Key Takeaways
- Chemical manufacturing software automates production processes, ensuring better efficiency, accuracy, and compliance with regulations.
- Key features include batch management, formula optimization, quality control, and real-time data analytics for informed decision-making.
- Implementing the right chemical manufacturing software streamlines operations, reduces costs, and improves overall product quality.
Chemical manufacturing is an intricate and highly regulated industry, where precision, efficiency, and safety are paramount.
As the demand for chemical products continues to grow across various sectors—including pharmaceuticals, agriculture, and industrial manufacturing—companies must leverage advanced technologies to stay competitive and compliant.
This is where chemical manufacturing software comes into play.
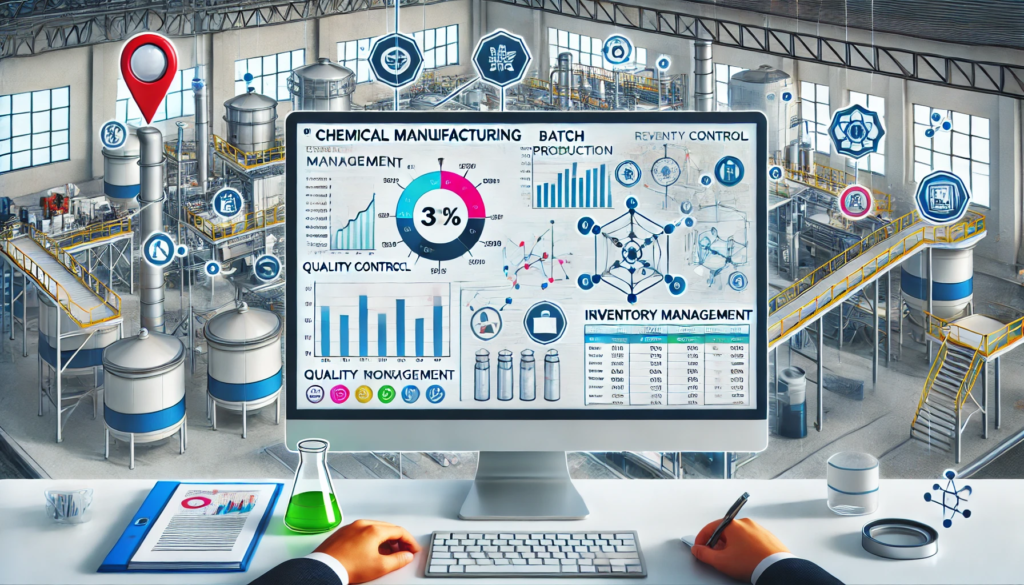
Chemical manufacturing software refers to a suite of digital tools and systems designed to optimize and streamline the entire production process within the chemical industry.
From managing raw material inventories to ensuring quality control, regulatory compliance, and production planning, this software plays a critical role in ensuring that chemical processes are both efficient and safe.
With the complexity of chemical formulations, batch production processes, and the growing need for operational transparency, chemical manufacturing software has become a necessity for modern chemical manufacturers.
In today’s fast-paced, data-driven world, relying on outdated methods or manual processes is no longer a viable option.
Chemical manufacturing software integrates seamlessly with existing systems like enterprise resource planning (ERP) and customer relationship management (CRM) software, facilitating real-time data access, process automation, and greater collaboration across departments.
It empowers manufacturers to track every stage of production, monitor inventory levels, and even predict equipment failures, all of which are essential for maintaining a competitive edge.
But how does chemical manufacturing software work?
At its core, it brings together different functionalities into one comprehensive platform to streamline production processes and improve decision-making.
By automating routine tasks, reducing human error, and offering advanced data analytics, this software helps manufacturers increase productivity, reduce waste, and ensure product consistency—all while maintaining stringent regulatory standards.
Whether it’s managing complex chemical recipes or ensuring that products meet safety standards, chemical manufacturing software provides the tools needed to navigate the complexities of the industry.
In this blog, we will explore the features, benefits, and inner workings of chemical manufacturing software. We will delve into how it enhances production workflows, improves compliance, and supports decision-making at every level of the manufacturing process.
Additionally, we’ll discuss the latest trends in the field and how chemical manufacturing software continues to evolve to meet the challenges of the modern chemical industry.
Understanding the ins and outs of this software is crucial for any organization looking to optimize its operations, reduce costs, and stay ahead in a highly competitive market.
Before we venture further into this article, we would like to share who we are and what we do.
About 9cv9
9cv9 is a business tech startup based in Singapore and Asia, with a strong presence all over the world.
With over nine years of startup and business experience, and being highly involved in connecting with thousands of companies and startups, the 9cv9 team has listed some important learning points in this overview of What is Chemical Manufacturing Software and How It Works.
If your company needs recruitment and headhunting services to hire top-quality employees, you can use 9cv9 headhunting and recruitment services to hire top talents and candidates. Find out more here, or send over an email to [email protected].
Or just post 1 free job posting here at 9cv9 Hiring Portal in under 10 minutes.
What is Chemical Manufacturing Software and How It Works
- Understanding the Role of Chemical Manufacturing Software
- Key Features of Chemical Manufacturing Software
- How Chemical Manufacturing Software Works
- Benefits of Using Chemical Manufacturing Software
- Choosing the Right Chemical Manufacturing Software
1. Understanding the Role of Chemical Manufacturing Software
Chemical manufacturing software is more than just a tool for automation; it plays an integral role in shaping the operations of a chemical plant. By streamlining various production processes, ensuring regulatory compliance, and enhancing decision-making, this software serves as the backbone of modern chemical production. Below, we explore the key roles chemical manufacturing software plays in transforming and optimizing chemical manufacturing operations.
Streamlining Production Processes
- Automation of Routine Tasks
- Chemical manufacturing software automates repetitive tasks, such as data entry, reporting, and inventory tracking, reducing the need for manual intervention and minimizing the risk of human error.
- Example: In a pharmaceutical manufacturing plant, software can automatically generate reports on batch production, ensuring that all relevant data is captured and filed according to regulatory requirements without manual input.
- Optimizing Workflow Management
- Software allows for seamless coordination between various departments, such as procurement, production, quality control, and logistics, ensuring smooth workflows and avoiding bottlenecks.
- Example: A chemical plant producing industrial chemicals can use manufacturing software to schedule production batches in real-time, ensuring that raw materials are available when needed, production runs smoothly, and delivery schedules are met.
- Real-time Monitoring and Control
- Real-time monitoring features enable managers to oversee chemical production at all times, adjusting parameters and processes as needed to maintain optimal performance.
- Example: In a specialty chemicals factory, the software can monitor temperature, pressure, and other crucial production parameters in real-time, providing operators with instant notifications if something deviates from the set threshold.
