Bill of Materials (BOM) software is a specialized tool designed to automate and optimize the creation, management, and tracking of BOMs throughout the product lifecycle. It offers manufacturers a centralized system that streamlines the entire process, reducing errors, improving efficiency, and ensuring that the right materials are available for production. BOM software simplifies the complex task of managing large quantities of parts and materials, providing real-time visibility and control over the entire manufacturing process.
This section explores how BOM software works, its core features, key functionalities, and how it integrates with other enterprise systems to improve the overall production workflow.
Core Features of BOM Software
BOM software comes with various features that make it essential for manufacturers. Here are the core features that allow it to function effectively:
1. Centralized Database
- Definition: A centralized database stores all the BOM data in one location, allowing for easy access and updates by authorized users.
- Example: For a manufacturer of medical devices, the software can store BOMs for different product models, making it easy for engineers and procurement teams to retrieve the necessary information.
2. Real-Time Updates and Version Control
- Definition: BOM software enables real-time updates whenever a change is made to a BOM. It also includes version control, which tracks all changes and ensures that only the latest version is used in production.
- Example: In a furniture company, if a design modification is made to the frame of a chair, the software will automatically update the BOM, notifying the procurement and manufacturing teams to source the updated materials.
3. Integration with Other Enterprise Software
- Definition: BOM software integrates seamlessly with other business software like Enterprise Resource Planning (ERP), Product Lifecycle Management (PLM), and Manufacturing Resource Planning (MRP) systems. This integration enables smooth data sharing across departments.
- Example: In an automotive manufacturing company, BOM software integrates with ERP systems to automate the ordering of parts and materials, ensuring that the correct components are procured in line with the production schedule.
4. Multi-Level BOM Management
- Definition: BOM software supports multi-level BOMs, allowing manufacturers to manage complex assemblies with multiple sub-assemblies and components.
- Example: A computer manufacturer uses multi-level BOM management to list not only the motherboard and processor but also the sub-assemblies for components like the screen, keyboard, and power supply, all of which are required for final assembly.
5. Customizable BOM Templates
- Definition: Most BOM software allows manufacturers to create customizable templates, adapting the software to their specific needs and industry requirements.
- Example: A custom-made jewelry company may use a BOM template that includes gemstones, metal types, and design specifications, while a construction company may customize a BOM template for raw materials like concrete, steel, and timber.
Key Functionalities of BOM Software
BOM software offers a wide range of functionalities that help manufacturers create, manage, and track the production of products in a more efficient and organized manner. The following are the key functionalities of BOM software:
1. Creation and Management of BOM Structures
- Definition: BOM software allows users to create BOM structures, including parts, sub-assemblies, and finished goods, all with a clear hierarchical layout.
- How It Works: Users can define the relationships between components (e.g., “part A is part of sub-assembly B”), and easily modify these relationships as the design evolves.
- Example: A smartphone manufacturer can create a BOM for the entire phone, with sub-assemblies like the screen, camera, and battery listed as individual components within the structure.
2. Costing and Pricing Management
- Definition: BOM software helps calculate the cost of materials, parts, and labor, giving manufacturers the ability to assess the total cost of production.
- How It Works: The software tracks component prices and labor costs and automatically updates the total cost whenever a change is made to the BOM.
- Example: In a clothing factory, BOM software calculates the cost of fabric, buttons, and zippers, and provides a comprehensive overview of the cost per garment.
3. Procurement and Inventory Management
- Definition: BOM software integrates with procurement systems, helping manufacturers manage inventory levels, track material availability, and ensure that materials are ordered on time.
- How It Works: When a BOM is created, the software checks inventory levels in real-time and generates purchase orders for materials that are in insufficient supply.
- Example: A bicycle manufacturer uses BOM software to automatically reorder tires, wheels, and handlebars when stock levels fall below the threshold set in the system.
4. Compliance Tracking and Documentation
- Definition: BOM software helps ensure compliance with industry regulations by tracking material certifications, safety standards, and environmental requirements.
- How It Works: The software stores certifications and compliance documents and automatically checks whether materials meet the required standards.
- Example: A pharmaceutical company utilizes BOM software to track the compliance of raw materials with FDA standards, ensuring that all components used in drug manufacturing are certified and safe.
5. Change Management and Revision Control
- Definition: BOM software allows manufacturers to track changes to parts, assemblies, and designs, ensuring that the correct version of a BOM is always in use.
