Key Takeaways
- CMMS automates maintenance processes, improving asset management, reducing downtime, and optimizing resource allocation.
- It enables preventive and predictive maintenance, ensuring equipment longevity, regulatory compliance, and cost savings.
- Future CMMS trends include AI, IoT, and cloud-based solutions, enhancing real-time monitoring and data-driven decision-making.
In today’s fast-paced industrial landscape, businesses across various sectors rely heavily on well-maintained equipment and assets to ensure smooth operations, minimize downtime, and optimize productivity. However, managing maintenance tasks manually can be a complex and inefficient process, often leading to unexpected breakdowns, costly repairs, and disruptions in workflow. This is where a Computerized Maintenance Management System (CMMS) comes into play as a transformative solution for modern businesses looking to streamline their maintenance operations.
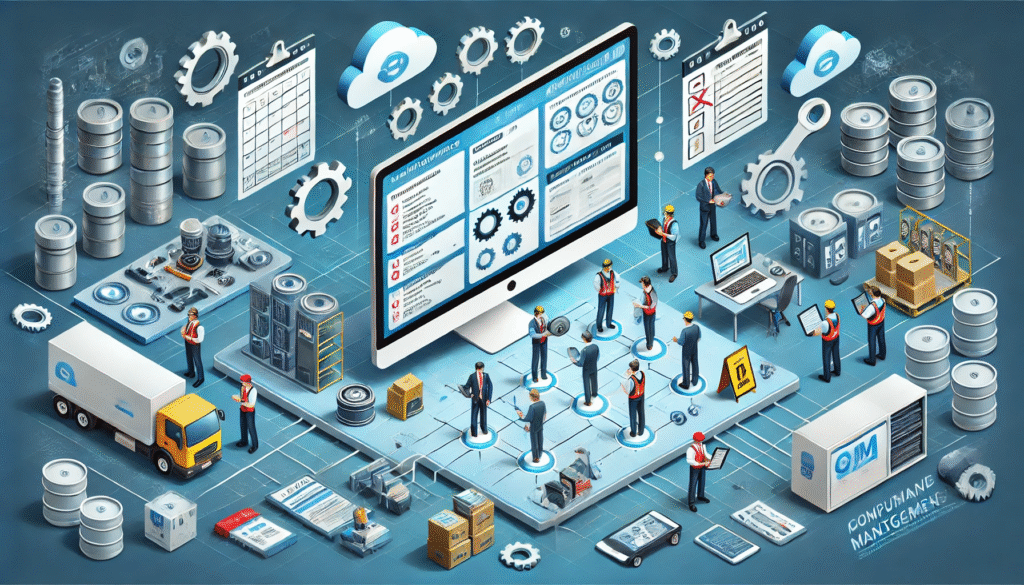
A CMMS is a software-based solution designed to centralize, automate, and optimize maintenance management activities, enabling organizations to efficiently track assets, schedule preventive maintenance, and manage work orders with real-time data insights. Whether in manufacturing, healthcare, facility management, or transportation, CMMS software provides a systematic approach to asset maintenance, helping businesses extend equipment lifespan, improve operational efficiency, and reduce overall maintenance costs.
The evolution of maintenance management from traditional manual methods to digital solutions has revolutionized the way organizations approach equipment upkeep. In the past, maintenance teams relied on spreadsheets, paperwork, and reactive maintenance strategies, which often resulted in costly inefficiencies. However, with the advent of CMMS software, businesses can now shift towards a proactive and data-driven maintenance approach, leveraging advanced features such as predictive analytics, automated scheduling, and IoT (Internet of Things) integration to enhance overall asset performance.
One of the core functions of a CMMS is its ability to track the entire lifecycle of assets, allowing organizations to monitor equipment usage, identify potential failures, and schedule maintenance tasks before problems arise. This proactive strategy helps reduce unplanned downtime, increase asset reliability, and ensure compliance with industry regulations and safety standards. Additionally, CMMS solutions provide maintenance teams with real-time visibility into inventory levels, ensuring that spare parts and essential resources are always available when needed, thus preventing delays in repairs.
Another crucial aspect of CMMS software is its capability to generate comprehensive reports and analytics, offering valuable insights into maintenance trends, cost analysis, and performance metrics. By utilizing these data-driven insights, businesses can make informed decisions to optimize maintenance budgets, allocate resources effectively, and improve overall asset management strategies. Moreover, the integration of CMMS with emerging technologies such as Artificial Intelligence (AI), Machine Learning (ML), and IoT further enhances predictive maintenance capabilities, allowing organizations to detect potential failures before they occur and optimize maintenance schedules accordingly.
As organizations strive to achieve higher operational efficiency, cost savings, and regulatory compliance, implementing a robust CMMS has become a necessity rather than a luxury. Whether managing a large fleet of vehicles, maintaining critical medical equipment, or overseeing industrial machinery, businesses can significantly benefit from a well-implemented CMMS solution. By automating and simplifying maintenance processes, CMMS not only enhances asset reliability but also empowers maintenance teams with the tools and insights needed to make proactive, data-driven decisions.
In the following sections, we will delve deeper into the core functionalities of CMMS, its working mechanisms, the benefits it offers, and how different industries leverage this powerful software to enhance their maintenance strategies. Understanding how CMMS works and why it is essential for businesses will provide valuable insights into how organizations can optimize maintenance operations and improve long-term asset performance.
Before we venture further into this article, we would like to share who we are and what we do.
About 9cv9
9cv9 is a business tech startup based in Singapore and Asia, with a strong presence all over the world.
With over nine years of startup and business experience, and being highly involved in connecting with thousands of companies and startups, the 9cv9 team has listed some important learning points in this overview of What is Computerized Maintenance Management System (CMMS) and How It Works.
If your company needs recruitment and headhunting services to hire top-quality employees, you can use 9cv9 headhunting and recruitment services to hire top talents and candidates. Find out more here, or send over an email to hello@9cv9.com.
Or just post 1 free job posting here at 9cv9 Hiring Portal in under 10 minutes.
What is Computerized Maintenance Management System (CMMS) and How It Works
- Understanding Computerized Maintenance Management System (CMMS)
- How CMMS Works: A Step-by-Step Breakdown
- Benefits of Using a CMMS
- Industries That Benefit from CMMS
- Key Features to Look for in a CMMS Software
- Challenges and Considerations in Implementing CMMS
- Future Trends in CMMS
1. Understanding Computerized Maintenance Management System (CMMS)
A Computerized Maintenance Management System (CMMS) is a powerful software solution designed to streamline and automate maintenance operations across various industries. It serves as a centralized platform for managing assets, scheduling maintenance, tracking work orders, and maintaining historical records of equipment performance. By replacing traditional paper-based methods and spreadsheets, CMMS helps businesses improve efficiency, reduce operational costs, and extend asset lifespans.
To gain a deeper understanding of CMMS, it is essential to explore its definition, key components, functionalities, and how it differs from other maintenance management systems.
What is a CMMS?
- A CMMS is a digital tool that helps organizations plan, track, and optimize maintenance activities to ensure equipment reliability and efficiency.