Improving Regulatory Compliance
- Tracking Chemical Formulations and Ingredients
- Chemical manufacturing software enables accurate tracking of all ingredients and chemicals used in production, ensuring compliance with industry standards and regulations.
- Example: A chemical manufacturing plant producing cleaning products uses software to track the source, quantity, and chemical makeup of each ingredient in its formulations, ensuring the final product adheres to safety regulations.
- Documenting Compliance and Reporting
- The software ensures that all required documentation, such as certificates of analysis, quality control results, and batch production records, are generated and stored for easy access during audits.
- Example: A food-grade chemical manufacturing plant uses software to automatically generate compliance reports for food safety standards, ensuring that they can be presented easily during inspections.
- Ensuring Environmental and Safety Compliance
- Chemical manufacturing software can assist in ensuring compliance with environmental regulations by tracking waste management, emissions, and energy consumption.
- Example: A chemical plant involved in producing plastics can use software to track hazardous waste generated during production and ensure it is disposed of according to government regulations.
Data Management and Reporting
- Centralized Data Storage
- Chemical manufacturing software consolidates all production-related data into a central repository, allowing for easy access and real-time updates for key stakeholders.
- Example: A petrochemical manufacturer uses the software to store data about each batch of production, including material usage, machine settings, and output levels, making it easier for managers to access this information for analysis or quality checks.
- Data-Driven Decision Making
- By providing in-depth analytics and reporting tools, the software enables managers and executives to make informed decisions based on accurate and up-to-date data.
- Example: A cosmetics chemical manufacturer can use the software’s analytics features to identify trends in production downtime, pinpoint inefficiencies, and implement improvements to boost output and reduce costs.
- Customizable Reporting Tools
- The software allows for customizable reports, which can be tailored to different aspects of the business, such as inventory levels, production yields, or quality control metrics.
- Example: A chemical manufacturer might generate daily, weekly, or monthly production reports to track key performance indicators (KPIs) and ensure consistent performance across the manufacturing plant.
Enhancing Collaboration and Communication
- Cross-Department Collaboration
- Chemical manufacturing software enhances collaboration by ensuring that all departments—production, procurement, quality assurance, and logistics—are working from the same data set and timelines.
- Example: In a large-scale chemical plant, the software ensures that the purchasing department knows exactly when raw materials are required for the next production batch, while the production team can track material deliveries in real-time.
- Improved Communication with Suppliers and Clients
- The software can be integrated with supplier and customer management systems, ensuring that suppliers receive real-time updates about order requirements and that customers are promptly notified of shipping or delivery schedules.
- Example: A chemical distributor using the software can track raw material orders from suppliers and ensure that customers receive up-to-date information about the status of their deliveries, minimizing delays.
Boosting Operational Efficiency
- Inventory Management and Control
- Effective inventory management is one of the critical features of chemical manufacturing software. It tracks stock levels of both raw materials and finished goods, ensuring that production isn’t interrupted due to supply shortages.
- Example: A chemical company producing detergents uses software to manage its raw material inventory, setting automatic reorder levels when certain chemicals, such as surfactants, are running low, thus avoiding production delays.
- Cost Reduction and Waste Minimization
- By providing insights into material usage, waste production, and production efficiency, the software helps companies minimize waste, reduce energy consumption, and optimize resource usage.
- Example: A chemical plant producing fertilizers uses software to monitor chemical reactions closely, reducing the occurrence of wasteful by-products and improving the overall cost efficiency of the manufacturing process.
- Maintenance Management
- Many chemical manufacturing software solutions include predictive maintenance tools that help monitor the health of machinery and equipment, reducing unplanned downtime and extending the lifespan of assets.
- Example: A chemical production plant might use software to monitor the performance of reactors and sensors, scheduling maintenance before a breakdown occurs, ensuring continuous production and reducing repair costs.
Facilitating Scalability and Growth
- Adapting to Changing Demand
- As the market demand for chemical products fluctuates, chemical manufacturing software enables companies to scale operations up or down based on real-time data and forecasts.
- Example: A chemical company that produces industrial adhesives can use the software to adjust production schedules based on a spike in customer orders, quickly ramping up manufacturing capacity while maintaining product quality.
- Expanding Operations Efficiently
- The scalability of chemical manufacturing software allows businesses to grow and expand without overhauling existing systems. New plants, equipment, or production lines can be seamlessly integrated into the system.
- Example: A multinational chemical manufacturer opening a new plant in a different region can integrate its new operations into the same software, allowing for centralized monitoring and management across all locations.
Conclusion
Chemical manufacturing software plays a pivotal role in modernizing production processes, improving compliance, enhancing data management, and fostering operational efficiency. By automating and optimizing key aspects of manufacturing—from inventory management to production workflows—this software ensures that chemical manufacturers can meet the ever-growing demands of the industry while maintaining high standards of quality and safety.
2. Key Features of Chemical Manufacturing Software
Chemical manufacturing software is designed with a variety of features to address the specific needs of the chemical industry, offering tools that support everything from production management to regulatory compliance. By integrating key functionalities, these software solutions help manufacturers streamline operations, reduce costs, and improve quality. Below are the core features of chemical manufacturing software and how they contribute to optimizing the manufacturing process.
Inventory Management
- Tracking Raw Materials and Finished Goods
- Chemical manufacturing software ensures that all raw materials and finished products are tracked in real-time. This helps prevent stockouts and overstocking, which can lead to production delays or unnecessary costs.
- Example: A manufacturer of paint uses the software to track the levels of pigments and other raw materials. The software alerts the procurement team when stocks are low, triggering automatic orders to suppliers to maintain optimal inventory levels.
- Optimizing Stock Levels
- With real-time data, manufacturers can manage inventory more effectively by setting automatic reorder points, thus optimizing stock levels to avoid disruptions in production.
- Example: In a chemical plant producing adhesives, the software calculates optimal stock levels of chemicals based on historical usage data, ensuring that production lines always have the necessary materials while minimizing waste from overstocking.
- Expiration and Shelf-Life Monitoring
- Many chemicals have a limited shelf life, and the software tracks the expiration dates of raw materials and finished products to ensure quality and compliance with industry standards.
- Example: A pharmaceutical manufacturing company uses the software to monitor the expiration dates of active ingredients in its drug formulations, ensuring that expired materials are not used in production.
Batch Control and Recipe Management
- Recipe Formulation and Modification
- Chemical manufacturing software allows for precise recipe formulation and modification, ensuring that each batch of product adheres to specific formulation parameters while enabling flexibility for different batch sizes or custom orders.
- Example: A chemical company that manufactures cleaning agents can use the software to store and retrieve precise recipes for different types of cleaners, adjusting for ingredient availability or customer-specific requirements.
- Batch Scheduling and Tracking
- The software enables efficient batch scheduling and real-time tracking of each batch through the production process, from mixing and chemical reactions to packaging and shipping.
