Key Takeaways
- CAPA software automates and streamlines the process of identifying, correcting, and preventing quality issues in compliance-driven industries.
- It enhances root cause analysis, documentation, tracking, and regulatory compliance through centralized, real-time data management.
- Implementing CAPA software fosters continuous improvement, reduces operational risks, and ensures audit readiness across organizations.
In today’s competitive and highly regulated industries, maintaining product quality, ensuring customer satisfaction, and complying with international standards are not just desirable goals—they are essential requirements. Whether in pharmaceuticals, medical devices, manufacturing, food and beverage, or aerospace, organizations face constant scrutiny from regulatory bodies and customers alike. One of the most critical tools used to uphold these standards and drive continuous improvement is Corrective and Preventive Action (CAPA) software. Designed to help organizations systematically identify, investigate, and resolve issues, CAPA software plays a vital role in ensuring compliance and reducing risk across all operational levels.
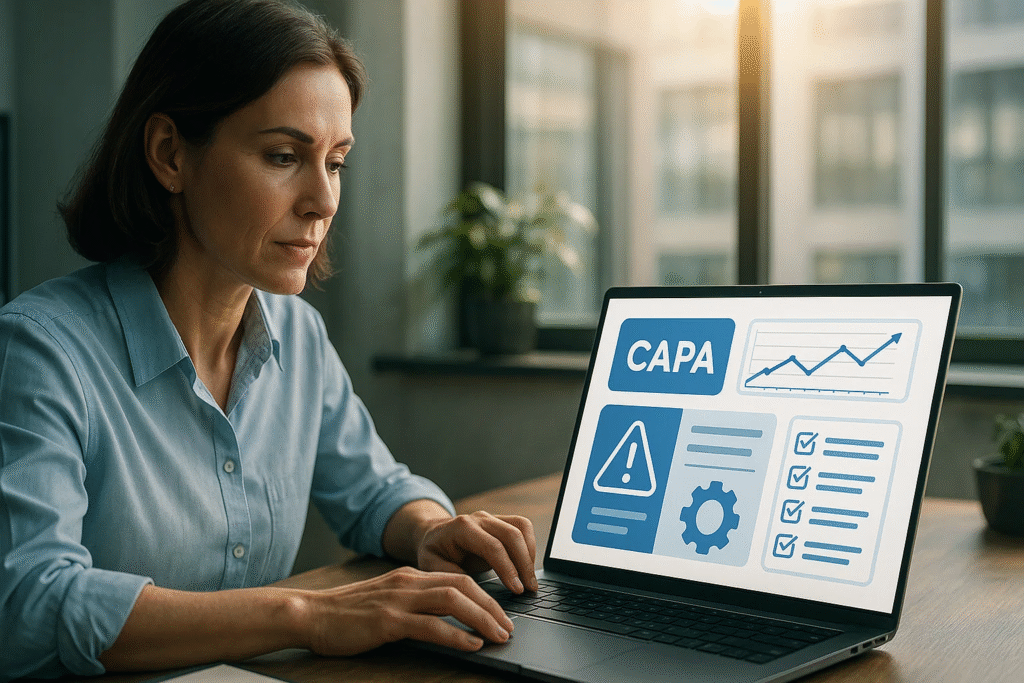
At its core, CAPA is a structured quality management process that enables organizations to correct existing problems (Corrective Actions) and proactively prevent potential issues from occurring in the future (Preventive Actions). Traditionally, CAPA procedures were paper-based, time-consuming, and prone to human error, making it difficult to track the lifecycle of issues or demonstrate compliance during audits. However, the evolution of CAPA software solutions has transformed this landscape by automating and streamlining the entire CAPA process—from problem identification to root cause analysis, action plan execution, and verification of effectiveness.
Modern CAPA software is a centralized digital platform integrated with other quality systems such as Document Management, Audit Management, Nonconformance Handling, and Risk Management. It not only helps reduce manual effort and administrative overhead but also ensures complete traceability, faster resolution cycles, and consistent regulatory compliance with standards like FDA 21 CFR Part 820, ISO 9001, GMP, and more. CAPA systems offer real-time visibility into quality trends and enable organizations to proactively mitigate risks before they escalate into costly non-compliance or recalls.
With increasing pressure from global regulatory agencies, companies are shifting toward agile and intelligent CAPA systems that can seamlessly integrate with broader Quality Management Systems (QMS). These solutions offer robust capabilities such as automated workflows, centralized documentation, built-in analytics, and role-based access control, allowing quality teams to collaborate more efficiently and improve accountability. CAPA software also supports audit readiness by maintaining a thorough audit trail of every action taken, providing critical documentation when undergoing internal or third-party audits.
As regulatory requirements become stricter and supply chains more complex, the implementation of effective CAPA software is no longer optional—it’s a strategic necessity. Businesses that leverage these systems not only gain a competitive advantage through improved quality and operational efficiency but also enhance customer trust and long-term sustainability. Whether you’re managing compliance in a highly regulated industry or aiming to foster a culture of continuous improvement, understanding how CAPA software works and selecting the right solution is crucial.
This comprehensive guide explores what Corrective and Preventive Action (CAPA) software is, how it functions, its key features, real-world applications, and the benefits it delivers to organizations of all sizes. By the end of this article, you will have a clear understanding of how CAPA tools can streamline your quality processes, safeguard compliance, and empower your team to focus on strategic growth rather than reactive problem-solving.
Before we venture further into this article, we would like to share who we are and what we do.
About 9cv9
9cv9 is a business tech startup based in Singapore and Asia, with a strong presence all over the world.
With over nine years of startup and business experience, and being highly involved in connecting with thousands of companies and startups, the 9cv9 team has listed some important learning points in this overview of What is Corrective and Preventive Action (CAPA) Software & How It Works.
If your company needs recruitment and headhunting services to hire top-quality employees, you can use 9cv9 headhunting and recruitment services to hire top talents and candidates. Find out more here, or send over an email to [email protected].
Or just post 1 free job posting here at 9cv9 Hiring Portal in under 10 minutes.
What is Corrective and Preventive Action (CAPA) Software & How It Works
- What is CAPA (Corrective and Preventive Action)?
- What is CAPA Software?
- Key Features of CAPA Software
- How CAPA Software Works
- Benefits of Using CAPA Software
- Common Use Cases and Real-World Applications
- Factors to Consider When Choosing CAPA Software
1. What is CAPA (Corrective and Preventive Action)?
Corrective and Preventive Action (CAPA) is a fundamental element of effective quality management and regulatory compliance. CAPA refers to a systematic process for identifying, investigating, correcting, and preventing the recurrence or potential occurrence of nonconformities or other undesirable situations within an organization. It plays a critical role in maintaining product integrity, operational efficiency, and adherence to industry standards like FDA 21 CFR Part 820, ISO 13485, GMP, and ISO 9001.