- It provides a structured approach to maintenance management by offering real-time visibility into asset conditions, work orders, and spare parts inventory.
- CMMS is widely used across various industries, including manufacturing, healthcare, facility management, transportation, energy, and logistics, where asset uptime is crucial.
- By leveraging automation and data-driven insights, organizations can transition from reactive maintenance (fixing equipment after failure) to proactive and predictive maintenance strategies.
Key Components of a CMMS
A well-structured CMMS consists of several core components that work together to enhance maintenance management. These include:
1. Asset and Equipment Management
- Stores detailed records of all assets, including serial numbers, model details, maintenance history, and expected lifespan.
- Helps organizations track the condition, location, and usage of equipment in real time.
- Example: A manufacturing plant can use CMMS to monitor production machinery, ensuring that each machine receives timely maintenance to prevent unplanned downtime.
2. Work Order Management
- Automates the creation, assignment, and tracking of work orders for corrective, preventive, and predictive maintenance tasks.
- Provides real-time updates on maintenance tasks, helping teams prioritize urgent repairs.
- Example: In a hospital, CMMS helps facility managers schedule maintenance for critical medical devices, such as MRI scanners and ventilators, ensuring patient safety.
3. Preventive Maintenance Scheduling
- Allows maintenance teams to set up recurring maintenance schedules based on time intervals, usage metrics, or condition-based triggers.
- Reduces the risk of unexpected equipment failures by ensuring that maintenance tasks are performed before issues arise.
- Example: An airline can use CMMS to schedule routine aircraft inspections, ensuring compliance with aviation regulations and passenger safety.
4. Spare Parts and Inventory Management
- Tracks spare parts usage, stock levels, and reordering requirements to prevent shortages or excess inventory.
- Sends automated alerts when stock levels fall below predefined thresholds.
- Example: A power plant using CMMS can ensure that essential components like turbines and circuit breakers are always available for emergency repairs.
5. Reporting and Analytics
- Generates detailed reports on maintenance performance, costs, equipment downtime, and resource allocation.
- Uses historical data and predictive analytics to optimize maintenance strategies.
- Example: A logistics company can analyze fleet maintenance reports in CMMS to identify patterns in vehicle breakdowns and implement proactive solutions.
6. Integration with IoT and Other Enterprise Systems
- Modern CMMS solutions integrate with Internet of Things (IoT) sensors, Enterprise Resource Planning (ERP) systems, and other business applications to enhance functionality.
- IoT-powered CMMS can detect anomalies in equipment performance and automatically trigger maintenance actions.
- Example: In a smart factory, IoT sensors detect abnormal vibrations in a conveyor belt and send an alert to the CMMS, which schedules an inspection before the issue escalates.
How CMMS Differs from Other Maintenance Management Systems
Organizations often compare CMMS with other maintenance management tools, such as Enterprise Asset Management (EAM) and Facility Management Software (FMS). Here’s how they differ:
1. CMMS vs. Enterprise Asset Management (EAM)
- CMMS focuses on maintenance-specific tasks, such as work orders, preventive maintenance, and asset tracking.
- EAM covers a broader scope, including asset lifecycle management, procurement, financial tracking, and compliance monitoring.
- Example: A manufacturing company may use CMMS for daily maintenance tasks, while EAM is used for long-term asset planning and capital investment decisions.
2. CMMS vs. Facility Management Software (FMS)
- CMMS is designed for managing equipment maintenance and repairs, focusing on asset reliability.
- FMS includes additional features for space planning, energy management, and facility security.
- Example: A hotel chain may use CMMS to manage HVAC system maintenance, while FMS is used for room booking and energy optimization.
Types of CMMS Deployments
Organizations can choose from different types of CMMS deployments based on their business needs and IT infrastructure.
1. Cloud-Based CMMS
- Hosted on remote servers and accessed via web browsers or mobile apps.
- Offers scalability, remote access, and automatic software updates.
- Ideal for businesses with multiple locations or remote maintenance teams.
- Example: A global construction company can use a cloud-based CMMS to manage heavy equipment maintenance across different project sites.
2. On-Premises CMMS
- Installed and maintained on the company’s internal servers.
- Provides greater control over data security and customization options.
- Requires IT expertise for software maintenance and updates.
- Example: A government agency with strict data security policies may prefer an on-premises CMMS to maintain compliance.
3. Mobile CMMS
- Accessible via smartphones and tablets, enabling maintenance teams to update work orders, check inventory, and access asset details on the go.
- Enhances real-time communication and field maintenance efficiency.
- Example: A transportation company can equip fleet maintenance crews with mobile CMMS to log vehicle inspections in real-time.
Why Businesses Need a CMMS
Investing in a CMMS offers several advantages that contribute to operational efficiency, cost savings, and improved asset management.
- Reduces equipment downtime by enabling preventive and predictive maintenance.
- Enhances workforce productivity by automating routine maintenance tasks.
- Improves compliance with safety regulations by maintaining detailed maintenance records.
- Optimizes maintenance budgets by tracking costs and reducing unnecessary repairs.
- Provides real-time visibility into asset performance for data-driven decision-making.
Conclusion
A Computerized Maintenance Management System (CMMS) is an essential tool for businesses looking to modernize their maintenance operations and improve asset reliability. By leveraging automation, real-time data, and integration with emerging technologies, CMMS helps organizations shift from reactive maintenance to a proactive and strategic approach. Whether managing factory equipment, medical devices, or transportation fleets, CMMS plays a critical role in ensuring efficiency, safety, and cost-effectiveness in maintenance management.
2. How CMMS Works: A Step-by-Step Breakdown
A Computerized Maintenance Management System (CMMS) is designed to streamline, automate, and enhance maintenance operations by centralizing all maintenance-related data in a digital system. It follows a structured process that enables organizations to plan, track, and execute maintenance activities efficiently.
This section provides a step-by-step breakdown of how CMMS works, covering key processes such as asset registration, work order management, preventive maintenance scheduling, inventory control, data analytics, and integration with other business systems.
1. Asset Registration and Data Entry
Before CMMS can be fully operational, organizations must register and catalog all assets into the system. This foundational step ensures that every piece of equipment, machine, or infrastructure component is properly recorded and tracked.
- Asset Identification:
- Each asset is assigned a unique identification number for easy tracking.
- Includes serial numbers, model information, manufacturer details, and purchase dates.
- Example: A manufacturing company registers all production machinery, such as CNC machines, conveyor belts, and robotic arms, in CMMS.
- Asset Classification and Grouping:
- Assets are categorized based on function, department, or location.
- Helps in assigning maintenance responsibilities efficiently.
- Example: In a hospital, medical devices like ventilators and MRI machines are grouped under “Medical Equipment,” while HVAC systems are categorized under “Facility Maintenance.”
- Maintenance History and Documentation:
- Previous maintenance records, warranty details, and service agreements are uploaded to the CMMS.
- Ensures compliance with safety regulations and industry standards.
- Example: An airline records the complete maintenance history of aircraft engines to ensure compliance with aviation safety laws.