- Example: In the production of industrial coatings, the software schedules production batches, tracks the status of each batch, and adjusts the process flow if there are delays or bottlenecks.
- Ensuring Consistency and Quality
- By maintaining accurate records of each recipe and batch, the software helps ensure that every product produced meets the required quality standards, regardless of variations in batch size or production conditions.
- Example: A company producing synthetic rubber uses the software to ensure each batch has the same chemical composition and properties, maintaining consistent product quality across multiple production runs.
Quality Control and Testing
- Automated Quality Checks
- The software incorporates automated testing tools to perform real-time quality checks throughout the production process. These checks can include temperature, pressure, and chemical composition analysis.
- Example: A chemical plant producing fertilizers uses software to monitor the chemical composition of its products during production. If any deviations from the desired formula are detected, the software automatically triggers an alert for corrective action.
- Real-Time Data Collection
- By collecting real-time data from sensors and equipment throughout the production line, the software helps identify potential quality issues before they become major problems.
- Example: In the production of paints and coatings, sensors integrated with the software continuously measure viscosity and color consistency, allowing operators to make immediate adjustments to ensure product quality.
- Non-Compliance Detection
- Chemical manufacturing software helps quickly identify deviations from quality standards or regulatory non-compliance, ensuring corrective actions are taken swiftly to avoid costly fines or product recalls.
- Example: A pharmaceutical manufacturing facility uses software to automatically flag any deviations from FDA-regulated processes, ensuring that any non-compliant batches are removed from production immediately.
Supply Chain Management
- Optimizing Procurement and Delivery
- By tracking the availability and lead times of raw materials and finished products, chemical manufacturing software helps optimize procurement schedules and ensures timely delivery of materials.
- Example: A specialty chemicals manufacturer uses the software to forecast demand and automate orders to suppliers, ensuring that there are no delays in the production process due to material shortages.
- Supplier Relationship Management
- The software enables better communication with suppliers by tracking order statuses, delivery schedules, and quality control data, enhancing collaboration and efficiency in the supply chain.
- Example: A large chemical company uses the software to maintain close relationships with its suppliers, providing real-time updates on production schedules and material requirements, ensuring timely deliveries.
- Logistics and Distribution Tracking
- Chemical manufacturing software integrates with logistics and distribution systems to track shipments, optimize transportation routes, and improve on-time delivery rates.
- Example: A manufacturer of agricultural chemicals uses software to track shipments of finished products from the plant to distributors, ensuring that the right products are delivered to the right locations on schedule.
Regulatory Compliance and Reporting
- Ensuring Compliance with Industry Regulations
- Chemical manufacturing software is designed to help manufacturers comply with a wide range of local, national, and international regulations, such as REACH, OSHA, and EPA guidelines.
- Example: A company producing cleaning products can use the software to ensure that its formulations meet the requirements of the Environmental Protection Agency (EPA) by tracking the chemical components and their concentrations.
- Automated Reporting for Audits
- The software generates accurate, ready-to-present reports for audits, ensuring that manufacturers remain compliant with regulatory bodies and avoid penalties.
- Example: A chemical manufacturer in the pharmaceutical industry uses software to automatically generate reports on batch production, quality control, and raw material sourcing, ensuring the company is audit-ready at any time.
- Environmental Compliance
- Chemical manufacturing software helps track waste generation, emissions, and energy consumption, facilitating compliance with environmental regulations and minimizing the environmental impact of production activities.
- Example: A plant producing petrochemicals uses the software to monitor emissions and energy usage, generating reports that demonstrate adherence to environmental regulations and helping identify opportunities for sustainability improvements.
Predictive Maintenance
- Monitoring Equipment Health
- Predictive maintenance features in chemical manufacturing software help monitor the health of equipment and machinery, preventing breakdowns and extending the lifespan of assets.
- Example: A chemical manufacturing plant that uses large industrial mixers can use software to monitor vibration levels, temperature, and motor performance, triggering alerts for maintenance when abnormalities are detected before a failure occurs.
- Scheduling Preventative Maintenance
- The software helps schedule routine maintenance activities based on equipment usage, reducing downtime and ensuring that machinery is serviced before it fails.
- Example: A plant that produces chemical solvents uses software to track the operating hours of its reactors and automatically schedules maintenance when necessary to avoid unexpected breakdowns.
User Interfaces and Dashboards
- Customizable Dashboards for Key Metrics
- Chemical manufacturing software provides customizable dashboards that allow users to track key performance indicators (KPIs) such as production efficiency, inventory levels, and quality control metrics.
- Example: A manager at a chemical company can create a dashboard that displays real-time data on production progress, material consumption, and machine performance, enabling quick decision-making and problem-solving.
- User-Friendly Interfaces
- Many software solutions are designed with intuitive user interfaces, ensuring that employees across various departments—whether in production, quality control, or maintenance—can easily navigate and use the software.
- Example: A small chemical manufacturer with limited IT resources can adopt software with an easy-to-use interface, ensuring that operators can quickly learn how to use it to improve efficiency without requiring extensive training.
Conclusion
The key features of chemical manufacturing software enable manufacturers to optimize their operations across various stages of production—from managing inventories and recipes to ensuring regulatory compliance and predictive maintenance. By integrating these features, manufacturers can increase efficiency, reduce costs, and enhance product quality while meeting industry regulations. The right software solution is indispensable for any chemical manufacturing operation aiming to stay competitive in an increasingly complex and demanding industry.
3. How Chemical Manufacturing Software Works
Chemical manufacturing software integrates various systems and processes within a manufacturing plant to streamline production, improve efficiency, and ensure regulatory compliance. The software connects key operations such as inventory management, production scheduling, quality control, and reporting, creating a cohesive and automated workflow. In this section, we will explore how chemical manufacturing software works, its key components, and the processes it supports.
1. Data Integration and Centralized System
- Centralized Data Repository
- Chemical manufacturing software operates as a centralized hub where all production-related data, including raw material inventories, product formulations, and equipment status, are stored and managed in real time.
- Example: A chemical plant producing paints uses the software to centralize data from all departments, including procurement, production, and quality control, to ensure all teams are aligned and have access to the latest information.
- Integration with Existing Systems
- The software seamlessly integrates with other enterprise systems such as Enterprise Resource Planning (ERP), Manufacturing Execution Systems (MES), and Customer Relationship Management (CRM) software.
- Example: A pharmaceutical manufacturer integrates its chemical manufacturing software with its ERP system, enabling real-time updates on inventory levels and order processing, ensuring a smooth flow of operations from production to customer delivery.
2. Raw Material and Inventory Management
- Tracking of Raw Materials
- The software tracks the movement of raw materials from the moment they are received until they are used in production, ensuring that the right materials are available when needed.