1. Definition and Purpose of CAPA
- Corrective Action (CA):
Measures taken to eliminate the causes of identified nonconformities or problems to prevent recurrence. - Preventive Action (PA):
Proactive steps implemented to eliminate potential causes of nonconformities or issues before they happen. - Main Objectives:
- Improve product quality
- Ensure regulatory compliance
- Promote continuous improvement
- Reduce customer complaints and product recalls
- Strengthen root cause analysis processes
2. Key Components of a CAPA System
Component | Description |
---|---|
Problem Identification | Capture and report the issue (nonconformance, audit finding, complaint, etc.) |
Investigation | Analyze the issue to understand its root cause |
Root Cause Analysis | Use structured tools (e.g., 5 Whys, Fishbone Diagram) to identify cause |
Corrective Action Plan | Define and implement actions to address the root cause |
Preventive Action Plan | Implement steps to prevent similar issues in the future |
Effectiveness Check | Verify if the corrective/preventive actions resolved the problem |
Documentation | Maintain records for audit readiness and traceability |
3. Difference Between Corrective and Preventive Actions
Criteria | Corrective Action | Preventive Action |
---|---|---|
Trigger | Known issue or nonconformance | Potential risk or opportunity for failure |
Objective | Eliminate root cause of existing problem | Mitigate risk before it results in a problem |
Example | Replacing faulty components in a failed batch | Redesigning product to avoid possible failure |
Frequency | Reactive (after event) | Proactive (before event) |
Compliance Impact | Typically required during audits or CAPA reviews | Demonstrates maturity of QMS |
4. Real-World Examples of CAPA in Practice
- Pharmaceutical Industry:
- Corrective: Recalling a batch of drugs after discovering contamination due to improper sanitation.
- Preventive: Updating SOPs and employee training to ensure proper cleaning protocols.
- Medical Devices:
- Corrective: Fixing a software bug in a diagnostic machine after a customer complaint.
- Preventive: Implementing automated code review to detect bugs before product release.
- Manufacturing:
- Corrective: Replacing defective bearings in a production line after several failures.
- Preventive: Introducing predictive maintenance to monitor wear and tear over time.
- Food & Beverage:
- Corrective: Discarding expired ingredients after discovering inventory mismanagement.
- Preventive: Integrating an inventory tracking system to alert before expiry.
5. Common Triggers for Initiating a CAPA Process
- Internal or external audit findings
- Customer complaints or product returns
- Nonconformance reports (NCRs)
- Deviations from standard operating procedures (SOPs)
- Supplier quality issues
- Regulatory inspection outcomes
6. Tools Commonly Used in CAPA Investigations
Tool | Purpose |
---|---|
5 Whys Analysis | Identify root cause by asking “why” repeatedly |
Fishbone (Ishikawa) Diagram | Visualize cause-and-effect relationships |
Pareto Analysis | Prioritize issues based on frequency/severity |
FMEA (Failure Mode and Effects Analysis) | Evaluate potential failure risks and their impact |
Flowcharts | Understand process steps and identify failure points |
7. CAPA Workflow Process (Visual Representation)
A[Problem Identified] --> B[Investigation Launched]
B --> C[Root Cause Analysis]
C --> D[Corrective Action Plan]
C --> E[Preventive Action Plan]
D --> F[Implementation]
E --> F
F --> G[Effectiveness Review]
G --> H[Closure and Documentation]
8. Benefits of a Robust CAPA System
- Operational Efficiency:
- Streamlined issue resolution
- Reduced downtime and disruptions
- Regulatory Readiness:
- Audit trails and documented evidence
- Compliance with ISO, FDA, GMP, etc.
- Risk Mitigation:
- Preventive actions reduce chance of future failures
- Enhanced customer satisfaction and trust
- Continuous Improvement:
- Data-driven decision-making
- Ongoing process refinement
9. Integration of CAPA into Quality Management Systems (QMS)
- CAPA is often integrated with modules like:
- Nonconformance Management
- Audit Management
- Document Control
- Risk Management
- Benefits of integration:
- Centralized data and communication
- Seamless escalation from issue to resolution
- Improved visibility and accountability across teams
10. Conclusion: Why CAPA is Essential for Quality Management
CAPA is not merely a regulatory requirement but a strategic tool for building resilient, high-performing organizations. It empowers companies to address existing failures, foresee potential threats, and continuously enhance quality systems. When backed by automation through CAPA software, this process becomes faster, more reliable, and easier to scale across departments and geographies.
2. What is CAPA Software?
CAPA Software—short for Corrective and Preventive Action Software—is a digital solution designed to automate and manage the entire CAPA process within an organization’s Quality Management System (QMS). It enables companies to systematically document, track, investigate, and resolve quality issues, ensuring full regulatory compliance and continuous process improvement. CAPA software is widely used across industries with strict regulatory oversight, such as pharmaceuticals, medical devices, manufacturing, aerospace, and food and beverage.
1. Definition and Purpose of CAPA Software
- Digital Platform for CAPA Management:
- Centralized system to record, analyze, and resolve nonconformities.
- Automates the lifecycle of corrective and preventive actions.
- Primary Goals:
- Ensure consistent resolution of quality issues.
- Prevent recurrence or occurrence of defects and noncompliance.
- Enable compliance with regulatory frameworks like FDA 21 CFR Part 820, ISO 13485, GMP, and ISO 9001.
2. Key Functionalities of CAPA Software
Function | Description |
---|---|
Issue Identification & Logging | Capture nonconformances, deviations, audit findings, or complaints. |
Root Cause Analysis Tools | Integrated tools like 5 Whys, Fishbone diagrams, or Fault Tree Analysis. |
Action Plan Development | Assign tasks, deadlines, and owners for corrective and preventive actions. |
Workflow Automation | Automate approvals, escalations, and task assignments. |
Document Control Integration | Link CAPA to controlled procedures and policies. |
Compliance Management | Ensure audit trails and documentation for FDA, ISO, and GMP inspections. |
Verification of Effectiveness | Monitor and validate whether actions taken were successful. |
Real-Time Dashboards & Reports | Visualize KPIs, overdue actions, trends, and audit readiness. |
3. How CAPA Software Works: Step-by-Step Workflow
A[Issue Identified] --> B[Record Issue in CAPA System]
B --> C[Initiate Investigation]
C --> D[Root Cause Analysis]
D --> E[Define CAPA Plan]
E --> F[Implement Actions]
F --> G[Verify Effectiveness]
G --> H[Close CAPA Record]
H --> I[Audit Trail Archived]
4. Common Triggers Managed by CAPA Software
- Internal Audit Findings
- Customer Complaints
- Nonconformance Reports (NCRs)
- Supplier Quality Issues
- Deviations or Process Failures
- Regulatory Inspections
5. Real-World Use Cases of CAPA Software
- Pharmaceutical Manufacturing:
- A batch deviation triggers a CAPA. The system automates investigation, links it to deviation reports, and tracks action items across departments.
- Medical Device Company:
- An FDA audit results in 483 observations. CAPA software helps assign owners, track timelines, and produce digital evidence of corrective actions.
- Automotive Industry:
- A defect reported by a dealership triggers a CAPA linked to supplier quality. The software integrates with supplier portals to ensure closed-loop communication.
6. Benefits of Using CAPA Software
- Operational Efficiency
- Eliminates paper-based processes and redundant manual tracking.
- Accelerates resolution timeframes and reduces downtime.
- Regulatory Compliance
- Creates complete and audit-ready documentation trails.
- Supports Part 11 e-signatures, role-based access, and electronic approvals.
- Visibility and Control
- Enables management to view open CAPAs, overdue tasks, and trending issues.
- Prioritizes high-risk CAPAs with severity scoring and escalation.