2. Work Order Creation and Management
Work orders are central to CMMS functionality, as they organize, schedule, and track maintenance tasks in real time.
- Creating a Work Order:
- Maintenance requests can be automatically generated based on system alerts or manually entered by staff.
- Includes task descriptions, priority levels, assigned technicians, and estimated completion times.
- Example: A logistics company generates a work order for routine vehicle inspections every 10,000 miles.
- Assigning and Scheduling Work Orders:
- Work orders are assigned based on technician availability, skill set, and urgency.
- CMMS provides a calendar view for scheduling maintenance tasks efficiently.
- Example: In a hotel, maintenance staff receive digital work orders on their mobile devices for plumbing or electrical repairs in guest rooms.
- Tracking and Completion:
- Technicians update work orders in real-time, including task completion status, parts used, and labor hours.
- CMMS logs the completion time and updates the asset’s maintenance history.
- Example: A factory technician logs repairs on a malfunctioning robotic arm, noting that a motor replacement was required.
3. Preventive Maintenance Scheduling
Preventive maintenance (PM) is a proactive approach to avoid unexpected breakdowns and extend equipment life. CMMS automates PM scheduling based on time, usage, or condition-based triggers.
- Setting Up Maintenance Triggers:
- CMMS allows maintenance managers to schedule PM tasks based on:
- Time-based intervals (e.g., every 3 months).
- Usage-based triggers (e.g., after 500 operating hours).
- Condition-based alerts from IoT sensors.
- Example: A power plant schedules boiler inspections every six months to comply with safety regulations.
- CMMS allows maintenance managers to schedule PM tasks based on:
- Automating Preventive Maintenance Tasks:
- CMMS generates automatic reminders and work orders when a PM task is due.
- Ensures equipment is serviced before failures occur.
- Example: An oil refinery uses CMMS to schedule lubrication of pumps and valves to prevent wear and tear.
- Tracking Compliance and Completion:
- CMMS logs completed PM tasks and alerts management to missed or overdue maintenance.
- Helps meet compliance standards like OSHA (Occupational Safety and Health Administration).
- Example: A food processing plant uses CMMS to track sanitization of production equipment to meet FDA standards.
4. Inventory and Spare Parts Management
CMMS helps organizations maintain optimal stock levels of spare parts to prevent maintenance delays.
- Tracking Spare Parts Usage:
- CMMS records real-time inventory levels and logs every part used in maintenance tasks.
- Avoids unnecessary stockpiling or shortages.
- Example: A railway company tracks the availability of train brake components to ensure replacements are available.
- Automated Reordering and Supplier Management:
- CMMS sends alerts when inventory levels drop below predefined thresholds.
- Integrates with supplier databases for automated purchasing.
- Example: A hospital CMMS triggers an order for replacement oxygen sensors when stock falls below five units.
5. Real-Time Data Analytics and Reporting
CMMS provides valuable insights through data analysis, enabling better decision-making and cost reduction.
- Generating Maintenance Performance Reports:
- CMMS analyzes data to generate reports on:
- Equipment downtime and uptime.
- Maintenance costs and labor efficiency.
- Mean Time Between Failures (MTBF) and Mean Time to Repair (MTTR).
- Example: A manufacturing company uses CMMS reports to identify machinery with frequent failures, planning replacement or upgrades accordingly.
- CMMS analyzes data to generate reports on:
- Predictive Maintenance with IoT Integration:
- Advanced CMMS platforms integrate with IoT sensors and AI-driven predictive analytics.
- Detects anomalies in equipment performance and schedules maintenance before failures occur.
- Example: A smart factory’s IoT sensors detect abnormal vibrations in conveyor belts and trigger a CMMS work order.
6. Integration with Other Business Systems
CMMS often integrates with Enterprise Resource Planning (ERP), Internet of Things (IoT), and Facility Management Software (FMS) to improve overall operational efficiency.
- ERP Integration:
- Links maintenance data with financial and procurement systems for better budgeting and cost tracking.
- Example: A logistics company integrates CMMS with ERP to track maintenance expenses for fleet vehicles.
- IoT and AI Integration:
- IoT sensors feed real-time data into CMMS, enabling automated work order generation.
- AI algorithms analyze equipment performance trends for predictive insights.
- Example: A wind farm uses AI-driven CMMS to schedule turbine maintenance based on wind speed and vibration data.
- Mobile CMMS for Remote Accessibility:
- Field technicians use mobile CMMS apps to receive, update, and close work orders in real-time.
- Enhances communication between teams, reducing response time.
- Example: A utility company’s field engineers use mobile CMMS to access power grid maintenance logsfrom remote locations.
Conclusion
A Computerized Maintenance Management System (CMMS) works through a structured and automated process that enhances asset reliability, reduces downtime, and optimizes maintenance workflows. By digitizing asset management, automating work orders, enabling preventive maintenance, and leveraging data analytics, CMMS transforms maintenance operations into a strategic advantage.
Businesses across various industries, from manufacturing to healthcare, transportation, and facility management, rely on CMMS to streamline maintenance processes, improve regulatory compliance, and reduce costs. As technology advances, integrations with AI, IoT, and mobile platforms will further enhance the capabilities of CMMS, making maintenance smarter, more predictive, and highly efficient.
3. Benefits of Using a CMMS
A Computerized Maintenance Management System (CMMS) offers organizations a powerful tool to streamline maintenance operations, enhance equipment reliability, and improve cost efficiency. By automating work orders, tracking asset performance, and providing data-driven insights, CMMS helps businesses across industries optimize maintenance management.
This section explores the key benefits of using CMMS, including improved asset longevity, reduced downtime, cost savings, regulatory compliance, data-driven decision-making, and enhanced workforce efficiency.
1. Improved Equipment Reliability and Longevity
CMMS helps businesses proactively maintain equipment, extending asset life and reducing the frequency of breakdowns.
- Prevents Unplanned Equipment Failures:
- Automated preventive maintenance scheduling ensures equipment is serviced before major issues arise.
- CMMS sends alerts for routine inspections, lubrication, and part replacements.
- Example: A manufacturing plant using CMMS for regular machine servicing experiences fewer unexpected failures, keeping production on schedule.
- Enhances Predictive Maintenance with IoT Integration:
- IoT-connected CMMS detects performance anomalies in real-time.
- AI-powered predictive analytics trigger maintenance work orders before equipment malfunctions.
- Example: A power plant integrates CMMS with IoT sensors to monitor turbine vibration levels, reducing unplanned outages.
- Increases Equipment Lifespan:
- Regular maintenance reduces wear and tear, prolonging asset longevity.
- Ensures machines operate at optimal efficiency for longer periods.
- Example: A hospital using CMMS to track MRI machine maintenance extends the machine’s lifespan by several years, reducing capital expenditures.
2. Reduced Downtime and Increased Productivity
CMMS minimizes equipment downtime by automating maintenance workflows and optimizing technician scheduling.
- Faster Issue Resolution:
- Digital work order tracking ensures quick response to maintenance requests.