- Example: A company producing specialty chemicals uses the software to track the procurement of raw materials, ensuring that chemicals like solvents and catalysts are available for production without delays.
- Automatic Stock Replenishment
- Chemical manufacturing software helps automate stock replenishment by tracking inventory levels and automatically generating purchase orders for raw materials when stock reaches predefined thresholds.
- Example: A chemical plant producing fertilizers uses the software to maintain optimal stock levels of key ingredients like nitrogen and phosphorus. When the inventory reaches the reorder point, the software automatically places an order with the supplier.
- Shelf-Life Management
- The software manages the shelf life of raw materials, ensuring that expired or near-expired chemicals are used or discarded before they compromise product quality.
- Example: In a pharmaceutical plant, the software tracks expiration dates for raw materials such as active pharmaceutical ingredients (APIs) and ensures that only fresh materials are used in production.
3. Recipe Formulation and Production Scheduling
- Recipe Management and Formulation Control
- Chemical manufacturing software allows for the precise formulation of chemical recipes, ensuring that each batch is produced according to strict specifications, including ingredient quantities and mixing parameters.
- Example: A company producing cleaning agents uses the software to manage multiple formulas for different types of cleaners, ensuring that production adheres to each formula’s specifications for optimal performance.
- Batch Scheduling
- The software optimizes production schedules by determining the best time to produce different batches, taking into account factors such as resource availability, machine uptime, and material availability.
- Example: A petrochemical manufacturer uses the software to schedule production runs based on the availability of raw materials like ethylene and propylene, ensuring that the plant operates at full capacity while avoiding downtime.
- Real-Time Production Monitoring
- As production progresses, chemical manufacturing software provides real-time data on each batch’s status, including temperature, pressure, and chemical composition, enabling operators to adjust parameters as needed.
- Example: A paint manufacturer uses sensors connected to the software to monitor the viscosity of the mixture in real-time, making adjustments during production to maintain product quality.
4. Quality Control and Testing
- Automated Quality Checks
- Chemical manufacturing software integrates with quality control systems to automate the testing of products at various stages of production. Parameters such as pH, viscosity, chemical composition, and color are tested automatically, ensuring that each batch meets quality standards.
- Example: A food additive manufacturer uses the software to run automated tests on batches to ensure they meet regulatory and safety standards, such as testing for contaminants like heavy metals or microorganisms.
- Real-Time Data Collection and Alerts
- The software collects real-time data from sensors placed throughout the production process, such as temperature, humidity, or chemical concentration. If the data deviates from predefined limits, alerts are sent to operators, prompting immediate action.
- Example: A chemical company producing adhesives uses the software to monitor the temperature during the curing process. If the temperature exceeds a certain threshold, an alert is triggered to prevent over-curing, which could affect the product’s quality.
- Non-Conformance and Issue Resolution
- The software detects any deviation from the established product specifications (non-conformances) and initiates corrective actions, such as halting production or adjusting parameters to rectify issues.
- Example: A pharmaceutical company producing tablets uses the software to monitor the compression force during tablet formation. If the force is too high or too low, the software automatically adjusts the machine settings or stops production to prevent defective tablets.
5. Regulatory Compliance and Reporting
- Automated Compliance Checks
- Chemical manufacturing software ensures that all production processes comply with industry regulations, including health and safety standards, environmental laws, and product certifications. It automatically checks for compliance with regulations like REACH (Registration, Evaluation, Authorization, and Restriction of Chemicals) or OSHA (Occupational Safety and Health Administration).
- Example: A chemical company manufacturing industrial lubricants uses the software to track chemical ingredients’ compliance with REACH regulations, ensuring that all materials are registered and meet safety requirements.
- Batch Traceability and Reporting
- The software maintains a detailed history of every batch produced, including raw material sourcing, production parameters, and quality control results. This traceability is essential for audits and regulatory compliance.
- Example: A food-grade chemical manufacturer uses the software to trace the origin and processing details of each batch, enabling quick identification of any issues and ensuring compliance with food safety standards.
- Automated Reporting for Audits
- The software generates comprehensive reports on production data, quality checks, inventory levels, and safety protocols, making it easy for manufacturers to prepare for audits and meet regulatory requirements.
- Example: A company producing pharmaceuticals uses the software to generate detailed reports for regulatory bodies like the FDA, including records of raw material batches, production conditions, and quality control testing results.
6. Predictive Maintenance and Equipment Monitoring
- Real-Time Equipment Monitoring
- Chemical manufacturing software integrates with machinery and equipment to monitor their health and performance in real time. It tracks critical factors such as vibration, temperature, and operational hours.
- Example: A chemical plant producing polymer resins uses the software to monitor the condition of reactors. If any abnormality is detected, such as excessive vibration in a mixer, the software sends an alert to the maintenance team.
- Predictive Analytics for Maintenance
- By analyzing historical data, the software predicts when maintenance should be performed to avoid unexpected equipment breakdowns. This minimizes downtime and reduces the need for costly emergency repairs.
- Example: A plant that manufactures solvents uses predictive maintenance features in the software to schedule repairs for distillation columns before they fail, reducing production downtime.
- Scheduling and Maintenance Logs
- The software automatically schedules routine maintenance based on equipment usage and tracks maintenance logs to ensure machines are serviced regularly, preventing unplanned failures.
- Example: A chemical manufacturer producing paints uses the software to schedule regular maintenance for mixing tanks, ensuring they are serviced before production runs to prevent potential malfunctions during manufacturing.
7. Reporting and Data Analytics
- Customizable Dashboards for Key Metrics
- Chemical manufacturing software provides customizable dashboards that display key performance indicators (KPIs) such as production efficiency, inventory status, and equipment performance, helping manufacturers make data-driven decisions.
- Example: A chemical plant producing detergents uses a dashboard that displays real-time data on production progress, energy consumption, and material costs, enabling managers to identify areas for improvement.
- Historical Data Analysis
- The software collects and stores historical data that can be analyzed to identify trends, inefficiencies, and areas of improvement in the manufacturing process.
- Example: A chemical company producing fertilizers uses historical data analytics to analyze production cycles and identify patterns in raw material usage, enabling them to optimize the use of resources and reduce waste.
Conclusion
Chemical manufacturing software works by integrating and automating key aspects of the production process, from raw material tracking to quality control and predictive maintenance. By offering centralized data management, production scheduling, inventory control, and compliance tracking, the software helps manufacturers increase efficiency, improve product quality, and reduce costs. As a result, chemical manufacturers are better equipped to meet regulatory standards, improve operational performance, and maintain a competitive edge in a dynamic industry.
4. Benefits of Using Chemical Manufacturing Software
Chemical manufacturing software offers a wide range of advantages that significantly enhance operational efficiency, streamline production processes, improve regulatory compliance, and reduce operational costs. In this section, we will explore the key benefits of using chemical manufacturing software, providing relevant examples to highlight its value in real-world applications.