- Risk Reduction
- Proactively prevents recurrence or future failures.
- Informs strategic improvements using historical CAPA data.
7. CAPA Software vs. Traditional CAPA Methods
Feature/Aspect | Manual (Traditional) CAPA | CAPA Software |
---|---|---|
Recordkeeping | Paper-based or Excel spreadsheets | Centralized digital system |
Workflow Management | Manual routing and follow-ups | Automated notifications and escalation |
Audit Readiness | Hardcopy documentation, hard to access | Electronic audit trails and traceability |
Data Analytics | Limited or unavailable | Built-in dashboards and root cause trend analysis |
Collaboration | Departmental silos | Cross-functional integration and visibility |
Compliance Monitoring | Prone to gaps or missed deadlines | Real-time tracking and alerts |
8. Common Modules Integrated with CAPA Software
Module | Description |
---|---|
Nonconformance Management | Directly links CAPA records to related NCRs or deviations. |
Document Control | Ensures that CAPAs reference current SOPs, policies, or training documents. |
Audit Management | Automatically generates CAPAs from internal or external audit findings. |
Training Management | Triggers training for personnel involved in new or revised processes. |
Risk Management | Assesses risk level of CAPAs to prioritize resources accordingly. |
9. Industries That Benefit Most from CAPA Software
Industry | Regulatory Drivers | Example Use Cases |
---|---|---|
Pharmaceuticals | FDA, GxP, EMA, ICH | CAPA for batch deviations and stability test failures |
Medical Devices | FDA 21 CFR 820, ISO 13485 | CAPA post-market surveillance and complaint handling |
Food & Beverage | FSMA, HACCP, GFSI | CAPA for allergen control or contamination response |
Aerospace & Defense | AS9100, ITAR, FAA regulations | CAPA for supplier nonconformances and audit findings |
Automotive | IATF 16949, AIAG Core Tools | CAPA for warranty claims and design process flaws |
Manufacturing | ISO 9001, Lean Six Sigma | CAPA for production downtime and equipment defects |
10. CAPA Software Features Comparison Matrix
Feature | Entry-Level Systems | Mid-Market Systems | Enterprise-Level Systems |
---|---|---|---|
Workflow Automation | Basic | Advanced | Highly configurable |
Root Cause Analysis Tools | Manual Input | Built-in Tools | AI-assisted recommendations |
Integration with QMS | Limited | Partial integration | Full end-to-end QMS integration |
Compliance Support | Minimal | FDA/ISO templates | Comprehensive audit-readiness |
Real-Time Reporting | Manual exports | Scheduled reports | Live dashboards with KPIs |
Scalability | Single site | Regional operations | Multi-site, global deployments |
Training & Support | Community support | Vendor email/chat | Dedicated account management |
11. CAPA Software Adoption Considerations
- Scalability:
Choose systems that can grow with your operations, from local teams to global compliance needs. - Ease of Use:
Systems should have intuitive interfaces to encourage user adoption and reduce training time. - Regulatory Fit:
Ensure the software supports relevant industry standards (FDA, ISO, GxP, etc.). - Integration Capabilities:
Select tools that integrate well with ERP, MES, LIMS, and other enterprise platforms. - Customization & Automation:
Look for flexible workflow engines that allow process customization based on your internal SOPs.
12. Conclusion: The Strategic Value of CAPA Software
CAPA software is more than just a digital recordkeeping tool—it’s a core enabler of regulatory compliance, risk management, and operational excellence. By automating and standardizing the CAPA process, organizations can not only ensure faster issue resolution but also foster a culture of proactive quality improvement. From root cause analysis to post-action verification, CAPA software brings transparency, accountability, and efficiency to the heart of quality management systems.
3. Key Features of CAPA Software
CAPA software is designed to streamline, automate, and improve the effectiveness of Corrective and Preventive Action (CAPA) processes within a Quality Management System (QMS). The best CAPA solutions offer a comprehensive suite of features that support everything from issue detection to root cause analysis, action planning, tracking, and verification of effectiveness—all while maintaining full traceability and regulatory compliance.
Below is a detailed breakdown of the key features you should expect in modern CAPA software, supported by practical examples, comparison matrices, and integration insights.
1. Centralized CAPA Management Dashboard
- Unified control center for tracking all open, in-progress, and closed CAPA records.
- Visual indicators such as status bars, progress trackers, and overdue alerts.
- Customizable dashboards to prioritize actions based on severity or risk.
Example Use Case:
A quality manager at a medical device company uses a centralized dashboard to monitor CAPAs generated from supplier audits, product complaints, and internal deviations—streamlining visibility and team coordination.
2. Automated Workflow Engine
- Pre-configured templates to define process stages and approval flows.
- Role-based assignments ensure tasks go to the correct individuals or departments.
- Automated reminders and escalations for overdue actions and reviews.
mermaidCopyEditgraph TD
A[CAPA Initiation] --> B[Root Cause Assignment]
B --> C[Corrective Action Approval]
C --> D[Implementation]
D --> E[Effectiveness Review]
E --> F[Closure and Archival]
Example Benefit:
Reduces administrative burden and eliminates bottlenecks often caused by manual handoffs.
3. Root Cause Analysis Tools
- Built-in RCA tools such as:
- 5 Whys Analysis
- Ishikawa (Fishbone) Diagrams
- Fault Tree Analysis (FTA)
- Pareto Analysis
- Collaborative investigation tools to gather evidence, interviews, and linked documents.
Table: Comparison of Root Cause Analysis Methods
Method | Best For | Complexity Level | Automation Support |
---|---|---|---|
5 Whys | Simple causes of human/process error | Low | Full |
Fishbone Diagram | Visualizing multi-factor problems | Medium | Partial |
Fault Tree Analysis | Analyzing technical/system failures | High | Limited |
Pareto Analysis | Prioritizing high-frequency issues | Medium | Full |
4. Corrective and Preventive Action Planning
- Pre-defined action templates for recurring issues.
- Customizable task lists with deadlines, dependencies, and linked documents.
- Risk-based prioritization using severity/probability scoring.
Example:
A pharmaceutical company uses risk scoring to prioritize CAPAs tied to product contamination higher than packaging errors.
5. Integration with Other QMS Modules
- Nonconformance Management: Auto-generate CAPAs from NCRs.
- Audit Management: Link audit findings to CAPA records.
- Document Control: Attach revised SOPs, training docs, or specifications.
- Training Management: Assign training as part of corrective/preventive action.
Integration Matrix:
QMS Module | CAPA Integration Functionality |
---|---|
Nonconformance | Direct CAPA launch from NCRs |
Audit Management | Trigger CAPA from audit findings |
Document Control | Link CAPAs to SOP updates and revision control |
Risk Management | Assign risk scores and classify by impact |
Training Management | Assign training tasks post-CAPA implementation |
6. Real-Time Reporting & Analytics
- Customizable reporting tools with charts, graphs, and KPIs.
- CAPA effectiveness metrics: Time to close, number of escalations, recurrence rate.
- Exportable reports for audits and compliance reviews.
7. Regulatory Compliance Support
- Audit trail functionality that records every action taken with timestamp and user ID.
- e-Signature capabilities to comply with FDA 21 CFR Part 11.