- CMMS allows managers to prioritize urgent repairs and allocate resources efficiently.
- Example: A logistics company reduces fleet downtime by using CMMS to automatically assign vehicle repairs to available mechanics.
- Optimized Work Scheduling:
- CMMS eliminates scheduling conflicts by organizing maintenance tasks in a centralized system.
- Assigns jobs based on technician availability, skill level, and location.
- Example: A hotel maintenance team receives automated CMMS notifications for plumbing, HVAC, and electrical repairs, ensuring minimal guest disruptions.
- Reduces Equipment Idle Time:
- Maintenance is scheduled during non-peak hours to prevent production slowdowns.
- CMMS ensures backup equipment is available when primary assets require servicing.
- Example: A food processing plant schedules machine cleaning cycles at night to keep production running smoothly during the day.
3. Significant Cost Savings on Maintenance Operations
By optimizing maintenance processes, CMMS helps businesses cut down on repair costs, labor expenses, and inventory waste.
- Lowers Emergency Repair Costs:
- Preventive and predictive maintenance reduces expensive emergency repairs.
- Avoids last-minute procurement of spare parts at higher costs.
- Example: A railway company saves thousands annually by using CMMS to track train brake component wear and replace parts proactively.
- Reduces Overtime and Labor Costs:
- CMMS distributes workload efficiently, preventing unnecessary overtime.
- Ensures technicians focus on high-priority tasks, improving labor productivity.
- Example: A university reduces HVAC system maintenance costs by using CMMS to schedule repairs when technicians are on regular shifts instead of overtime hours.
- Optimized Spare Parts Inventory Management:
- CMMS prevents overstocking and understocking of spare parts.
- Automated reordering ensures essential components are available without excessive stockpiling.
- Example: A manufacturing company uses CMMS to track bearing replacements, reducing excess inventory costs.
4. Regulatory Compliance and Safety Improvements
CMMS helps organizations comply with industry regulations and maintain safe working environments.
- Automated Compliance Tracking:
- CMMS stores inspection reports, safety logs, and regulatory documentation in a centralized system.
- Sends alerts for upcoming audits and compliance deadlines.
- Example: A pharmaceutical company uses CMMS to track compliance with FDA regulations, ensuring production facility inspections are always up to date.
- Ensures Workplace Safety:
- Regular maintenance reduces workplace hazards such as equipment malfunctions and electrical failures.
- Safety checklists and procedures are integrated into CMMS to prevent accidents and injuries.
- Example: A construction company uses CMMS to enforce crane and heavy equipment safety inspections, minimizing the risk of mechanical failures.
- Tracks Certification and Training Compliance:
- CMMS ensures maintenance staff have updated certifications and training records.
- Prevents unauthorized personnel from operating or repairing specialized equipment.
- Example: A chemical plant uses CMMS to track operator licenses for hazardous equipment to meet OSHA requirements.
5. Data-Driven Decision Making and Performance Insights
CMMS provides real-time analytics and historical data, allowing businesses to make informed maintenance decisions.
- Generates Detailed Maintenance Reports:
- Tracks metrics such as Mean Time Between Failures (MTBF) and Mean Time to Repair (MTTR).
- Provides insights into asset performance, labor efficiency, and maintenance costs.
- Example: A transportation company analyzes CMMS data to identify high-maintenance vehicles and replace them with more reliable alternatives.
- Predicts Future Maintenance Needs:
- AI-powered CMMS predicts which assets are likely to fail next, allowing proactive servicing.
- Reduces the need for unexpected capital expenditures.
- Example: An airline company uses CMMS to analyze engine performance trends, scheduling maintenance before performance drops.
- Improves Budget Planning and Cost Forecasting:
- Historical data helps organizations allocate maintenance budgets more accurately.
- Identifies areas where costs can be reduced without compromising asset performance.
- Example: A municipal water treatment plant uses CMMS to track pump replacement costs, optimizing future budget planning.
6. Remote and Mobile Accessibility for Technicians
Modern CMMS platforms support mobile access, allowing technicians to update work orders, check inventory, and submit reports from the field.
- Enhances Technician Efficiency:
- Mobile CMMS reduces paperwork and manual data entry.
- Field workers receive real-time updates, reducing miscommunication.
- Example: A utility company enables remote technicians to access asset maintenance logs from their mobile devices, eliminating unnecessary trips to the office.
- Faster Response to Equipment Issues:
- Mobile alerts notify technicians of urgent work orders instantly.
- Reduces downtime by eliminating delays in issue reporting and resolution.
- Example: A hotel maintenance team receives real-time CMMS alerts for plumbing and electrical malfunctions, ensuring quick repairs before guest complaints arise.
Conclusion
A CMMS is a critical tool for organizations looking to improve maintenance efficiency, reduce costs, and extend asset lifespan. From enhancing preventive maintenance and minimizing downtime to ensuring regulatory compliance and data-driven decision-making, CMMS transforms maintenance management into a strategic advantage.
Industries such as manufacturing, healthcare, transportation, and facility management increasingly rely on CMMS to automate workflows, increase productivity, and optimize asset performance. As CMMS technology continues to evolve with AI, IoT, and mobile accessibility, organizations that implement it effectively will gain a competitive edge in operational efficiency and cost savings.
4. Industries That Benefit from CMMS
A Computerized Maintenance Management System (CMMS) is a valuable tool across multiple industries that require efficient maintenance operations, asset tracking, and regulatory compliance. Organizations that manage equipment, facilities, vehicle fleets, or infrastructure can leverage CMMS to reduce downtime, optimize maintenance costs, and improve operational efficiency.
This section explores the industries that benefit most from CMMS, including manufacturing, healthcare, facility management, transportation, energy, hospitality, and education.
1. Manufacturing Industry
The manufacturing sector relies on highly complex machinery and production lines, making maintenance optimization crucial to prevent downtime and maximize productivity.
- Preventive Maintenance for Machinery:
- CMMS automatically schedules routine maintenance, preventing equipment failures.
- Tracks performance data to detect early signs of wear and tear.
- Example: A car manufacturer uses CMMS to ensure robotic assembly arms are serviced regularly, reducing production delays.
- Minimized Downtime and Production Losses:
- CMMS helps schedule maintenance during non-peak hours, preventing production stoppages.
- Provides real-time alerts for urgent repairs before breakdowns occur.
- Example: A food processing plant reduces equipment failures by implementing automated CMMS alertsfor conveyor belt inspections.
- Optimized Spare Parts Inventory Management:
- Tracks spare parts usage to prevent overstocking and reduce storage costs.
- Ensures parts are available before equipment failures occur.
- Example: A textile manufacturer uses CMMS to manage spare motors and gearboxes, preventing production delays due to missing parts.
2. Healthcare and Hospital Management
Hospitals and healthcare facilities operate 24/7, making equipment maintenance essential for patient safety and compliance with health regulations.
- Ensuring Medical Equipment Reliability:
- CMMS schedules regular maintenance for MRI machines, ventilators, and surgical equipment.
- Tracks performance data to detect malfunction risks before failure.