1. Improved Operational Efficiency
- Streamlined Production Processes
- Chemical manufacturing software automates many aspects of the production process, reducing the need for manual intervention and minimizing human error. This results in smoother operations and faster production cycles.
- Example: A chemical company producing industrial adhesives uses the software to automate batching, ingredient mixing, and formulation, reducing human error and improving production timelines.
- Optimized Resource Utilization
- The software ensures the efficient use of raw materials, labor, and equipment by providing real-time insights into inventory levels, production schedules, and equipment status.
- Example: A fertilizer manufacturer uses chemical manufacturing software to ensure that the right quantities of raw materials such as nitrogen and phosphorus are used in each production run, avoiding excess inventory or shortages.
- Enhanced Production Scheduling
- By analyzing production demands, equipment availability, and material stock, the software helps optimize production schedules, ensuring that production runs are completed on time without delays.
- Example: A company manufacturing specialty chemicals uses the software to adjust production schedules dynamically, ensuring they meet urgent customer orders without compromising quality or on-time delivery.
2. Cost Savings and Waste Reduction
- Reduced Material Waste
- Chemical manufacturing software helps minimize material waste by accurately tracking inventory, monitoring consumption rates, and forecasting material requirements. This prevents over-ordering and under-utilization of raw materials.
- Example: A company producing paints uses the software to manage the exact quantities of pigments and solvents needed for each batch, reducing waste and lowering raw material costs.
- Energy Efficiency
- The software optimizes energy consumption by monitoring production processes and ensuring equipment runs efficiently, leading to reduced energy usage.
- Example: A petrochemical plant uses the software to track energy consumption across different production lines, identifying areas where energy can be saved without affecting production quality.
- Lower Operational Costs
- By automating routine tasks and improving workflow efficiency, chemical manufacturing software reduces the need for manual labor, lowers operational overheads, and enhances overall cost control.
- Example: A chemical plant producing cleaning agents uses the software to automate inventory management, reducing the need for manual tracking and lowering administrative costs.
3. Enhanced Quality Control and Consistency
- Real-Time Quality Monitoring
- Chemical manufacturing software integrates with quality control systems to provide real-time monitoring of key product parameters such as chemical composition, temperature, pressure, and viscosity. This allows manufacturers to identify potential quality issues early and take corrective action promptly.
- Example: A pharmaceutical manufacturer uses the software to monitor the chemical composition of a batch in real time, ensuring that each batch meets strict regulatory and quality standards.
- Standardized Production Methods
- By using precise recipe formulations and production protocols, chemical manufacturing software ensures that products are consistently produced to the same high standards, reducing variations in product quality.
- Example: A food additive manufacturer relies on the software to manage and maintain standardized formulas, ensuring that every batch of flavor enhancers meets the same strict quality criteria.
- Automated Quality Inspections
- Chemical manufacturing software automates quality checks during production, reducing the risk of human error and ensuring products are tested according to predefined specifications.
- Example: A paint manufacturer uses the software to automatically test each batch for color consistency, viscosity, and chemical stability, ensuring high-quality products with minimal variation.
4. Regulatory Compliance and Traceability
- Easier Compliance with Industry Regulations
- Chemical manufacturing software ensures that all production processes comply with industry standards and government regulations, such as REACH, OSHA, and FDA requirements. It automates documentation and reporting, making it easier to meet regulatory audits.
- Example: A pharmaceutical company uses the software to track the sourcing and testing of raw materials to ensure they comply with FDA regulations for active pharmaceutical ingredients.
- Batch Traceability and Transparency
- The software provides complete traceability of each batch produced, from raw material sourcing to final product distribution. This ensures that any product defects or quality issues can be traced back to their root cause quickly and accurately.
- Example: A chemical manufacturer producing detergents uses the software to track the origin and processing details of each batch, making it easy to identify the source of any product defects and quickly take corrective action.
- Automated Documentation and Reporting
- Chemical manufacturing software automates the generation of regulatory reports, safety documents, and quality control records, significantly reducing the time and effort required to prepare for audits or inspections.
- Example: A company manufacturing agrochemicals uses the software to generate automated compliance reports for environmental regulations, reducing the administrative burden of manual reporting.
5. Increased Productivity and Output
- Faster Production Cycles
- With optimized production scheduling and real-time process monitoring, chemical manufacturing software helps reduce downtime and increase the speed of production, leading to higher output levels.
- Example: A specialty chemical manufacturer uses the software to automate mixing and blending processes, reducing production cycle times and increasing the overall output of the plant.
- Real-Time Performance Data
- The software collects data from various stages of production and presents it on customizable dashboards, allowing managers to make quick, data-driven decisions to improve productivity.
- Example: A chemical company producing lubricants uses real-time performance dashboards to track machine efficiency, operator productivity, and material consumption, identifying potential improvements for faster production.
- Fewer Operational Interruptions
- By tracking and analyzing equipment health and providing predictive maintenance alerts, the software helps prevent unexpected breakdowns, ensuring continuous production.
- Example: A chemical plant producing polymers uses predictive maintenance features in the software to schedule repairs on critical equipment before it breaks down, reducing unplanned downtime and maintaining continuous production.
6. Better Decision-Making and Data-Driven Insights
- Advanced Analytics and Reporting
- Chemical manufacturing software offers advanced analytics tools that help manufacturers interpret data from various production stages, providing actionable insights for decision-making. This helps optimize processes and improve overall performance.
- Example: A company producing adhesives uses the software’s analytics tools to analyze production trends, material costs, and labor utilization, enabling better decision-making about future production strategies.
- Forecasting and Demand Planning
- The software helps manufacturers forecast demand based on historical data, sales trends, and market conditions, allowing them to adjust production plans accordingly and avoid overproduction or stockouts.
- Example: A specialty chemical manufacturer uses demand forecasting tools in the software to predict future production needs, ensuring that production is aligned with market demand.
- Customizable Dashboards and Key Performance Indicators (KPIs)
- Chemical manufacturing software allows managers to create customizable dashboards that track KPIs such as production efficiency, raw material consumption, energy use, and equipment performance. These dashboards provide real-time insights for decision-makers.
- Example: A chemical company producing specialty coatings uses the software to create dashboards that display key metrics such as production speed, raw material cost per unit, and batch yield, helping managers make more informed decisions.
7. Enhanced Collaboration and Communication
- Cross-Departmental Integration
- Chemical manufacturing software integrates various departments within the manufacturing process, such as procurement, production, and quality control. This ensures better communication and collaboration, reducing errors and delays.
- Example: A chemical plant uses the software to synchronize data between the procurement team, who tracks raw material purchases, and the production team, ensuring that production is not delayed due to material shortages.