- Pre-configured compliance workflows for ISO 9001, ISO 13485, FDA, and GMP.
Key Compliance Features Checklist:
Feature | Required By | Available in Modern CAPA Software |
---|---|---|
Audit Trails | FDA, ISO | ✅ |
Electronic Signatures | FDA 21 CFR | ✅ |
Role-Based Access Control | ISO 27001 | ✅ |
Version Control of Documents | ISO, GMP | ✅ |
CAPA Effectiveness Verification | All | ✅ |
8. Mobile and Cloud Accessibility
- Cloud-based access for remote teams or multi-site facilities.
- Mobile apps or web-responsive UI to approve or review CAPAs on the go.
- Offline data capture in manufacturing or lab environments.
Example Use Case:
A field quality engineer logs a product issue on a mobile tablet, initiating a CAPA that syncs with the central system once online.
9. Risk Assessment and Prioritization Engine
- Built-in risk matrix to classify CAPAs based on likelihood and impact.
- Automatic severity scoring based on input data.
- Thresholds and filters to flag high-risk CAPAs for immediate attention.
Risk Matrix Example:
Impact \ Likelihood | Low | Medium | High |
---|---|---|---|
Low | Low | Low | Medium |
Medium | Low | Medium | High |
High | Medium | High | Critical |
10. Effectiveness Review & CAPA Closure Validation
- Scheduled follow-up checks post-implementation.
- Quantitative and qualitative validations to confirm issue resolution.
- Final approval workflows for full CAPA closure.
Example Tasks:
- Conduct re-inspection of affected process.
- Validate via trend data (e.g., complaints decreased by X%).
- Update SOPs or preventive controls accordingly.
11. Multilingual and Multi-Site Capability
- Global enterprise support with multi-language UIs.
- Location-based access controls and reporting.
- Multi-site CAPA comparison and trend analysis.
Example:
A multinational food manufacturing company uses one CAPA platform across five countries to enforce standard procedures and reporting templates.
12. User Roles, Permissions, and Access Control
- Granular role-based permissions to ensure only authorized users can:
- Initiate CAPAs
- Approve actions
- Access sensitive documents
- Audit-compliant access logs for each user activity.
User Role Table:
User Role | Permissions |
---|---|
Quality Manager | Full access, approve CAPAs, configure templates |
Auditor | Read-only access, generate audit trail reports |
Process Owner | Create/track CAPAs, update root cause analysis |
CAPA Approver | Review/approve implementation plans and effectiveness reviews |
IT Administrator | Manage user roles, integrations, and system backups |
Conclusion: Why These Features Matter
The key features of CAPA software are what empower organizations to move beyond reactive problem-solving and toward predictive, data-driven quality management. From automated workflows and root cause analysis to real-time dashboards and regulatory compliance tools, each feature plays a critical role in transforming how companies handle quality issues. Selecting a CAPA solution that integrates these functionalities not only enhances operational efficiency but also ensures the company remains audit-ready, customer-focused, and compliance-driven at every stage.
4. How CAPA Software Works
Corrective and Preventive Action (CAPA) software is a powerful digital tool that automates the end-to-end process of identifying, addressing, and preventing quality issues in compliance-driven industries. It transforms traditionally manual, paper-based workflows into a streamlined and traceable digital system—ensuring efficiency, accountability, and audit readiness.
Understanding how CAPA software works requires a deep dive into its step-by-step operational workflow, along with the underlying logic, automation layers, and quality control loops it facilitates.
1. Overview of the CAPA Software Workflow
The CAPA software operates through a series of logical steps that form a closed-loop system. Each stage ensures traceability, timely task execution, collaboration, and compliance documentation.
mermaidCopyEditflowchart TD
A[Issue Detection] --> B[Initiation of CAPA Request]
B --> C[Investigation and Root Cause Analysis]
C --> D[Action Plan Development]
D --> E[Implementation of Actions]
E --> F[Effectiveness Verification]
F --> G[Closure and Documentation]
2. Step-by-Step Breakdown of the CAPA Process in Software
Step 1: Issue Detection and Logging
- Sources of Input:
- Nonconformances
- Internal/External Audit Findings
- Customer Complaints
- Regulatory Inspections
- Risk Assessments
- System Functions:
- Automated CAPA creation from linked modules (e.g., NCRs or audit systems)
- Categorization of issues based on severity, recurrence, or risk level
- Assignment of CAPA ID and case owner
Example:
A pharmaceutical firm’s internal audit flags deviation in temperature logs. The system automatically initiates a CAPA request with linked deviation details and auditor remarks.
Step 2: Initiation of CAPA Request
- Data Entry Fields:
- Problem description
- Source of issue
- Product/process impact
- Date of occurrence
- Relevant documents and batch IDs
- Initial Review Gate:
- System-based routing to quality assurance or CAPA coordinator for review and approval
- Automation Features:
- Pre-configured templates for different CAPA types (e.g., product-related, process-related)
Step 3: Investigation and Root Cause Analysis
- Analysis Tools Integration:
- 5 Whys Method
- Fishbone (Ishikawa) Diagram
- Fault Tree Analysis
- FMEA (Failure Mode and Effects Analysis)
- Collaboration Capabilities:
- Role-based collaboration among quality, engineering, compliance, and production teams
- Comment threads and versioned investigative logs
Table: Root Cause Analysis Tool Selection Matrix
Issue Type | Recommended Tool | Reason |
---|---|---|
Process Deviation | 5 Whys + Fishbone Diagram | Quick to apply, effective in root categorization |
Product Design Failure | Fault Tree Analysis | Explores system interdependencies |
Equipment Malfunction | FMEA | Identifies failure modes and impact severity |
Human Error | 5 Whys | Pinpoints training or SOP gaps |
Step 4: Action Plan Development
- Corrective and Preventive Actions Defined:
- Assign owners and due dates
- Link to relevant SOPs, work instructions, or training requirements
- Prioritization Logic:
- Risk matrix scoring based on likelihood and impact
- Escalation workflows for critical CAPAs
Risk Priority Matrix
Impact \ Likelihood | Low | Medium | High |
---|---|---|---|
Low | Low | Medium | Medium |
Medium | Medium | High | High |
High | Medium | High | Critical |
Example:
A recurring supplier defect leads to a CAPA with corrective actions for supplier requalification and preventive actions involving revised incoming inspection protocols.
Step 5: Implementation of Actions
- Workflow Automation:
- Tasks are auto-assigned with notifications, SLAs, and escalation alerts
- Linked training modules or SOP updates are triggered automatically
- Progress Tracking:
- Real-time status monitoring of each action item
- Dependency mapping to ensure sequential task execution
Example:
In a food production plant, the system assigns tasks to engineering for equipment calibration and to quality for revising HACCP documentation.