- How It Works: When changes are made, the software records the change history, including the date, user who made the change, and the reason behind it. It also ensures that teams are notified of any BOM revisions.
- Example: A laptop manufacturer might revise a BOM when upgrading a model’s processor, and the software will track the revision, alerting all stakeholders to the new BOM version.
6. Reporting and Analytics
- Definition: BOM software generates detailed reports and analytics, providing insights into material usage, inventory levels, and overall production costs.
- How It Works: Reports can be generated based on various parameters such as cost breakdowns, material shortages, and lead times, enabling informed decision-making.
- Example: A toy manufacturer uses reports from BOM software to analyze material waste and identify cost-saving opportunities during production.
Integration of BOM Software with Other Systems
BOM software doesn’t work in isolation; it integrates with other business systems to provide a seamless and holistic solution for managing the manufacturing process. Here are some examples of how BOM software integrates with other systems:
1. ERP Systems Integration
- Definition: ERP systems help manage and automate the core business processes like inventory, procurement, and order fulfillment. Integrating BOM software with ERP ensures smooth data flow between product design and resource management.
- Example: A custom machinery manufacturer integrates its BOM software with ERP to automatically generate purchase orders for raw materials when a new machine design is finalized.
2. PLM (Product Lifecycle Management) Integration
- Definition: PLM systems focus on managing product data and design throughout the product lifecycle. Integrating BOM software with PLM systems allows engineers and designers to synchronize BOM data with product design updates.
- Example: An aerospace manufacturer integrates BOM software with PLM to align the BOM with design changes during the development of a new aircraft model.
3. MRP (Manufacturing Resource Planning) Integration
- Definition: MRP systems help plan manufacturing activities, including scheduling and material planning. By integrating BOM software with MRP, manufacturers can optimize production planning and ensure that the right materials are available when needed.
- Example: A food processing plant integrates BOM software with MRP to optimize production schedules and ensure that all ingredients are ordered and available for production at the right time.
Conclusion
BOM software is an indispensable tool for modern manufacturers, providing a centralized and automated system to manage the complex task of creating, managing, and tracking Bills of Materials. Through its core features and key functionalities, BOM software streamlines the production process, reduces errors, and improves operational efficiency. Integration with ERP, PLM, and MRP systems further enhances the software’s ability to provide seamless data flow across departments, ensuring that every part of the manufacturing process is aligned and optimized. With the ability to manage costs, inventory, compliance, and revisions, BOM software ultimately helps businesses maintain control, save time, and improve profitability.
3. Benefits of Using BOM Software
Bill of Materials (BOM) software offers transformative advantages for organizations involved in manufacturing, engineering, and supply chain management. By automating and streamlining BOM processes, businesses can improve operational efficiency, reduce errors, and enhance collaboration across teams. Below, we explore the key benefits of BOM software, categorized into various sub-sections for clarity.
1. Enhanced Accuracy and Reduced Errors
- Minimized Manual Errors
- BOM software automates data entry and updates, reducing the risk of human errors in material lists.
- Example: In an automotive factory, software ensures precise data for assembling complex vehicles with hundreds of components.
- Real-Time Data Synchronization
- Ensures all stakeholders have access to the most up-to-date BOMs, reducing discrepancies.
- Example: A furniture company avoids production delays by instantly updating changes to the BOM for a new design.
- Error Detection Mechanisms
- Flags inconsistencies, missing components, or incorrect quantities in BOMs.
- Example: A smartphone manufacturer uses BOM software to detect an overlooked part in a multi-level assembly before production begins.
2. Improved Collaboration Across Teams
- Centralized Data Repository
- Provides a single source of truth for engineers, designers, procurement teams, and production managers.
- Example: In an aerospace company, engineers and procurement teams simultaneously access the latest BOM for an aircraft wing assembly.
- Streamlined Communication
- Allows team members to leave comments, make suggestions, or request changes directly within the software.
- Example: A custom electronics firm accelerates product development by enabling seamless interaction between design and production teams.
- Global Accessibility
- Cloud-based BOM software allows teams in different locations to collaborate effectively.
- Example: A multinational company ensures that its U.S.-based design team and Asian manufacturing unit stay aligned on BOM updates.
3. Cost and Time Savings
- Efficient Procurement Management
- Tracks material availability and generates purchase orders to prevent overstocking or shortages.
- Example: A packaging company uses BOM software to order exact quantities of materials, avoiding excess inventory costs.