- Example: A large hospital uses CMMS to monitor dialysis machines, preventing unexpected failures that could impact patient care.
- Regulatory Compliance and Safety Standards:
- CMMS stores maintenance logs and inspection reports, ensuring compliance with FDA, HIPAA, and other health regulations.
- Notifies staff of upcoming audits or required servicing.
- Example: A biotechnology lab uses CMMS to track sterilization equipment maintenance, ensuring regulatory adherence.
- Facility Management for Hospitals:
- Schedules HVAC system maintenance for proper air circulation.
- Manages sanitation, emergency power systems, and water filtration maintenance.
- Example: A nursing home reduces airborne infection risks by ensuring HVAC filters are changed regularly through CMMS reminders.
3. Facility and Property Management
Facility managers oversee large buildings, offices, and commercial spaces, requiring an organized system for maintenance tracking and work order management.
- Automated Work Order Management:
- CMMS enables property managers to schedule repairs, track technician performance, and monitor building maintenance requests.
- Reduces delays in addressing tenant complaints.
- Example: A corporate office complex uses CMMS to schedule elevator maintenance and lighting repairs, improving workplace safety.
- Energy Efficiency and Cost Reduction:
- CMMS tracks HVAC, plumbing, and electrical system performance, optimizing energy consumption.
- Detects inefficiencies in water usage, heating, and cooling systems.
- Example: A shopping mall reduces energy costs by using CMMS to schedule HVAC system servicing, preventing energy wastage.
- Safety and Compliance in Public Spaces:
- Ensures compliance with fire safety regulations, building codes, and security system maintenance.
- Reduces risks of liabilities due to unmaintained structures.
- Example: A stadium uses CMMS to track fire extinguisher inspections and emergency exit maintenance before major events.
4. Transportation and Fleet Management
Logistics and transportation industries depend on vehicle uptime and efficiency, making CMMS essential for fleet maintenance and regulatory compliance.
- Scheduled Vehicle Maintenance for Fleets:
- CMMS automates oil changes, tire rotations, brake inspections, and engine servicing.
- Reduces unexpected breakdowns and increases fuel efficiency.
- Example: A trucking company minimizes downtime costs by using CMMS for real-time fleet health monitoring.
- Regulatory Compliance for Transport Safety:
- Ensures vehicles meet DOT, FAA, or railway safety regulations.
- Stores maintenance records for audit readiness.
- Example: A bus company uses CMMS to track wheel alignment inspections, preventing safety hazards.
- Optimized Fuel and Parts Inventory Management:
- Tracks fuel efficiency and spare parts usage trends, reducing waste.
- Prevents unnecessary expenditures on excess parts stockpiling.
- Example: A rental car company uses CMMS to monitor battery replacements, preventing unexpected vehicle failures.
5. Energy and Utilities Industry
Energy companies manage complex infrastructure, including power plants, wind farms, and water treatment facilities, requiring strict maintenance schedules.
- Preventive Maintenance for Critical Infrastructure:
- CMMS ensures power grids, turbines, and substations are serviced on time.
- Reduces risks of power outages and equipment failures.
- Example: A hydroelectric plant tracks turbine inspections using CMMS to prevent system failures.
- Compliance with Environmental Regulations:
- Ensures compliance with EPA, OSHA, and energy safety standards.
- Tracks emissions, leak detection, and hazardous material disposal.
- Example: A solar power plant uses CMMS to track panel maintenance and inverter efficiency, ensuring sustainable energy production.
- Remote Monitoring and IoT Integration:
- CMMS integrates with IoT sensors to track temperature, pressure, and vibration levels in real-time.
- Reduces the need for manual inspections in hazardous environments.
- Example: A natural gas pipeline company detects pressure leaks using CMMS alerts, preventing accidents.
6. Hospitality Industry
Hotels, resorts, and entertainment facilities require constant maintenance to ensure guest satisfaction and operational efficiency.
- Preventive Maintenance for Guest Comfort:
- CMMS schedules HVAC, plumbing, and electrical inspections, ensuring seamless hotel operations.
- Tracks maintenance requests from guests and staff.
- Example: A five-star hotel uses CMMS to ensure room air conditioning units are serviced before peak tourist seasons.
- Kitchen and Laundry Equipment Management:
- CMMS tracks the maintenance of industrial dishwashers, refrigerators, and laundry machines.
- Prevents service disruptions in restaurants and housekeeping.
- Example: A casino resort reduces kitchen equipment failures by using CMMS to schedule regular servicing.
7. Educational Institutions
Schools and universities require efficient facility maintenance to support student and staff needs.
- Campus Facility Maintenance:
- CMMS tracks classroom HVAC, lighting, and restroom maintenance.
- Ensures playgrounds, gyms, and sports fields are safe.
- Example: A university uses CMMS to schedule dormitory repairs, improving student satisfaction.
- Laboratory and IT Equipment Management:
- CMMS schedules servicing for computers, projectors, lab equipment, and electrical systems.
- Reduces unexpected failures affecting education.
- Example: A STEM research center uses CMMS to track microscope calibration schedules.
Conclusion
A CMMS provides immense value across multiple industries, ensuring optimized asset performance, compliance with regulations, and cost savings. Organizations in manufacturing, healthcare, transportation, energy, hospitality, and education benefit from CMMS to streamline maintenance processes, reduce downtime, and enhance operational efficiency. As industries continue to adopt digital transformation, CMMS will become an essential tool for ensuring long-term sustainability and productivity.
5. Key Features to Look for in a CMMS Software
A Computerized Maintenance Management System (CMMS) is a vital tool for businesses seeking to optimize maintenance operations, asset management, and facility upkeep. The effectiveness of a CMMS depends on its features, which should align with an organization’s maintenance needs, industry requirements, and operational goals.
Below are the key features to look for in a CMMS software, ensuring maximum efficiency, cost savings, and compliance.
1. Asset Management and Tracking
A robust asset management feature is essential for tracking and maintaining equipment, machinery, and infrastructure efficiently.
- Real-Time Asset Monitoring:
- Provides a centralized database for storing asset details, including location, condition, warranty, and maintenance history.
- Helps businesses track equipment depreciation for financial planning.
- Example: A manufacturing plant uses CMMS to monitor production line machinery, ensuring timely maintenance to prevent breakdowns.
- Barcode and RFID Integration:
- Allows asset identification through QR codes, barcodes, or RFID tags.
- Reduces errors in manual data entry and streamlines inventory audits.
- Example: A hospital tags MRI machines and ventilators with RFID chips for real-time tracking and preventive maintenance scheduling.
- Lifecycle Management:
- Tracks the entire lifecycle of an asset, from procurement to disposal.
- Helps organizations make data-driven decisions on asset replacement and maintenance budgeting.
- Example: A fleet management company monitors vehicle depreciation rates and schedules replacements accordingly.
2. Preventive Maintenance Scheduling
CMMS should enable automated scheduling of routine maintenance tasks, reducing downtime and repair costs.
- Automated Preventive Maintenance (PM) Scheduling:
- Allows users to set up custom schedules based on time, meter readings, or usage thresholds.