Step 6: Effectiveness Review and Monitoring
- Verification Mechanisms:
- User-defined criteria for effectiveness validation (e.g., zero recurrence in 3 months)
- Automated follow-up reminders and review scheduling
- Quantitative and Qualitative Data Sources:
- Complaint volume before/after CAPA
- Audit results
- Yield/rework trends
Step 7: CAPA Closure and Archiving
- Closure Validation:
- Final review by QA or designated authority
- Verification that all tasks are completed and documented
- Documentation and Reporting:
- Auto-generated CAPA report with all audit trails
- Archival in centralized repository for audit readiness
- Regulatory Audit-Readiness:
- Complies with FDA 21 CFR Part 11 (e-signatures)
- Includes linked files: investigation results, risk assessments, training logs
3. CAPA Workflow Comparison: Manual vs. Automated
Feature | Manual CAPA Process | Automated CAPA Software |
---|---|---|
Task Assignment | Manual emails or verbal requests | Role-based auto-routing and notifications |
Root Cause Analysis | Hand-drawn diagrams | Interactive, built-in tools |
Action Monitoring | Excel sheets | Real-time dashboards |
Effectiveness Review | Subjective checks | Data-driven validation workflows |
Audit Trails | Paper-based | Secure, time-stamped digital logs |
Document Linkage | Manual attachments | Version-controlled integration |
Closure & Approval | Hand signatures | Digital workflows with e-signature compliance |
4. Cross-Module Integration and Data Flow
Example Data Flow Diagram:
A[Nonconformance] --> B[CAPA Initiation]
B --> C[Investigation Module]
C --> D[Document Control]
C --> E[Training Module]
D --> F[CAPA Implementation]
E --> F
F --> G[Audit Management]
G --> H[CAPA Reporting]
- Integrated Modules:
- Audit Management
- Document Control
- Training Records
- Risk Assessments
- Complaint Management
5. CAPA Notifications and User Engagement
- Automated Email Alerts:
- Task assignment
- Due date reminders
- Escalations for overdue items
- In-App Alerts:
- Role-specific dashboards showing pending CAPAs
- Graphical heatmaps for high-risk items
Example:
A CAPA overdue more than 10 days is flagged with red color on the dashboard and automatically escalated to management.
6. Output Reports and KPIs for Quality Monitoring
Common KPIs Tracked:
KPI | Description |
---|---|
Average CAPA Closure Time | Time taken from initiation to closure |
% Overdue CAPAs | Percentage of CAPAs not closed by due date |
Recurrence Rate | Incidence of repeated issues post-CAPA |
CAPA Effectiveness Success Rate | Verified successful CAPAs vs total closed |
Compliance Readiness Score | % of CAPAs with full documentation and audit trails |
Example Dashboard Widgets:
- Pie chart of CAPAs by status (Open, In Progress, Closed)
- Bar graph of CAPAs by department
- Line graph of average CAPA resolution time over quarters
Conclusion: How CAPA Software Streamlines Compliance and Quality
The operational workflow of CAPA software ensures that each step of the Corrective and Preventive Action process is executed with precision, accountability, and compliance in mind. From initial detection to final closure and audit reporting, the software brings structure, speed, and scalability to organizations operating in complex regulatory environments. By automating workflows, integrating cross-functional data, and embedding analytics, CAPA software enables companies to reduce risk, prevent recurrence, and drive continuous quality improvement.
5. Benefits of Using CAPA Software
Implementing CAPA (Corrective and Preventive Action) software delivers transformative benefits across compliance, quality assurance, productivity, and organizational risk management. By replacing manual systems with digital automation, companies can streamline the full lifecycle of corrective and preventive actions, ensure accountability, and achieve sustainable quality improvements.
1. Enhanced Efficiency and Automation
- Automated Task Assignment and Tracking
- Automatically assigns tasks based on workflows and roles
- Sends email alerts and in-app reminders to prevent delays
- Tracks progress across all action items in real time
- Workflow Standardization
- Ensures uniform processes across departments or global teams
- Reduces time spent manually updating or routing documents
- Faster Issue Resolution
- Eliminates delays from manual investigation or routing
- Accelerates corrective action implementation timelines
Efficiency Impact Matrix
Task Type | Manual CAPA Time (Avg) | With CAPA Software | Time Saved |
---|---|---|---|
Task Assignment | 30 mins | 5 mins | 83% |
Root Cause Documentation | 1 hour | 20 mins | 67% |
Status Reporting Compilation | 3 hours/week | Instant dashboards | 100% |
Closure Approval & Verification | 2 days | 4 hours | 92% |
2. Improved Compliance and Audit Readiness
- Built-In Regulatory Frameworks
- Aligns with ISO 9001, ISO 13485, FDA 21 CFR Part 820, GxP, etc.
- Provides templates and workflow controls tailored to industry standards
- Real-Time Audit Trails
- Captures every change, comment, approval, and timestamp
- Provides full transparency for internal or regulatory audits
- Documented CAPA Lifecycle
- Every phase from issue identification to effectiveness review is stored and searchable
Audit Readiness Chart
A[CAPA Initiation] --> B[Root Cause Analysis]
B --> C[Corrective Action Plan]
C --> D[Preventive Action Plan]
D --> E[Implementation & Monitoring]
E --> F[Effectiveness Check]
F --> G[Audit Trail & Reports]
3. Data-Driven Decision Making
- Advanced Reporting & Dashboards
- Visual KPIs (e.g., open CAPAs, overdue actions, recurrence rates)
- Filter by location, root cause, department, issue type, etc.
- Trend Analysis
- Detect patterns in recurring issues
- Identify systemic weaknesses to prioritize preventive strategies
- Root Cause Insights
- Data clustering identifies high-risk areas and common failures
- Supports continuous quality improvement (CQI) initiatives
Sample KPI Dashboard
KPI Metric | Value | Trend | Target |
---|---|---|---|
Open CAPA Cases | 42 | Decreasing | < 30 |
Average Time to Closure (Days) | 12.7 | Improving | < 10 |
Recurrence Rate (Last 6 Months) | 6% | Stable | < 5% |
Most Common Root Cause Category | Training | ↑ | – |
4. Increased Collaboration and Accountability
- Role-Based Access and Responsibilities
- Ensures only authorized personnel can initiate, edit, or approve CAPAs
- Creates clarity on ownership at each stage
- Team Collaboration Tools
- In-app commenting, file attachments, and chat integrations
- Promotes cross-functional input and buy-in
- Escalation Workflows
- Automatically escalates overdue or stalled actions to supervisors
Responsibility Matrix (RACI Chart Sample)
CAPA Activity | QA Manager | Process Owner | Compliance Officer | IT Admin |
---|---|---|---|---|
Initiate CAPA | A | R | C | – |
Investigate Root Cause | R | A | C | – |
Approve Action Plans | C | A | R | – |
Implement Actions | – | A | – | R |
Verify Effectiveness | A | R | C | – |
Legend: R = Responsible, A = Accountable, C = Consulted
5. Reduced Operational Risk and Cost
- Fewer Product Recalls and Nonconformances
- Preventive actions reduce chances of recurring quality issues
- Reduces penalties or brand damage due to compliance failures
- Improved Supplier Quality
- CAPA software can extend to supplier-related issues
- Strengthens vendor accountability through measurable data
- Decreased Cost of Poor Quality (COPQ)
- Tracks and mitigates quality-related financial losses
Cost Impact Table
Impact Area | Estimated Annual Savings with CAPA Software |
---|---|
Recalls and Product Returns | $50,000 – $500,000 |
Audit Failure Penalties | $100,000+ |
Staff Time Saved | 30–50% reduction |
Cost of Paper-based Management | Eliminated |
6. Scalability and Integration with Other Systems
- Modular and Scalable Design
- Easily add users, processes, and regions as your organization grows
- Integration with QMS, ERP, and MES
- Syncs data with quality modules, inventory, manufacturing, and document control
- Multi-Language and Multi-Site Support
- Ideal for global enterprises or regulated industries with complex structures
7. Real-World Benefits: Use Case Examples
- Life Sciences Company (FDA-Regulated)
- Reduced CAPA closure time by 48%
- Improved audit outcomes with full traceability
- Automotive Manufacturer
- Lowered recurrence rate of defects by 63%
- Integrated CAPA with supplier portal for issue tracking
- Food Processing Company
- Moved from spreadsheet-based tracking to automated software
- Reduced nonconformance backlog by over 70%
Conclusion
CAPA software is more than a compliance tool—it is a strategic enabler for quality transformation. It reduces human error, accelerates resolution timelines, ensures compliance, and creates a centralized system of truth for managing quality events. Organizations that adopt CAPA software gain measurable improvements in productivity, customer satisfaction, and operational resilience. In highly regulated or risk-sensitive industries, it can be the difference between passing and failing an audit, retaining or losing certifications, or staying competitive in global markets.