- Faster Time-to-Market
- Reduces delays in product development and manufacturing by automating BOM processes.
- Example: A medical device company brings new products to market quickly by streamlining its BOM creation and revision process.
- Optimized Resource Utilization
- Ensures efficient use of materials and labor, reducing waste and rework.
- Example: A clothing manufacturer minimizes fabric waste by accurately calculating material requirements through BOM software.
4. Scalability and Adaptability
- Handling Complex BOMs
- Effectively manages multi-level BOMs for products with intricate sub-assemblies.
- Example: An industrial equipment manufacturer handles BOMs for machinery with hundreds of sub-components using advanced software features.
- Customization for Different Industries
- Adapts to various industries with customizable templates and configurations.
- Example: A food and beverage company tailors BOM software to include recipes, packaging materials, and nutritional data.
- Support for Growth
- Scales to accommodate increasing production volumes or product lines.
- Example: A startup transitioning from small-scale production to mass manufacturing uses BOM software to handle its growing inventory needs.
5. Better Compliance and Quality Assurance
- Regulatory Compliance Tracking
- Ensures that all materials meet industry regulations and safety standards.
- Example: A pharmaceutical company tracks FDA compliance for raw materials in drug production.
- Document Management
- Maintains certifications, warranties, and material specifications for easy retrieval.
- Example: An aerospace manufacturer stores material certifications to demonstrate compliance with stringent aviation standards.
- Enhanced Quality Control
- Links materials and components to quality checks, ensuring adherence to production standards.
- Example: An electronics company integrates quality testing records with BOM software to trace faulty components.
6. Improved Inventory and Supply Chain Management
- Inventory Optimization
- Monitors stock levels in real-time, preventing overstocking and shortages.
- Example: A bicycle manufacturer prevents delays by using BOM software to maintain optimal inventory levels for high-demand parts.
- Supply Chain Transparency
- Tracks supplier performance, lead times, and material sourcing.
- Example: An automotive parts supplier uses BOM software to analyze delays in raw material delivery and switch to more reliable suppliers.
- Forecasting and Demand Planning
- Predicts future material needs based on historical data and trends.
- Example: A seasonal toy manufacturer uses forecasting tools within BOM software to prepare for holiday demand spikes.
7. Streamlined Change Management
- Real-Time Revision Control
- Tracks all changes to BOMs and maintains version history.
- Example: A consumer electronics company tracks updates to its BOM when launching a new model of its flagship smartphone.
- Automated Notifications
- Sends alerts to relevant teams whenever a BOM is revised.
- Example: In a car manufacturing plant, BOM updates for new safety features are immediately shared with production and procurement teams.
- Impact Analysis
- Evaluates how changes in one component affect the entire product.
- Example: A laptop manufacturer assesses the impact of switching to a more sustainable material for its casings.
8. Comprehensive Reporting and Analytics
- Detailed Cost Breakdown
- Generates reports on material costs, labor expenses, and overheads.
- Example: A kitchen appliance company uses cost breakdowns to evaluate profit margins for each product line.
- Performance Monitoring
- Tracks key performance indicators (KPIs) for production efficiency and material usage.
- Example: A furniture manufacturer identifies inefficiencies in material usage through analytics provided by the BOM software.
- Customizable Dashboards
- Offers real-time visual insights tailored to different user roles.
- Example: Procurement managers at an electronics firm use dashboards to monitor supplier lead times and material availability.
Conclusion
BOM software is an indispensable tool for modern manufacturers, offering a wide range of benefits that streamline operations, enhance collaboration, and improve decision-making. By automating processes, reducing errors, and ensuring compliance, BOM software not only drives efficiency but also supports growth and innovation across industries. From small-scale manufacturers to large enterprises, the advantages of adopting BOM software are clear, making it a critical investment for companies aiming to remain competitive in today’s fast-paced manufacturing landscape.
4. Choosing the Right BOM Software
Selecting the right Bill of Materials (BOM) software is critical for optimizing operations, ensuring accuracy, and driving efficiency in manufacturing and product development. With numerous options available in the market, it is important to evaluate your specific business needs and match them with the features offered by different BOM solutions. Below is a comprehensive guide divided into sub-sections to help you make an informed decision.
1. Assess Your Business Needs
- Industry-Specific Requirements
- Identify features that cater specifically to your industry.
- Example: An electronics manufacturer may need support for multi-level BOMs to manage complex product designs.