- Prevents unexpected failures and increases asset lifespan.
- Example: A hotel chain uses CMMS to schedule HVAC system inspections, ensuring optimal guest comfort.
- Predictive Maintenance with IoT Integration:
- Uses IoT sensors to track real-time vibration, temperature, and pressure changes.
- Detects potential failures before they occur, reducing emergency repairs.
- Example: A power plant integrates CMMS with vibration sensors to predict turbine failures.
- Work Order Automation for Routine Tasks:
- Automatically generates work orders for maintenance staff based on predefined conditions.
- Reduces administrative workload and ensures maintenance tasks are never overlooked.
- Example: A university facility team receives auto-generated work orders for classroom air conditioning maintenance.
3. Work Order Management
Efficient work order management enhances team coordination, maintenance planning, and service response times.
- Centralized Work Order Dashboard:
- Provides a real-time view of open, in-progress, and completed work orders.
- Helps prioritize urgent repairs and distribute workload efficiently.
- Example: A logistics company manages fleet maintenance requests through a centralized CMMS dashboard.
- Mobile Work Order Execution:
- Allows technicians to access, update, and complete work orders via mobile devices.
- Improves response time for field teams.
- Example: A facility management team receives instant mobile notifications for HVAC breakdowns in a commercial building.
- Work Order Tracking and Reporting:
- Tracks maintenance completion rates, response times, and technician performance.
- Helps managers optimize workforce allocation.
- Example: A mining company analyzes work order data to improve maintenance efficiency in remote locations.
4. Inventory and Spare Parts Management
CMMS should help organizations manage spare parts and maintenance supplies, preventing stock shortages and excess inventory costs.
- Automated Inventory Tracking:
- Monitors stock levels of critical spare parts and reorders them when supplies are low.
- Reduces downtime caused by missing parts.
- Example: A textile factory prevents production halts by tracking spare motor stock levels.
- Multi-Location Inventory Control:
- Helps businesses manage spare parts across multiple warehouses or facilities.
- Ensures efficient part allocation for different sites.
- Example: A retail chain manages store maintenance supplies across multiple locations.
- Supplier and Purchase Order Integration:
- Links CMMS with suppliers to facilitate automated purchase orders.
- Speeds up procurement for urgent repairs.
- Example: A transportation company automates tire replacement orders for fleet vehicles.
5. Reporting and Analytics
A good CMMS should provide data-driven insights to improve maintenance efficiency and cost-effectiveness.
- Customizable Maintenance Reports:
- Generates reports on downtime, costs, and asset performance.
- Helps management optimize maintenance strategies.
- Example: A utility company analyzes substation maintenance trends to improve reliability.
- Key Performance Indicator (KPI) Tracking:
- Monitors metrics like mean time to repair (MTTR), mean time between failures (MTBF), and maintenance costs.
- Ensures operations align with business goals.
- Example: A food production plant tracks equipment failure rates to minimize wastage.
- Regulatory Compliance Documentation:
- Stores maintenance logs and inspection reports to meet industry standards.
- Reduces legal risks and simplifies audits.
- Example: A pharmaceutical company maintains FDA compliance records with CMMS.
6. User-Friendly Interface and Mobile Accessibility
A CMMS should be intuitive, easy to use, and mobile-compatible for seamless adoption.
- Intuitive Dashboard and Navigation:
- Allows technicians and managers to quickly access work orders, asset details, and reports.
- Reduces training time for new users.
- Example: A hotel maintenance team quickly updates work orders via a user-friendly interface.
- Mobile App for On-the-Go Maintenance:
- Enables technicians to access work orders, scan QR codes, and update maintenance records in real-time.
- Ensures maintenance teams can work from any location.
- Example: A construction company uses CMMS mobile apps to manage on-site equipment servicing.
7. Integration with Other Systems
A CMMS should seamlessly integrate with existing enterprise systems for enhanced functionality.
- ERP and Accounting Integration:
- Links CMMS with ERP software to track maintenance costs.
- Ensures financial accuracy for maintenance budgeting.
- Example: A manufacturing firm integrates CMMS with SAP ERP for expense tracking.
- IoT and Sensor Integration:
- Collects real-time equipment data for predictive maintenance.
- Reduces manual inspections by using automated alerts.
- Example: A wind energy farm uses IoT-enabled CMMS to track turbine efficiency.
- Facility Management System Integration:
- Syncs with building automation and HVAC control systems.
- Improves overall energy efficiency and maintenance coordination.
- Example: A corporate office integrates CMMS with smart HVAC systems for automated temperature adjustments.
Conclusion
Selecting the right CMMS software requires evaluating key features that align with an organization’s maintenance objectives, industry needs, and scalability requirements. Essential features like asset tracking, work order management, preventive maintenance scheduling, inventory control, reporting, mobile access, and system integration play a crucial role in optimizing maintenance operations. Investing in a feature-rich CMMS leads to reduced downtime, cost savings, and improved operational efficiency across industries.
6. Challenges and Considerations in Implementing CMMS
Implementing a Computerized Maintenance Management System (CMMS) can significantly enhance asset management, preventive maintenance, and overall operational efficiency. However, many organizations face challenges and key considerations when adopting CMMS, which can impact its effectiveness and return on investment (ROI).
Below are the most common challenges and important factors to consider when implementing a CMMS, along with relevant examples.
1. Resistance to Change and User Adoption
One of the biggest hurdles in CMMS implementation is employee resistance and a lack of willingness to adopt new technology.
- Lack of Training and Awareness:
- Employees may find CMMS complex or intimidating without proper training.
- Without adequate knowledge, teams might rely on old manual processes, reducing the system’s effectiveness.
- Example: A manufacturing plant introduces CMMS for work order tracking, but maintenance staff continue using paper-based logs due to insufficient training.
- Fear of Job Displacement:
- Some employees may perceive CMMS as a threat, fearing automation will replace jobs.
- Organizations must clarify that CMMS is meant to enhance efficiency, not reduce workforce size.
- Example: A facility management company encounters resistance from senior technicians who believe automated scheduling will eliminate their roles.
- Overcoming Resistance with Change Management Strategies:
- Conduct interactive training sessions to familiarize users with CMMS features.
- Involve employees in the decision-making process to encourage engagement.
- Example: A hospital maintenance team successfully adopts CMMS after attending hands-on workshops that demonstrate its benefits in reducing equipment downtime.
2. High Initial Implementation Costs
While CMMS delivers long-term savings, the initial costs of software, training, and infrastructure upgrades can be a challenge.
- Software Licensing and Subscription Fees:
- Many CMMS providers offer subscription-based pricing, which may increase operational expenses.
- Businesses must carefully evaluate pricing plans and feature sets to ensure cost-effectiveness.
- Example: A small manufacturing company hesitates to invest in CMMS due to ongoing subscription costs exceeding their budget.
- Hardware and IT Infrastructure Upgrades:
- Some CMMS solutions require server installations, mobile devices, or IoT sensor integration, leading to additional costs.