6. Common Use Cases and Real-World Applications
Corrective and Preventive Action (CAPA) software is widely adopted across regulated and quality-sensitive industries to ensure consistent product quality, reduce nonconformances, maintain compliance, and drive continuous improvement. This section explores the most prevalent use cases and real-world applications of CAPA systems, with illustrative examples, industry-specific insights, and practical matrices.
1. Quality Management and Nonconformance Handling
Use Case Highlights:
- Nonconformance Event Management
- Automatically captures deviations, out-of-spec results, or customer complaints
- Links each nonconformance to appropriate CAPA workflows
- Audit Findings Follow-Up
- Tracks issues raised during internal, supplier, or regulatory audits
- Assigns ownership and corrective actions with full traceability
- Quality Control Escalation
- Converts inspection failures into CAPA records
- Ensures root cause investigation and preventive planning
Real-World Example:
- Medical Device Manufacturer
- Detected 12% increase in batch failure due to supplier defect
- Used CAPA software to trace the issue, enforce requalification, and issue supplier CAPA
- Resulted in a 35% drop in supplier-related defects over the next 6 months
Industry Matrix: Quality Use Cases
Industry | Common Quality Triggers | CAPA Application |
---|---|---|
Pharmaceuticals | Batch deviations, OOS/OOT results | GMP CAPA integration with LIMS and QMS |
Automotive | Line defects, customer complaints | CAPA linked to SPC and supplier scorecards |
Electronics | Component failure, test failure | Embedded CAPA within testing lifecycle |
2. Regulatory Compliance and Audit Management
Use Case Highlights:
- Compliance with ISO, FDA, EU MDR, GAMP
- Automates CAPA workflows aligned with specific regulatory requirements
- Captures objective evidence for each regulatory clause
- Inspection and Audit Observations
- Quickly respond to 483 observations or audit nonconformances
- Assign actions and track effectiveness with timestamps
- Documentation and Traceability
- Maintains audit-ready electronic records
- Supports e-signatures and document version control
Real-World Example:
- Biotech Firm (FDA Regulated)
- Faced warning letter due to inadequate CAPA documentation
- Implemented CAPA software with compliance templates
- Closed regulatory gaps and passed follow-up inspection with zero findings
Audit Lifecycle CAPA Flow (GxP-focused):
A[Audit Observation] --> B[CAPA Initiation]
B --> C[Root Cause Analysis]
C --> D[Corrective Action Planning]
D --> E[Preventive Action Execution]
E --> F[Effectiveness Review]
F --> G[Audit Trail Archiving]
3. Supplier Management and External Quality Issues
Use Case Highlights:
- Supplier Nonconformance Reporting
- Initiates CAPA when supplier product fails inspection
- Enables secure collaboration with suppliers via portals
- Vendor Performance Monitoring
- Tracks recurring supplier issues and trends over time
- Creates preventive actions for high-risk vendors
- Third-Party Audit Follow-Ups
- Ensures external partners close out CAPAs after audit findings
Real-World Example:
- Global Food Manufacturer
- Experienced repeated contamination issues from packaging supplier
- Used CAPA software to implement supplier re-certification and training plans
- Decreased packaging defects by 70% within a quarter
Supplier CAPA Matrix:
Trigger Type | CAPA Action | Follow-up Metric |
---|---|---|
Failed incoming inspection | Issue CAPA and update inspection SOP | Supplier defect trend (monthly) |
Late delivery impact | Implement logistic monitoring CAPA | On-time delivery improvement (%) |
Audit noncompliance | Issue mandatory training CAPA | Audit closure time (days) |
4. Product Safety, Recalls, and Risk Mitigation
Use Case Highlights:
- Post-Market Surveillance (PMS) Integration
- Automates CAPA for adverse event reports or product complaints
- Ensures actions are taken before market withdrawal is required
- Product Recall CAPAs
- Assigns tasks related to root cause investigation and containment
- Documents effectiveness checks before resumption of sales
- Risk-Based CAPA Prioritization
- Uses severity and probability ratings to escalate high-risk issues
Real-World Example:
- Consumer Electronics Brand
- Product overheating complaints triggered a CAPA
- Identified flawed thermal paste from third-party supplier
- CAPA closed with supplier switch, saving $2M in potential recall costs
Risk-Based CAPA Prioritization Matrix:
Severity | Probability | Risk Score | Priority Level | CAPA Timeline |
---|---|---|---|---|
High | High | 9 | Critical | < 48 hours |
Medium | High | 6 | High | < 5 days |
Medium | Medium | 4 | Moderate | < 10 days |
Low | Low | 1 | Low | < 30 days |
5. Training and Competency Management
Use Case Highlights:
- CAPA from Training Gaps
- Initiates CAPAs when training deficiencies lead to quality issues
- Tracking Employee Retraining
- Automates assignments of re-training following CAPA closures
- Linking CAPAs to SOP Updates
- Ensures procedural changes are communicated and enforced
Real-World Example:
- Chemical Manufacturer
- Safety incident traced to lack of updated SOP training
- CAPA triggered employee re-certification across 3 locations
- Compliance score increased by 25% in the next internal audit
CAPA-Training Linkage Table:
Trigger Event | CAPA Action | Training Follow-Up |
---|---|---|
SOP deviation | Revise SOP, assign retraining | LMS integration for auto-tracking |
Audit training finding | Identify gaps, update curriculum | Compliance dashboard alerts |
Safety incident | Root cause: skills gap → retrain team | New certification logged in HRMS |
6. Continuous Improvement and Operational Excellence
Use Case Highlights:
- Lean Six Sigma Integration
- CAPA becomes central to DMAIC and PDCA cycles
- Performance Trend Monitoring
- Highlights recurring inefficiencies or delays
- Actionable Insights for Optimization
- Uses CAPA reports to redesign flawed processes or products
Real-World Example:
- Automotive Plant (Lean Manufacturing)
- Used CAPA data to pinpoint and eliminate root causes of scrap material
- Yield improved by 12%, saving $400K/year
CAPA in DMAIC Cycle:
A[Define] --> B[Measure]
B --> C[Analyze]
C --> D[Improve]
D --> E[Control]
E --> F[Initiate CAPA for Preventive Action]
Conclusion
CAPA software supports a broad spectrum of critical business operations beyond just compliance. Whether addressing internal process flaws, responding to customer complaints, managing supplier performance, or driving proactive improvement, CAPA systems serve as a foundational tool for quality-focused organizations. By enabling visibility, accountability, and systemic resolution across diverse operational areas, CAPA software helps companies minimize risks, boost productivity, and build lasting trust with regulators, partners, and customers alike.