- Company Size and Scale
- Consider software scalability if you plan to grow your operations.
- Example: A small startup might start with a lightweight solution but require advanced features as it scales to mass production.
- Integration with Existing Systems
- Ensure the BOM software integrates seamlessly with your ERP, MRP, or CAD systems.
- Example: A furniture manufacturer may require integration with design software like AutoCAD for efficient material planning.
2. Key Features to Look For
- Ease of Use
- User-friendly interfaces and intuitive navigation to minimize learning curves.
- Example: A small-scale jewelry maker benefits from an easy-to-learn BOM tool with drag-and-drop functionality.
- Real-Time Collaboration
- Support for team collaboration across departments and geographic locations.
- Example: A global manufacturing firm allows engineers and procurement teams to collaborate in real-time on BOM changes.
- Version Control and Change Management
- Tracks revisions and maintains a history of changes.
- Example: A smartphone manufacturer uses version control to document updates in BOMs for different product models.
- Automation Capabilities
- Automates repetitive tasks like generating purchase orders and updating inventory.
- Example: A clothing company automates material reordering to avoid production delays.
- Customizability
- Allows configuration to meet unique business processes.
- Example: A medical device manufacturer customizes the software to include compliance tracking for FDA-approved materials.
3. Evaluate Vendor Reputation and Support
- Track Record of the Vendor
- Research the vendor’s history, user reviews, and case studies.
- Example: A high-tech equipment manufacturer might opt for a vendor with proven experience in handling complex BOM requirements.
- Customer Support
- Ensure the vendor offers robust technical support and training.
- Example: A startup with limited IT resources prefers a vendor that provides 24/7 customer support and onboarding tutorials.
- Software Updates and Maintenance
- Check if the vendor regularly updates the software with new features and security enhancements.
- Example: A food processing company relies on frequent updates to keep up with changing regulatory requirements.
4. Consider Deployment Options
- Cloud-Based Solutions
- Ideal for remote accessibility and scalability.
- Example: A multinational company with dispersed teams uses cloud-based BOM software to ensure global collaboration.
- On-Premises Solutions
- Suitable for businesses requiring high-level data security and control.
- Example: A defense contractor opts for an on-premises solution to meet strict security protocols.
- Hybrid Options
- Combines the benefits of both cloud and on-premises deployments.
- Example: A mid-sized manufacturing firm uses a hybrid setup to balance cost efficiency and data security.
5. Budget and Cost Considerations
- Total Cost of Ownership (TCO)
- Include licensing fees, implementation costs, and ongoing maintenance.
- Example: A startup might choose a subscription-based model to minimize upfront costs.
- Return on Investment (ROI)
- Assess how the software will contribute to cost savings and efficiency.
- Example: A furniture company evaluates ROI by analyzing reductions in material waste and faster production cycles.
- Scalable Pricing Models
- Opt for flexible pricing plans that align with your business growth.
- Example: A growing toy manufacturer selects a solution that offers additional features as their production needs expand.
6. Integration Capabilities
- ERP and MRP Systems
- Ensures seamless synchronization of BOMs with enterprise resource planning tools.
- Example: An automotive company integrates BOM software with its SAP ERP system for streamlined operations.
- CAD and PLM Systems
- Facilitates the transfer of design data into BOMs.
- Example: A 3D printing firm integrates BOM software with SolidWorks to automate material listing from design files.
- Inventory and Supply Chain Management
- Links BOM data to inventory tracking and supplier management systems.
- Example: An electronics manufacturer avoids shortages by integrating BOM software with its inventory system.
7. Test and Compare Options
- Free Trials and Demos
- Utilize free trials to evaluate usability and compatibility.
- Example: A small machinery manufacturer tests multiple BOM tools before committing to a purchase.
- Feature Comparisons
- Use comparison charts to weigh the pros and cons of each software.
- Example: An apparel company lists must-have features like inventory forecasting and chooses the software that meets most criteria.
- User Feedback
- Seek input from employees who will use the software daily.
- Example: An engineering firm involves its design and procurement teams in the decision-making process.
8. Compliance and Security
- Regulatory Compliance Support
- Ensure the software helps meet industry-specific regulations.
- Example: A pharmaceutical company ensures compliance with ISO standards by selecting a validated BOM tool.
- Data Security Features
- Look for encryption, role-based access, and secure backups.
- Example: A military supplier requires robust security to protect sensitive component data.