- Real-Time Communication and Alerts
- The software sends real-time alerts and notifications to relevant departments in case of any issues or delays in the production process, facilitating quick problem resolution.
- Example: A chemical manufacturer producing cleaning products uses real-time alerts to notify the quality control department of any batch deviations, enabling immediate corrective actions.
- Improved Supplier and Customer Relations
- By providing accurate, real-time information about production schedules, material availability, and order fulfillment, chemical manufacturing software enhances communication with suppliers and customers.
- Example: A pharmaceutical manufacturer uses the software to provide customers with real-time updates on the status of their orders, ensuring transparency and improving customer satisfaction.
8. Scalability and Adaptability
- Easily Scalable to Meet Growth
- Chemical manufacturing software is designed to scale with the growth of the business, accommodating increased production volumes, more complex operations, and larger inventories.
- Example: A small chemical manufacturer that produces industrial chemicals for local markets uses the software to scale up its operations as it expands into international markets, easily managing higher production volumes and more complex supply chains.
- Adaptable to Different Manufacturing Needs
- The software is flexible and can be customized to meet the unique needs of different chemical manufacturing sectors, whether producing pharmaceuticals, food chemicals, or industrial solvents.
- Example: A company producing food-grade chemicals customizes its software to track specific regulatory requirements and quality parameters unique to the food industry, ensuring full compliance and quality assurance.
Conclusion
The benefits of using chemical manufacturing software are numerous and impactful, from improving operational efficiency and reducing costs to enhancing product quality and regulatory compliance. By automating key processes such as production scheduling, quality control, and inventory management, chemical manufacturers can optimize their operations, reduce waste, and increase productivity. Additionally, the ability to make data-driven decisions and forecast demand helps manufacturers stay competitive in a fast-evolving industry. As a result, adopting chemical manufacturing software is a strategic investment that enhances overall operational performance and long-term success.
5. Choosing the Right Chemical Manufacturing Software
Choosing the right chemical manufacturing software is a critical decision for any organization. It can significantly affect productivity, regulatory compliance, cost management, and operational efficiency. With so many available solutions, selecting the best software for your business needs requires careful consideration. This section will provide an in-depth guide on the key factors to evaluate when choosing the right chemical manufacturing software for your organization.
1. Understand Your Specific Business Needs
- Assess Operational Requirements
- Different chemical manufacturing businesses have distinct operational needs depending on the type of chemicals they produce (e.g., pharmaceuticals, fertilizers, food chemicals, industrial chemicals). Therefore, it is essential to evaluate your specific business processes and requirements before selecting software.
- Example: A company producing specialty chemicals may prioritize advanced formulation management features, while a pharmaceutical manufacturer might require robust regulatory compliance capabilities.
- Evaluate Production Volume and Complexity
- Consider your production volume and complexity. High-volume producers may need software capable of handling large amounts of data and automating many processes, while smaller companies may need a more streamlined solution.
- Example: A large-scale petrochemical plant needs software capable of managing multiple production lines simultaneously, while a boutique fragrance manufacturer may need a simpler solution focused on batch control and inventory management.
- Customization and Flexibility
- The software should be adaptable to the specific workflows of your business. Many chemical manufacturers have unique processes that require highly customizable software solutions.
- Example: A custom-made solution for a food additive company might require adjustments to address industry-specific needs, like batch testing for flavor consistency and compliance with food safety standards.
2. Key Functional Features
- Batch and Formula Management
- Chemical manufacturing software should support batch production and provide advanced formulation capabilities. This feature allows manufacturers to track the exact ingredients, quantities, and production conditions for each batch.
- Example: A company manufacturing paint needs software that can manage complex formulas for different colors, types, and viscosity levels, ensuring consistency across batches.
- Regulatory Compliance Management
- Choose software that helps you stay compliant with local and international regulations (e.g., FDA, REACH, OSHA). It should help automate the process of generating required reports and storing necessary documentation for audits.
- Example: A pharmaceutical manufacturer needs software with built-in features to ensure compliance with FDA Good Manufacturing Practices (GMP) and the ability to generate compliance reports for each production batch.
- Inventory and Supply Chain Management
- The software should include features to manage raw materials, finished products, and supplier data. It must provide real-time visibility into inventory levels, material needs, and order statuses.
- Example: A fertilizer manufacturer uses software to track the inventory of raw materials like nitrogen and phosphorus and manage purchase orders from suppliers to avoid production delays.
- Quality Control and Assurance
- Ensure the software includes functionality to manage quality control at every stage of production. It should provide tools for real-time monitoring and alerts for quality deviations, as well as post-production testing.
- Example: A medical-grade chemical manufacturer needs software that integrates with quality control systems to monitor temperature, pressure, and chemical concentrations in real time, ensuring that every batch meets stringent health standards.
- Energy and Resource Optimization
- Software with energy management features helps chemical manufacturers track and optimize energy usage, reducing costs and minimizing environmental impact.
- Example: A chemical plant producing solvents may use software to monitor energy consumption across multiple stages of production, adjusting processes to reduce energy waste.
3. Integration Capabilities
- Seamless Integration with Existing Systems
- The right software should easily integrate with your current enterprise systems, including ERP (Enterprise Resource Planning), CRM (Customer Relationship Management), and supply chain management systems.
- Example: A company that already uses an ERP system might choose chemical manufacturing software that integrates with the ERP to ensure seamless data flow between production, inventory, and sales departments.
- Cloud vs. On-Premise Solutions
- Decide between cloud-based or on-premise software. Cloud-based systems offer easier remote access and lower upfront costs, while on-premise solutions might provide greater control over security and customization.
- Example: A multinational chemical corporation may prefer an on-premise solution for higher data security, while a smaller company with fewer IT resources might opt for cloud-based software to reduce infrastructure costs.
- Data Interoperability
- Ensure the software allows for data interoperability across different departments, making it easier to share data between production, R&D, sales, and management. This promotes real-time decision-making and improves coordination.
- Example: A chemicals manufacturer uses the software’s ability to connect R&D and production data, ensuring that new formulations are accurately transferred to the production floor for pilot runs.
4. Ease of Use and User Interface
- Intuitive and User-Friendly Interface
- The software should have an intuitive interface, making it easy for your team to use without extensive training. Look for software with customizable dashboards and an easy-to-navigate layout.
- Example: A chemical plant operator prefers software with a simple dashboard that highlights production performance, inventory levels, and machine status, making it easier to make quick adjustments on the fly.
- User Support and Training
- Ensure that the software vendor provides comprehensive training materials, documentation, and a responsive customer support team. This will help your team adapt to the system faster and resolve any issues efficiently.
- Example: A new chemical manufacturer chooses software that provides on-site training and 24/7 customer support to ensure smooth implementation and troubleshooting during the initial setup phase.