7. Factors to Consider When Choosing CAPA Software
Selecting the right CAPA (Corrective and Preventive Action) software is a critical decision that can directly impact quality performance, compliance readiness, operational efficiency, and risk mitigation. With various vendors offering diverse features, organizations must carefully assess multiple factors to ensure the software meets both current needs and future scalability. Below is a detailed, SEO-optimized, and structured breakdown of key considerations when evaluating CAPA software, along with examples, feature comparison tables, and evaluation matrices.
1. Regulatory Compliance and Industry Standards Alignment
Key Considerations:
- Support for Global Standards
- ISO 9001, ISO 13485, ISO/TS 16949, FDA 21 CFR Part 11, EU MDR, GAMP 5, and ICH Q10
- Electronic Signatures and Audit Trails
- Ensures digital compliance with data integrity and traceability
- Validation-Ready Platform
- Important for regulated industries like pharmaceuticals, biotech, and medical devices
Example:
- A pharmaceutical company using FDA-regulated systems must ensure the CAPA software provides electronic records and e-signatures compliant with 21 CFR Part 11. Non-compliance can result in costly 483 warnings or consent decrees.
Compliance Capability Matrix:
Regulatory Standard | Supported by Software A | Supported by Software B | Supported by Software C |
---|---|---|---|
ISO 9001 | ✅ | ✅ | ✅ |
FDA 21 CFR Part 11 | ✅ | ❌ | ✅ |
EU MDR | ✅ | ✅ | ✅ |
GAMP 5 | ✅ | ❌ | ✅ |
2. Integration Capabilities with Existing Systems
Key Considerations:
- ERP/QMS Integration
- Seamless connection with systems like SAP, Oracle, Microsoft Dynamics, MasterControl
- LIMS and MES Compatibility
- Crucial for laboratory and manufacturing environments
- APIs and Webhooks
- Enables custom workflows and data sharing across tools
Example:
- A biotech firm requires integration with their LIMS to trigger CAPAs automatically from OOS results.
Common Integrations Table:
System Type | Integration Must-Haves | Common Vendors |
---|---|---|
ERP | Two-way data sync | SAP, NetSuite, Oracle |
Document Control System | Version tracking and linkage | Veeva, SharePoint |
CRM/Service Management | Complaint-to-CAPA traceability | Salesforce, Zendesk |
Manufacturing Systems | Real-time defect capture | Siemens, Rockwell |
3. User Interface and Ease of Use
Key Considerations:
- Intuitive Design
- Drag-and-drop workflows, user-friendly dashboards
- Role-Based Access Control
- Customizable views and permissions based on user function
- Mobile Accessibility
- Tablet/mobile support for on-site audits or quality checks
Example:
- In a multi-site automotive manufacturer, shop floor users reported fewer training issues and higher usage when the CAPA system had mobile accessibility and simple navigation.
Usability Evaluation Checklist:
Feature | Importance Level | Example Benefit |
---|---|---|
Dashboard Customization | High | Track open CAPAs by department |
Task Notifications & Reminders | Medium | Automated emails prevent missed deadlines |
Mobile App Support | High | Enables on-the-go audit documentation |
Multilingual Interface | Medium | Supports global teams across regions |
4. Root Cause Analysis and Risk Assessment Tools
Key Considerations:
- Built-In RCA Frameworks
- 5 Whys, Fishbone Diagram, Fault Tree Analysis (FTA)
- FMEA and Risk Prioritization
- Score risks based on severity, occurrence, and detection
- CAPA Effectiveness Checks
- Integrated review tools to ensure corrective actions worked
Example:
- A medical device company uses Fishbone Diagrams to visually map root causes of field complaints. CAPA software with this tool led to faster closure times and stronger preventive measures.
RCA & Risk Management Toolkit Comparison:
RCA Tools Available | Software A | Software B | Software C |
---|---|---|---|
5 Whys | ✅ | ✅ | ✅ |
Fishbone Diagram | ✅ | ❌ | ✅ |
FMEA Risk Matrix | ✅ | ✅ | ❌ |
Effectiveness Review | ✅ | ✅ | ✅ |
5. Workflow Automation and Customization
Key Considerations:
- Custom Workflows by Issue Type
- Tailor CAPA processes based on audit, complaint, deviation, etc.
- Escalation Logic and Routing
- Auto-assign tasks based on department, region, or severity
- SOP Integration
- Link CAPA steps directly to controlled documents
Example:
- A food production company designed separate workflows for packaging issues and contamination incidents, reducing resolution time by 30%.
Custom Workflow Example Diagram:
A[Issue Detection] --> B{CAPA Type}
B --> C1[Audit Finding CAPA]
B --> C2[Customer Complaint CAPA]
C1 --> D1[Root Cause Analysis]
C2 --> D2[Customer Response Action]
D1 & D2 --> E[Preventive Measures]
E --> F[Effectiveness Check]
6. Scalability and Multi-Site Support
Key Considerations:
- Cloud Deployment Options
- SaaS or hybrid models suitable for enterprise scaling
- Global User and Site Management
- Hierarchical structures to manage site-specific CAPAs
- Data Segmentation
- Secure partitioning for regional compliance or team needs
Example:
- A multinational electronics brand deployed CAPA software across 12 sites. The ability to view global trends while managing local actions improved global quality KPIs.
Scalability Evaluation Matrix:
Feature | Single Site | Multi-Site | Global Enterprise |
---|---|---|---|
Centralized Dashboard | ✅ | ✅ | ✅ |
Site-Level Permissions | ❌ | ✅ | ✅ |
Region-Based Reporting | ❌ | ✅ | ✅ |
Multilingual Support | ❌ | ✅ | ✅ |
7. Reporting and Analytics Capabilities
Key Considerations:
- Custom Reports & Dashboards
- Visualize CAPA status, overdue tasks, trends, and recurrence
- Predictive Analytics
- Identify future risks based on historical data
- KPI Tracking
- Track closure times, root cause categories, effectiveness scores
Example:
- A contract manufacturer used trend reports to identify a recurring failure mode in component assembly, enabling preventive redesign.
CAPA Metrics Dashboard Example (KPIs):
KPI | Ideal Benchmark | Actual Performance |
---|---|---|
Avg. Time to Close CAPA | < 15 days | 12.5 days |
% of CAPAs Closed On-Time | > 90% | 95% |
Repeat Issue Rate | < 5% | 2.7% |
Corrective Action Effectiveness | > 85% | 88% |
8. Cost and Licensing Model
Key Considerations:
- Subscription vs. Perpetual Licensing
- SaaS models offer lower upfront cost and automatic updates
- User-Based or Site-Based Pricing
- Choose based on number of users or facilities
- Implementation and Support Fees
- Consider hidden costs in configuration, training, and updates
Cost Consideration Table:
Cost Category | Typical Range | Hidden Costs to Watch For |
---|---|---|
Licensing Fees | $5,000 – $50,000+ | Per user/site charges |
Implementation Services | $3,000 – $25,000 | Customization, validation support |
Ongoing Support & Updates | 15-20% of license | SLA limitations, update frequency |
Conclusion
Choosing CAPA software requires a holistic assessment of regulatory needs, operational complexity, integration readiness, and business growth strategy. By prioritizing compliance features, customization flexibility, analytics depth, and scalability, organizations can adopt a CAPA system that not only meets today’s quality demands but also supports a culture of continuous improvement and long-term excellence. Use structured matrices, comparison charts, and tailored workflows during vendor evaluation to make a data-driven, future-proof decision.