9. Long-Term Scalability and Flexibility
- Adaptability to Future Needs
- Choose software that can evolve with your business.
- Example: A tech startup selects BOM software that supports future integration with IoT systems.
- Global Expansion Support
- Ensures the software can handle multiple currencies and languages.
- Example: A global consumer goods manufacturer selects a solution that accommodates international supply chain complexities.
Conclusion
Choosing the right BOM software is a strategic decision that can significantly impact a business’s efficiency, accuracy, and profitability. By carefully assessing your needs, prioritizing essential features, and evaluating vendors, you can identify a solution that aligns with your current operations and future growth plans. Investing in the right BOM software not only streamlines your processes but also positions your organization for sustained success in a competitive market.
5. Common Challenges in BOM Management
Managing a Bill of Materials (BOM) effectively is critical for product development and manufacturing. However, BOM management is fraught with challenges that can disrupt workflows, increase costs, and reduce productivity if not addressed. Below, we explore the common challenges in BOM management, illustrated with real-world examples and actionable insights.
1. Inaccurate or Incomplete Data
- Errors in Material Details
- Incorrect or missing specifications lead to production errors.
- Example: A smartphone manufacturer omits a key resistor value in the BOM, causing a batch of defective products.
- Inconsistent Data Formatting
- Variations in data entry standards across teams create confusion.
- Example: An automotive company’s procurement team struggles because the same material is listed with different codes by engineering.
- Outdated Information
- Failure to update BOMs with revised components leads to inefficiencies.
- Example: A machinery manufacturer uses an outdated BOM version, resulting in orders for obsolete parts.
2. Version Control Issues
- Difficulty Tracking Revisions
- Lack of proper versioning leads to the use of outdated BOMs.
- Example: An aerospace company’s engineering team works on an older BOM version, causing delays in incorporating updated materials.
- Collaboration Challenges
- Teams working in silos fail to synchronize BOM changes.
- Example: A large electronics company’s design and production teams clash over unsynchronized BOM updates.
3. Complexity of Multi-Level BOMs
- Managing Nested Components
- Multi-level BOMs increase the difficulty of tracking sub-assemblies.
- Example: A medical device manufacturer struggles to trace specific parts within a multi-level BOM for compliance audits.
- Errors in Roll-Ups
- Summing up quantities across levels can lead to miscalculations.
- Example: An automotive company orders excess fasteners due to errors in a multi-level BOM summary.
4. Communication Gaps
- Poor Cross-Department Collaboration
- Engineering, procurement, and manufacturing teams lack clear communication channels.
- Example: A fashion brand’s design team updates the BOM but fails to inform production, leading to material shortages.
- Global Team Misalignment
- Remote teams face challenges in accessing and understanding BOM updates.
- Example: A global electronics firm’s teams in Asia and Europe misinterpret component specifications due to regional terminology differences.
5. Inventory and Procurement Challenges
- Overstocking or Understocking
- Inaccurate BOMs disrupt inventory management.
- Example: A furniture company underestimates wood requirements due to incorrect BOM data, delaying production schedules.
- Supplier Coordination Issues
- Poor communication of material specifications to suppliers causes delays.
- Example: A solar panel manufacturer receives the wrong type of silicon wafers due to vague descriptions in the BOM.
6. Regulatory and Compliance Risks
- Failure to Meet Standards
- BOMs lacking compliance data risk regulatory penalties.
- Example: A pharmaceutical company faces FDA scrutiny for not documenting raw material sources in its BOM.
- Difficulty in Traceability
- Incomplete BOMs hinder the ability to trace defective components.
- Example: An electronics firm recalls a product but struggles to identify affected components due to missing serial numbers in the BOM.
7. Data Integration Challenges
- Lack of System Interoperability
- BOM software that doesn’t integrate with other systems causes inefficiencies.
- Example: A consumer goods manufacturer experiences delays when its BOM software fails to sync with its ERP system.
- Manual Data Entry
- Reliance on manual processes increases errors and delays.
- Example: A small startup manually transfers BOM data into spreadsheets, leading to frequent errors and miscalculations.
8. High Costs and Resource Wastage
- Material Waste Due to Errors
- Inaccurate BOMs lead to over-ordering and wastage.
- Example: A packaging company discards surplus raw materials ordered due to a miscalculation in the BOM.
- Time-Consuming Rework
- Rectifying errors in BOMs adds to project timelines and costs.