- Organizations must assess whether cloud-based CMMS can reduce infrastructure expenses.
- Example: A utility company adopts cloud-based CMMS to eliminate the need for expensive on-premise servers.
- Budgeting and Cost-Benefit Analysis:
- Organizations should conduct a cost-benefit analysis to justify CMMS investment.
- Evaluating long-term savings from reduced downtime and maintenance efficiency can help secure stakeholder buy-in.
- Example: A logistics firm demonstrates that CMMS implementation will reduce fleet maintenance costs by 20% over three years.
3. Data Migration and System Integration Challenges
Transferring existing maintenance records and integrating CMMS with other enterprise systems can be complex and time-consuming.
- Migrating Legacy Maintenance Data:
- Organizations must clean, validate, and format existing maintenance data before importing it into CMMS.
- Incomplete or incorrect data can lead to inaccurate maintenance schedules and asset tracking issues.
- Example: A municipal water treatment plant faces difficulties migrating 20 years’ worth of manual maintenance records into CMMS.
- Integration with Existing Enterprise Systems:
- CMMS must integrate with Enterprise Resource Planning (ERP), Accounting, and HR management systems.
- Poor integration can result in data silos, inefficient workflows, and inaccurate financial tracking.
- Example: A retail chain struggles to sync CMMS work orders with their accounting software, delaying supplier payments for spare parts.
- Ensuring Compatibility with IoT and Smart Devices:
- Advanced CMMS solutions integrate with IoT sensors to enable predictive maintenance.
- Organizations need to ensure compatibility with existing equipment to leverage real-time data insights.
- Example: A wind energy farm upgrades CMMS to integrate with turbine performance sensors, preventing unexpected breakdowns.
4. Customization and Scalability Issues
Choosing a CMMS that fits current business needs while allowing for future expansion is crucial.
- Limited Customization for Industry-Specific Needs:
- Some CMMS solutions offer generic features that may not align with industry-specific maintenance requirements.
- Businesses must select CMMS software that supports custom workflows and asset categories.
- Example: A pharmaceutical company struggles with a CMMS that lacks compliance tracking for FDA maintenance regulations.
- Scalability for Growing Operations:
- A CMMS should be able to handle increasing asset volume, new locations, and expanding maintenance teams.
- Organizations must assess whether the chosen CMMS can scale without performance issues.
- Example: A construction firm needs a CMMS that scales as new project sites are added, ensuring consistent maintenance across all locations.
- Configuring User Permissions and Role-Based Access:
- A well-structured CMMS should provide role-based access control to protect sensitive maintenance data.
- Setting up permissions can be complex and requires careful planning.
- Example: A hospital maintenance team configures CMMS so that technicians can access only relevant work orders, while managers oversee reporting dashboards.
5. Measuring ROI and Long-Term Effectiveness
Organizations must track key performance indicators (KPIs) to assess whether CMMS implementation delivers expected benefits.
- Defining Success Metrics for CMMS Implementation:
- Metrics such as mean time to repair (MTTR), asset uptime, and maintenance costs should be measured.
- Regular performance evaluations ensure CMMS is meeting efficiency goals.
- Example: A food processing plant tracks reduced equipment downtime after CMMS implementation to measure ROI success.
- Ensuring Continuous Improvement in Maintenance Workflows:
- CMMS should not be a one-time setup—organizations must continuously refine maintenance strategies based on real-time data insights.
- Conducting periodic employee feedback sessions helps optimize system usage.
- Example: A railway company holds quarterly meetings to review CMMS-generated reports and adjust maintenance schedules.
- Assessing Vendor Support and Software Updates:
- Ongoing vendor support ensures CMMS remains functional, secure, and updated with the latest features.
- Lack of support can lead to system downtimes and security vulnerabilities.
- Example: A municipal waste management company partners with a CMMS provider offering 24/7 support to minimize disruptions.
Conclusion
Implementing a CMMS solution presents several challenges, including resistance to change, high costs, data migration difficulties, customization limitations, and measuring ROI. However, businesses can overcome these hurdles by prioritizing employee training, choosing scalable solutions, ensuring seamless integration, and continuously monitoring maintenance performance.
A well-planned CMMS implementation leads to long-term benefits such as reduced downtime, improved asset reliability, and enhanced cost efficiency, making it a valuable investment for organizations across industries.
7. Future Trends in CMMS
The Computerized Maintenance Management System (CMMS) industry is rapidly evolving with technological advancements, AI-driven automation, and data analytics. As businesses strive for greater efficiency, cost savings, and predictive maintenance, CMMS solutions are integrating new features to enhance asset management, maintenance scheduling, and operational workflows.
This section explores the emerging trends in CMMS that are shaping the future of maintenance management.
1. AI and Machine Learning for Predictive Maintenance
Artificial Intelligence (AI) and Machine Learning (ML) are transforming CMMS solutions by enabling predictive maintenance strategies instead of reactive or preventive approaches.
- Predicting Equipment Failures Before They Happen:
- AI-powered CMMS analyzes historical maintenance data, sensor inputs, and real-time equipment performance to predict potential failures.
- Reduces unexpected breakdowns and extends asset lifespan.
- Example: A manufacturing plant uses AI-driven CMMS to detect early signs of motor overheating and schedules maintenance before failure occurs.
- Automated Work Order Prioritization:
- AI can analyze urgency levels based on equipment criticality and failure risk, ensuring high-priority repairs are addressed first.
- Example: A hospital maintenance team leverages AI to prioritize MRI scanner repairs over non-critical assets.
- Self-Learning Maintenance Strategies:
- Machine learning algorithms continuously improve maintenance schedules by identifying patterns in repair frequencies and failure causes.
- Example: An oil refinery notices AI adjusting lubrication schedules based on past oil degradation trends.
2. IoT and Smart Sensors for Real-Time Monitoring
The Internet of Things (IoT) is revolutionizing CMMS by integrating smart sensors that provide real-time data on asset health and performance.
- Continuous Condition Monitoring:
- IoT-enabled CMMS collects data on temperature, pressure, vibration, and energy consumption to detect anomalies.
- Allows maintenance teams to act immediately when abnormal patterns are detected.
- Example: A wind farm deploys IoT sensors to monitor turbine vibrations, preventing catastrophic failures.
- Automated Alerts and Notifications:
- When equipment operates outside normal thresholds, the CMMS automatically triggers alerts and creates maintenance work orders.
- Example: A food processing facility receives instant alerts when refrigeration units exceed temperature limits, ensuring food safety compliance.
- IoT-Enabled Remote Asset Management:
- Maintenance teams can monitor and troubleshoot equipment remotely, reducing the need for on-site inspections.
- Example: A utilities company manages water pumps and electrical substations remotely using IoT-integrated CMMS.
3. Cloud-Based CMMS for Scalability and Accessibility
As businesses expand operations, cloud-based CMMS solutions are gaining traction due to scalability, remote access, and cost-efficiency.
- Anywhere, Anytime Access:
- Cloud-based CMMS allows maintenance teams to access asset records, work orders, and reports from any location using mobile devices or web portals.