Conclusion
In an era defined by increasing regulatory complexity, customer expectations for quality, and rising operational risks, the importance of a well-executed Corrective and Preventive Action (CAPA) strategy cannot be overstated. CAPA software serves as the digital backbone of that strategy—empowering organizations to move beyond reactive problem-solving and toward a data-driven culture of continuous improvement.
By automating, centralizing, and streamlining the CAPA lifecycle, this software enables quality teams to detect systemic issues earlier, investigate root causes more thoroughly, implement more effective corrective and preventive actions, and ensure long-term compliance with internal policies and external regulations. Whether you’re operating in a highly regulated sector like pharmaceuticals or striving for operational excellence in industrial manufacturing, CAPA software provides the agility, consistency, and audit-readiness needed to thrive in today’s business landscape.
As explored throughout this guide, CAPA software is far more than a digital tool—it’s a strategic enabler that touches every aspect of an organization’s quality management system. From nonconformance handling and document control to training, audits, and risk management, an integrated CAPA platform ensures that quality processes are no longer siloed or disjointed. Instead, they become interconnected, transparent, and action-oriented.
Choosing the right CAPA software solution involves careful consideration of several factors including scalability, ease of use, integration capabilities, regulatory compliance, reporting functionalities, and vendor reputation. Real-world applications across industries—from healthcare and aerospace to consumer goods and electronics—demonstrate how CAPA solutions have been instrumental in preventing costly recalls, reducing compliance risk, and enhancing long-term product quality and customer satisfaction.
Ultimately, organizations that adopt CAPA software gain a competitive advantage not just through regulatory compliance, but through operational resilience, better decision-making, and stronger brand trust. CAPA systems help shift the organizational mindset from firefighting problems to proactively preventing them—making quality and compliance a shared, strategic responsibility rather than an isolated department function.
As you evaluate your organization’s current quality management practices, consider how CAPA software can be leveraged to elevate your processes, protect your brand, and unlock new levels of efficiency. In a global business environment where agility and compliance are paramount, implementing a robust CAPA system is no longer a luxury—it is a necessity for sustained growth and excellence.
If you find this article useful, why not share it with your hiring manager and C-level suite friends and also leave a nice comment below?
We, at the 9cv9 Research Team, strive to bring the latest and most meaningful data, guides, and statistics to your doorstep.
To get access to top-quality guides, click over to 9cv9 Blog.
People Also Ask
What is CAPA software?
CAPA software automates the process of identifying, documenting, and resolving quality issues to ensure compliance and prevent recurrence in regulated industries.
How does CAPA software improve quality management?
It streamlines issue tracking, root cause analysis, action assignment, and effectiveness verification, ensuring faster resolutions and improved compliance.
Which industries benefit most from CAPA software?
Pharmaceuticals, medical devices, manufacturing, automotive, food and beverage, and any regulated industry benefit from CAPA software.
What are the key features of CAPA software?
Key features include issue tracking, root cause analysis tools, automated workflows, document control, reporting dashboards, and audit trail management.
How does CAPA software help with regulatory compliance?
It ensures audit-ready documentation, enforces standard procedures, supports electronic signatures, and aligns with standards like FDA 21 CFR Part 11 and ISO 13485.
Can CAPA software integrate with other systems?
Yes, CAPA software often integrates with ERP, QMS, LIMS, and document management systems for seamless data sharing and process automation.
What is the difference between corrective and preventive actions in CAPA?
Corrective actions address existing problems, while preventive actions target potential issues to avoid future occurrences.
How does CAPA software assist in root cause analysis?
It provides tools like 5 Whys and Fishbone diagrams to systematically investigate and document the root causes of problems.
Is CAPA software suitable for small businesses?
Yes, many CAPA solutions offer scalable features tailored for small and medium businesses to improve quality processes affordably.
How does CAPA software track the effectiveness of actions?
It schedules reviews, monitors metrics, and collects data to verify whether corrective and preventive actions successfully resolved issues.
What role does automation play in CAPA software?
Automation reduces manual tasks, enforces workflows, sends notifications, and escalates overdue actions to improve efficiency and accountability.
Can CAPA software support multi-site operations?
Yes, many CAPA platforms offer multi-site management and multilingual support for global organizations.
How long does it take to implement CAPA software?
Implementation can vary from weeks to months depending on customization, integrations, and training needs.
Does CAPA software support audit preparation?
Yes, it provides detailed, time-stamped audit trails and organizes documentation to facilitate internal and regulatory audits.
What are common challenges CAPA software helps solve?
It tackles delayed issue resolution, poor documentation, lack of root cause analysis, and ineffective preventive measures.
How does CAPA software enhance collaboration?
It offers role-based access, in-app comments, and task assignment features to ensure cross-functional teamwork.
Are cloud-based CAPA software solutions secure?
Reputable cloud CAPA solutions comply with strict security standards, including data encryption and user access controls.
What types of reports does CAPA software generate?
Reports on CAPA status, root cause trends, effectiveness, overdue tasks, and compliance metrics are common.
Can CAPA software reduce the risk of product recalls?
Yes, by proactively managing issues and preventing recurrence, it helps minimize product failures and recalls.
How customizable is CAPA software?
Most platforms allow configuration of workflows, templates, roles, and notifications to match organizational processes.
Does CAPA software include training management?
Some solutions integrate training modules to link CAPA outcomes with employee competency tracking.
Can CAPA software manage supplier-related issues?
Yes, it can track supplier nonconformances and manage related corrective and preventive actions.
How does CAPA software support continuous improvement?
By providing actionable insights and tracking recurring issues, it drives ongoing quality enhancements.
Is mobile access available for CAPA software?
Many modern CAPA solutions offer mobile apps or responsive interfaces for fieldwork and remote access.
What is the typical ROI of implementing CAPA software?
Organizations often see faster issue resolution, reduced compliance risks, and lower operational costs leading to positive ROI.
How does CAPA software handle document control?
It links relevant SOPs and records, maintains version control, and ensures proper documentation is attached to CAPA cases.
Can CAPA software be used for non-regulated industries?
Yes, any industry focused on quality and process improvement can benefit from CAPA software.
What support and training are usually provided with CAPA software?
Vendors typically offer onboarding, user training, ongoing support, and software updates.
How scalable is CAPA software for growing businesses?
Most solutions are designed to scale from small teams to enterprise-wide deployments without losing performance.
What role does data analytics play in CAPA software?
Data analytics helps identify trends, predict risks, and prioritize actions based on historical CAPA data.
How does CAPA software help prevent repeat issues?
By enforcing preventive actions and monitoring effectiveness, it reduces the likelihood of recurring problems.