5. Scalability and Future Growth
- Support for Business Expansion
- As your business grows, the software should be able to scale with it. Look for software that can handle increased production volumes, additional product lines, and expanded geographical reach.
- Example: A growing industrial chemical manufacturer opts for software with flexible configuration options and scalability, enabling them to add new production lines and locations without outgrowing the system.
- Upgrade and Customization Flexibility
- The software should allow for easy upgrades and customizations in response to evolving business needs or new regulations. This ensures that the solution remains valuable in the long term.
- Example: A chemical manufacturer that expands into new markets requires software that can be easily updated to comply with the new regulatory requirements of those regions.
6. Cost-Effectiveness
- Initial and Ongoing Costs
- Consider both the upfront cost and the ongoing expenses for the software, including licensing, maintenance, and training. Ensure the solution fits within your budget while still offering the necessary features and support.
- Example: A smaller chemical plant chooses a solution with lower upfront costs, but carefully reviews the subscription model to ensure that long-term expenses remain manageable as the company grows.
- Total Cost of Ownership (TCO)
- Look at the total cost of ownership, which includes not only the software purchase but also ongoing maintenance, IT support, updates, and integration with other systems.
- Example: A large-scale chemical manufacturer calculates the TCO to ensure that the investment in chemical manufacturing software will deliver value over time, factoring in future upgrades and potential operational savings.
7. Vendor Reputation and Customer Reviews
- Vendor Experience and Reputation
- Research the software vendor’s experience and track record in the chemical manufacturing industry. A vendor with a deep understanding of the sector will be more likely to provide solutions tailored to your needs.
- Example: A global chemical corporation selects a software provider with over 20 years of experience in the chemical sector, knowing that the vendor understands the nuances and regulatory challenges specific to the industry.
- Customer Testimonials and Case Studies
- Look for customer reviews, testimonials, and case studies to assess the software’s performance in real-world applications. Positive feedback and success stories can provide valuable insights into the software’s capabilities.
- Example: A specialty chemicals manufacturer reads customer reviews and case studies from similar businesses to validate the software’s ability to streamline production and improve regulatory compliance.
8. Security and Data Privacy
- Data Security Measures
- Ensure that the software vendor provides robust data security measures, including encryption, backup, and secure access protocols, especially if the software stores sensitive company or customer information.
- Example: A pharmaceutical manufacturer with sensitive data regarding active ingredients selects software with advanced security features, such as encrypted data storage and multi-factor authentication.
- Regulatory Data Privacy Compliance
- Choose software that adheres to relevant data privacy regulations, such as GDPR for businesses operating in Europe or CCPA for those in California. Compliance with these regulations ensures the software meets legal standards for handling customer and business data.
- Example: A chemical company expanding into the European market opts for software that complies with GDPR regulations to ensure the safe handling of personal data and avoid legal issues.
Conclusion
Choosing the right chemical manufacturing software is a complex process that requires thorough research and evaluation. By understanding your unique business needs, evaluating key features such as batch management, regulatory compliance, and scalability, and considering factors like integration capabilities and cost-effectiveness, you can make a well-informed decision. Remember to look for a solution that not only fits your current requirements but also supports future growth and ensures long-term operational efficiency. With the right software in place, your chemical manufacturing processes can become more streamlined, cost-effective, and compliant, driving business success in an increasingly competitive industry.
Conclusion
Chemical manufacturing software is a vital tool in the modern chemical industry, enabling businesses to streamline their operations, enhance productivity, ensure regulatory compliance, and optimize resources. As we’ve explored throughout this article, the growing complexity of chemical production, stringent regulatory requirements, and the need for operational efficiency make adopting specialized software solutions crucial for any chemical manufacturer aiming to remain competitive in today’s market.
By integrating advanced features such as batch management, formula optimization, inventory tracking, and quality control, chemical manufacturing software provides a comprehensive approach to managing the entire production lifecycle. Whether a small-scale producer or a global corporation, the right software can significantly improve production consistency, reduce operational risks, and ensure that your products meet the highest quality standards.
Key Benefits and Advantages
As highlighted earlier, the benefits of chemical manufacturing software are far-reaching. Companies can achieve tighter control over their production processes, mitigate human error, and maintain compliance with ever-evolving industry regulations. For instance, advanced data analytics and reporting features offer manufacturers the ability to make data-driven decisions, improving forecasting accuracy and enhancing supply chain visibility. These capabilities allow businesses to stay ahead of the competition by proactively addressing challenges and seizing new market opportunities.
Choosing the Right Solution
The process of choosing the right chemical manufacturing software requires careful analysis of your company’s specific needs. Factors such as production volume, customization needs, scalability, and integration with existing systems should guide your decision-making process. Moreover, understanding the vendor’s experience, reputation, and ability to offer ongoing support can significantly influence the success of your software implementation. A well-chosen software system will not only streamline current operations but will also scale with your business growth, adapting to new challenges and opportunities as they arise.
Implementation and Future Trends
While adopting chemical manufacturing software can be a transformative move, successful implementation is key to unlocking its full potential. Proper training, integration with existing workflows, and a clear roadmap for deployment are essential components of a successful adoption strategy. Furthermore, as the industry evolves, chemical manufacturing software will continue to advance with emerging technologies such as artificial intelligence (AI), machine learning, and IoT (Internet of Things), offering even more powerful capabilities to further enhance automation, process optimization, and predictive maintenance.
In Summary
In conclusion, chemical manufacturing software is more than just a technological tool; it is an integral asset that supports growth, efficiency, and compliance across every stage of production. By embracing this technology, chemical manufacturers can streamline complex operations, enhance product quality, and reduce costs. With the increasing demand for more sophisticated manufacturing processes and heightened regulations, the need for specialized software has never been greater.
Investing in chemical manufacturing software today can pave the way for a more efficient, cost-effective, and competitive future. As the industry continues to face new challenges, the ability to quickly adapt to new requirements and opportunities will depend on leveraging the right technology. By understanding the functionalities, benefits, and best practices for implementing chemical manufacturing software, businesses can ensure they remain at the forefront of the industry and meet the demands of an increasingly complex and competitive global market.
If you find this article useful, why not share it with your hiring manager and C-level suite friends and also leave a nice comment below?
We, at the 9cv9 Research Team, strive to bring the latest and most meaningful data, guides, and statistics to your doorstep.
To get access to top-quality guides, click over to 9cv9 Blog.
People Also Ask
What is Chemical Manufacturing Software?
Chemical manufacturing software is a digital solution designed to manage and optimize various processes in the chemical production industry, such as batch management, inventory control, and quality assurance.
How does Chemical Manufacturing Software work?
It integrates various production systems to track materials, manage formulations, monitor quality, and optimize manufacturing processes, often in real-time, to improve efficiency and compliance.
What are the key features of Chemical Manufacturing Software?