- Example: A drone manufacturer spends weeks revising production schedules due to inaccuracies in the initial BOM.
9. Scalability Issues
- Inability to Handle Growth
- As businesses scale, static BOM processes become inadequate.
- Example: A growing startup expands to mass production but struggles to manage complex BOMs with manual systems.
- Limited Customization Options
- Static BOMs fail to adapt to new product lines or variations.
- Example: A modular furniture company needs dynamic BOMs to handle custom orders, but the current system lacks flexibility.
10. Security and Access Control
- Unauthorized Modifications
- Lack of access control allows unapproved changes to BOMs.
- Example: An engineering intern at a manufacturing company accidentally modifies critical data, causing a production error.
- Data Breaches
- Sensitive product data in BOMs is at risk of unauthorized access.
- Example: A defense contractor experiences a security breach, exposing details of classified components.
Conclusion
The challenges in BOM management, from inaccurate data to security risks, can significantly impact manufacturing efficiency and cost-effectiveness. By identifying and addressing these common issues, companies can streamline their operations and ensure smooth collaboration between teams. Implementing robust BOM software with features such as version control, real-time collaboration, and integration with other systems can help overcome these challenges and optimize overall productivity.
Conclusion
The complexity of modern manufacturing demands precision, efficiency, and streamlined processes. Bill of Materials (BOM) software has emerged as a critical tool to meet these challenges, transforming how businesses design, produce, and manage their products. From automating data entry and enhancing collaboration to ensuring regulatory compliance and minimizing costs, BOM software provides a comprehensive solution to many pain points in the manufacturing process.
The Role of BOM Software in Modern Manufacturing
- Centralized Data Management: BOM software consolidates all product-related data, offering a single source of truth. This eliminates discrepancies and ensures accuracy in all stages of production.
- Example: A consumer electronics company reduced production errors by 30% by adopting a cloud-based BOM solution.
- Real-Time Collaboration: With teams often spread across geographies, the need for seamless communication is vital. BOM software enables synchronized updates, ensuring all stakeholders work from the same data.
- Example: An automotive giant improved its cross-departmental collaboration, reducing lead times by 15%.
- Efficiency Gains: Automated processes within BOM software significantly cut down on manual labor, improving efficiency and allowing teams to focus on innovation.
- Example: A furniture manufacturer accelerated its time-to-market by leveraging BOM software for real-time updates.
Why BOM Software is Essential for Business Growth
- Scalability: As companies grow and product lines expand, the ability to handle complex BOMs becomes critical. BOM software provides the flexibility and tools to scale operations seamlessly.
- Cost Savings: By reducing material waste, optimizing inventory, and preventing production delays, BOM software directly impacts a company’s bottom line.
- Future-Proofing Operations: Advanced features such as integration with PLM, ERP, and CAD systems position businesses to stay competitive in an ever-evolving market.
Addressing Common Challenges with BOM Software
- Overcoming Data Inaccuracies: BOM software ensures accurate data input and real-time updates, reducing costly errors.
- Streamlining Version Control: Integrated version tracking eliminates confusion caused by outdated information.
- Navigating Compliance Requirements: With built-in compliance features, BOM software simplifies audits and ensures adherence to industry regulations.
Key Takeaways for Businesses
- BOM software is not just a tool but a strategic asset that drives operational excellence.
- Selecting the right BOM software tailored to your business needs is crucial. Factors such as scalability, integration capabilities, and user-friendliness should guide your choice.
- Implementing BOM software requires thoughtful planning and cross-departmental collaboration to realize its full potential.
A Future of Innovation with BOM Software
As technology advances, BOM software is expected to evolve further, integrating with cutting-edge technologies like artificial intelligence (AI), machine learning, and IoT. These advancements promise even greater efficiency, predictive capabilities, and automation in the manufacturing process.
For businesses striving to stay competitive, investing in BOM software is no longer optional—it’s a necessity. By leveraging this powerful tool, companies can enhance productivity, reduce costs, and ensure the successful delivery of high-quality products in today’s fast-paced marketplace.
Final Thought
Understanding what BOM software is and how it works is the first step toward transforming your manufacturing operations. Whether you are a small startup or a global enterprise, adopting BOM software will empower your team, streamline processes, and unlock new opportunities for growth.
If you find this article useful, why not share it with your hiring manager and C-level suite friends and also leave a nice comment below?