Key features include batch management, formula management, quality control, inventory tracking, compliance management, and real-time data analytics to support decision-making and optimize production.
Why is Chemical Manufacturing Software important?
It streamlines chemical production processes, enhances operational efficiency, ensures compliance with regulations, reduces errors, and improves product quality, ultimately saving time and costs.
What industries use Chemical Manufacturing Software?
Chemical manufacturing software is used in industries like pharmaceuticals, agrochemicals, petrochemicals, food processing, and specialty chemicals to manage production and ensure product consistency and safety.
How does Chemical Manufacturing Software improve compliance?
It helps companies comply with industry standards and regulations by providing real-time reporting, audit trails, and ensuring proper documentation of all production processes, making compliance easier.
What is batch management in Chemical Manufacturing Software?
Batch management involves tracking and managing the production of materials in batches, ensuring proper formulation, and monitoring each batch’s quality and traceability for consistency and safety.
Can Chemical Manufacturing Software integrate with other systems?
Yes, many chemical manufacturing software solutions are designed to integrate with ERP, CRM, and supply chain systems to enhance data sharing, streamline operations, and improve overall workflow.
What is the role of data analytics in Chemical Manufacturing Software?
Data analytics in chemical manufacturing software helps analyze production data, identify trends, predict outcomes, and optimize manufacturing processes for improved efficiency and decision-making.
What are the benefits of using Chemical Manufacturing Software?
Benefits include improved production efficiency, better quality control, enhanced compliance, reduced operational costs, and the ability to track and trace materials throughout the production process.
Can Chemical Manufacturing Software help with quality control?
Yes, it includes tools for monitoring production quality, identifying defects or inconsistencies, and ensuring that each batch meets the required specifications, improving product consistency.
How does Chemical Manufacturing Software optimize inventory management?
It tracks raw materials, work-in-progress, and finished goods in real-time, optimizing stock levels, reducing wastage, and ensuring timely availability of materials for uninterrupted production.
Is Chemical Manufacturing Software customizable?
Yes, many solutions offer customization options to adapt to specific manufacturing processes, industry needs, and company workflows, allowing businesses to tailor the software to their requirements.
How can Chemical Manufacturing Software help reduce production costs?
By optimizing resource use, reducing downtime, improving inventory management, and streamlining production processes, the software helps minimize waste, improve efficiency, and lower overall operational costs.
What is the cost of implementing Chemical Manufacturing Software?
The cost varies depending on the software’s features, scalability, and complexity. Factors such as company size, customization needs, and deployment type (cloud or on-premise) also influence the price.
Can Chemical Manufacturing Software help with supply chain management?
Yes, it supports supply chain management by offering real-time tracking of materials, monitoring suppliers, and optimizing delivery schedules, ensuring seamless production flow and reducing supply chain disruptions.
What types of reports can Chemical Manufacturing Software generate?
It can generate reports on production performance, inventory levels, quality control, compliance status, batch traceability, and more, providing insights to support informed decision-making and management.
How can Chemical Manufacturing Software help with regulatory compliance?
It automates the documentation and reporting required by regulatory authorities, providing audit trails, real-time data, and process tracking to ensure compliance with industry regulations like GMP, FDA, or ISO standards.
Is Chemical Manufacturing Software suitable for small businesses?
Yes, chemical manufacturing software can be tailored to suit small businesses, offering scalability and affordable options to streamline operations, manage quality, and ensure regulatory compliance even with limited resources.
How does Chemical Manufacturing Software improve traceability?
It tracks the flow of materials and finished products through every stage of production, providing complete visibility and documentation for traceability, which is crucial for quality control and compliance.
What is the difference between Chemical Manufacturing Software and ERP?
Chemical manufacturing software focuses on specific needs like batch production, formula management, and quality control, while ERP (Enterprise Resource Planning) is broader and manages overall business functions such as finance, HR, and supply chain.
Can Chemical Manufacturing Software improve production efficiency?
Yes, by automating workflows, optimizing production schedules, and reducing errors, it enhances the speed, accuracy, and consistency of manufacturing processes, ultimately improving overall efficiency.
What is formula management in Chemical Manufacturing Software?
Formula management allows manufacturers to track and manage the precise ratios of raw materials needed for different chemical products, ensuring consistency and quality in every batch produced.
Does Chemical Manufacturing Software support real-time monitoring?
Yes, it supports real-time monitoring of production metrics, inventory levels, and equipment performance, allowing for quick adjustments and ensuring smooth production operations.
Can Chemical Manufacturing Software handle multiple production facilities?
Yes, many systems offer multi-site support, enabling companies with multiple production facilities to monitor and manage operations, inventory, and quality across various locations from a central platform.
How secure is Chemical Manufacturing Software?
Most software solutions incorporate robust security features, such as data encryption, access control, and regular updates, to ensure the protection of sensitive production data and compliance with privacy regulations.
What types of businesses benefit from Chemical Manufacturing Software?
Businesses involved in chemical production, including those in pharmaceuticals, petrochemicals, agrochemicals, and specialty chemicals, benefit from enhanced process control, inventory management, and regulatory compliance.
Can Chemical Manufacturing Software help with forecasting?
Yes, by analyzing historical production data and market trends, it enables businesses to forecast demand, adjust production schedules, and optimize resources for better financial planning and decision-making.
How do I choose the right Chemical Manufacturing Software?
Choose based on your business’s specific needs, such as production volume, customization options, integration capabilities, and scalability, ensuring the software aligns with your production goals and regulatory requirements.
Is training required to use Chemical Manufacturing Software?
Yes, training is typically required to ensure employees can fully leverage the software’s features, understand workflows, and use it effectively for managing production and compliance.
How does Chemical Manufacturing Software improve decision-making?
By providing real-time data, performance analytics, and comprehensive reports, it helps managers make data-driven decisions regarding inventory, quality control, production scheduling, and more.
Can Chemical Manufacturing Software help with environmental compliance?
Yes, it helps ensure that manufacturing processes adhere to environmental regulations by tracking emissions, waste management, and ensuring compliance with sustainability standards.
What are the advantages of cloud-based Chemical Manufacturing Software?
Cloud-based software offers easier scalability, remote access, lower upfront costs, and automatic updates, providing manufacturers with a flexible and cost-effective solution for their production management needs.
How often do updates occur in Chemical Manufacturing Software?
Updates vary by vendor but typically occur regularly to add new features, enhance security, improve functionality, and ensure compliance with changing regulations in the chemical industry.
What kind of support do Chemical Manufacturing Software vendors provide?
Most vendors offer technical support, training, troubleshooting, and system maintenance to ensure smooth operation, address issues promptly, and help businesses get the most from the software.
Can Chemical Manufacturing Software be used for global production operations?
Yes, it can be used for global operations, with features that allow for multi-language support, multiple currencies, and the management of international regulatory standards across different regions.