We, at the 9cv9 Research Team, strive to bring the latest and most meaningful data, guides, and statistics to your doorstep.
To get access to top-quality guides, click over to 9cv9 Blog.
People Also Ask
What is Bill of Materials (BOM) software?
Bill of Materials (BOM) software is a tool used in manufacturing to manage product data, including components, raw materials, and assembly instructions, ensuring efficient production processes.
How does BOM software work?
BOM software centralizes product data, automates processes like updates and version control, and integrates with systems like ERP and CAD for seamless operations.
What industries use BOM software?
Industries like manufacturing, automotive, aerospace, electronics, and consumer goods heavily rely on BOM software for product lifecycle management.
Why is BOM software important?
BOM software streamlines operations, ensures data accuracy, supports compliance, and enhances collaboration across departments for efficient production.
What are the key features of BOM software?
Key features include centralized data management, version control, integration with ERP and CAD systems, compliance tracking, and reporting tools.
What are the benefits of BOM software?
BOM software improves accuracy, reduces production errors, enhances collaboration, minimizes costs, and accelerates product time-to-market.
How does BOM software improve collaboration?
BOM software provides real-time updates and shared access, allowing teams across departments or locations to work on the same data efficiently.
Can BOM software handle multi-level BOMs?
Yes, BOM software supports multi-level BOMs by organizing complex assemblies into hierarchies for better visibility and management.
What is the difference between single-level and multi-level BOMs?
Single-level BOMs list components for a single assembly, while multi-level BOMs detail hierarchical structures of sub-assemblies and components.
Is BOM software suitable for small businesses?
Yes, many BOM software solutions offer scalable options, making them ideal for small businesses looking to improve efficiency and reduce errors.
How does BOM software integrate with ERP systems?
BOM software integrates with ERP systems to share data like inventory levels, procurement details, and production schedules seamlessly.
What is the role of version control in BOM software?
Version control ensures that all stakeholders work with the latest BOM data, reducing errors caused by outdated or incorrect information.
Can BOM software track compliance?
Yes, BOM software includes compliance tracking features, ensuring products meet industry standards and regulatory requirements.
What are some common challenges in BOM management?
Common challenges include data inaccuracies, outdated information, inefficient version control, and compliance risks, which BOM software addresses.
How does BOM software reduce production costs?
BOM software minimizes waste, optimizes inventory management, and prevents production delays, leading to significant cost savings.
What are the integration capabilities of BOM software?
BOM software integrates with systems like PLM, ERP, CAD, and supply chain management tools for streamlined operations and data consistency.
How secure is BOM software?
Most BOM software solutions offer robust security features, including user authentication, data encryption, and role-based access controls.
Can BOM software be customized?
Yes, many BOM software solutions allow customization to meet specific business needs, including workflows, reports, and data fields.
What are the costs of implementing BOM software?
Costs vary based on the software’s features, scalability, and licensing model, with options available for different budget ranges.
What is cloud-based BOM software?
Cloud-based BOM software is hosted online, offering accessibility from anywhere, real-time updates, and easier scalability for businesses.
What is on-premise BOM software?
On-premise BOM software is installed locally on a company’s servers, offering more control but requiring in-house IT management and maintenance.
What factors should be considered when choosing BOM software?
Consider scalability, integration capabilities, user-friendliness, security, and support for your industry-specific requirements when selecting BOM software.
What are some popular BOM software tools?
Popular tools include Arena Solutions, OpenBOM, SolidWorks, and SAP PLM, each offering unique features for various industries.
How long does it take to implement BOM software?
Implementation time depends on the software complexity and business size, typically ranging from a few weeks to several months.
Can BOM software support remote teams?
Yes, cloud-based BOM software enables remote teams to access, update, and collaborate on product data from anywhere in real time.
How does BOM software improve inventory management?
BOM software tracks material usage, updates inventory levels, and provides alerts for reordering, ensuring optimal inventory control.
Is training required to use BOM software?
Most BOM software requires basic training to familiarize users with its features, ensuring effective adoption and utilization.
What is the future of BOM software?
The future includes AI-driven analytics, IoT integration, and advanced automation to further enhance manufacturing efficiency and decision-making.
How can BOM software support sustainability goals?
BOM software helps track sustainable materials, reduce waste, and improve resource efficiency, aligning with eco-friendly practices.
What are the risks of not using BOM software?
Without BOM software, businesses face risks like data errors, compliance failures, production delays, and increased operational costs.