- Example: A logistics company enables technicians to update maintenance logs from remote warehouses via cloud-based CMMS.
- Lower Infrastructure Costs:
- Eliminates the need for on-premise servers, reducing IT maintenance expenses and security concerns.
- Example: A small manufacturing firm saves on IT costs by adopting a subscription-based CMMSinstead of maintaining physical servers.
- Seamless Software Updates and Security Enhancements:
- Cloud-based CMMS providers automatically roll out updates, bug fixes, and security patches without disrupting operations.
- Example: A pharmaceutical company benefits from automatic compliance updates for industry regulations in its cloud-based CMMS.
4. Mobile CMMS and Augmented Reality (AR) for Field Technicians
Mobile CMMS and augmented reality (AR) applications are enhancing technician efficiency and on-the-go maintenance capabilities.
- Mobile Work Order Management:
- Technicians can view, update, and close work orders directly from smartphones or tablets.
- Reduces paperwork and streamlines real-time communication.
- Example: A construction company equips field technicians with mobile CMMS to track heavy machinery maintenance.
- AR for Guided Repairs and Remote Assistance:
- Augmented reality (AR) overlays digital instructions, schematics, and troubleshooting guides onto equipment via smart glasses or tablets.
- Enables remote experts to assist on-site technicians in real-time diagnostics.
- Example: An automotive assembly plant integrates AR with CMMS to assist junior technicians with complex machinery repairs.
- Barcode and QR Code Scanning for Quick Asset Access:
- Mobile CMMS apps allow technicians to scan QR codes or barcodes on equipment to instantly retrieve service history, manuals, and repair logs.
- Example: A hospital maintenance team scans QR codes on X-ray machines to access past maintenance records.
5. CMMS with AI-Driven Reporting and Business Intelligence (BI)
AI-powered CMMS platforms are evolving to provide advanced reporting, trend analysis, and actionable insightsfor better decision-making.
- Automated KPI Tracking and Performance Dashboards:
- AI analyzes CMMS data to generate real-time performance metrics such as mean time to repair (MTTR), mean time between failures (MTBF), and asset downtime.
- Example: A city transportation authority uses AI-powered CMMS to optimize bus fleet maintenance schedules based on usage trends.
- Cost Optimization and Maintenance Budget Forecasting:
- Predictive analytics helps organizations forecast maintenance costs based on historical spending, part replacements, and labor expenses.
- Example: A facility management company reduces operational expenses by automating spare part inventory restocking based on usage patterns.
- Automated Compliance and Audit Readiness:
- AI-driven CMMS ensures organizations adhere to industry regulations, generating audit reports and compliance documentation automatically.
- Example: A chemical manufacturing plant generates OSHA and EPA compliance reports directly from CMMS.
6. Blockchain Technology for Secure Maintenance Records
Blockchain is emerging as a reliable method for ensuring data integrity, security, and transparency in CMMS systems.
- Tamper-Proof Maintenance Records:
- Blockchain creates immutable maintenance logs, ensuring data cannot be altered or falsified.
- Example: An aerospace company stores aircraft maintenance histories in a blockchain-powered CMMSto comply with FAA regulations.
- Smart Contracts for Automated Maintenance Agreements:
- Enables automated service agreements between organizations and external contractors, ensuring maintenance deadlines and payments are met.
- Example: A shipping company uses blockchain-based CMMS to track ship engine maintenance contracts with third-party providers.
- Enhanced Equipment Lifecycle Tracking:
- Blockchain provides a secure chain of custody for equipment repairs, part replacements, and performance history.
- Example: A medical device manufacturer ensures traceability of surgical equipment servicing recordsusing blockchain.
Conclusion
The future of CMMS technology is driven by AI, IoT, cloud computing, mobile accessibility, and blockchain security. These emerging trends are transforming asset management, predictive maintenance, and real-time data analytics, leading to optimized workflows, cost savings, and enhanced operational efficiency.
As organizations continue to embrace digital transformation, integrating these advanced CMMS capabilities will become essential for staying competitive, reducing downtime, and improving maintenance strategies across industries.
Conclusion
A Computerized Maintenance Management System (CMMS) is a powerful digital solution that transforms how organizations manage assets, maintenance schedules, work orders, and operational efficiency. By centralizing maintenance data and automating processes, CMMS significantly improves productivity, reduces costs, enhances asset longevity, and ensures regulatory compliance across various industries.
The Growing Importance of CMMS in Modern Industries
As businesses expand and asset management becomes more complex, the reliance on data-driven maintenance strategies is increasing. CMMS provides a structured approach to preventive, predictive, and reactive maintenance, enabling organizations to transition from manual maintenance tracking to fully automated workflows. Industries such as manufacturing, healthcare, energy, transportation, and facility management benefit from CMMS by ensuring minimal downtime, optimized resource allocation, and real-time performance monitoring.
Moreover, CMMS helps companies adhere to industry regulations by maintaining detailed maintenance logs, audit trails, and compliance reports. Organizations that implement CMMS experience fewer operational disruptions, improved safety standards, and a more structured approach to asset lifecycle management.
How CMMS Enhances Maintenance Operations
CMMS is designed to address key challenges in maintenance management, including equipment failures, unplanned downtime, inefficient work order handling, and excessive maintenance costs. By integrating asset tracking, inventory management, and real-time monitoring, CMMS ensures that maintenance teams work proactively rather than reactively.
- Optimized Work Order Management: Streamlines maintenance requests, scheduling, and completion tracking.
- Improved Asset Performance: Reduces equipment breakdowns and extends asset lifespan through preventive maintenance.
- Efficient Spare Parts Management: Ensures that required spare parts and materials are always available.
- Automated Reporting and Compliance Management: Facilitates regulatory adherence and audit readiness.
Future of CMMS and Its Role in Digital Transformation
The future of CMMS is driven by technological advancements such as Artificial Intelligence (AI), Machine Learning (ML), the Internet of Things (IoT), cloud computing, and mobile accessibility. These innovations are enabling predictive maintenance strategies, real-time monitoring, remote asset management, and AI-driven analytics.
- AI and Predictive Maintenance: Helps organizations forecast failures before they occur, reducing unexpected downtime.
- IoT Integration: Enables real-time condition monitoring of equipment, enhancing operational efficiency.
- Cloud-Based CMMS: Improves scalability, data security, and remote access to maintenance records.
- Mobile CMMS Solutions: Allow field technicians to manage work orders and access asset data from anywhere.
With the rise of Industry 4.0 and smart manufacturing, CMMS will continue evolving to support automated decision-making, digital twins, and AI-powered maintenance optimization. Companies that embrace these next-generation CMMS solutions will gain a competitive edge by achieving higher productivity, lower maintenance costs, and improved asset reliability.
Final Thoughts
Implementing a Computerized Maintenance Management System is no longer a luxury but a necessity for organizations looking to streamline maintenance operations, reduce costs, and maximize asset performance. Whether managing a small facility or a large-scale industrial plant, CMMS provides the digital infrastructure needed to optimize maintenance workflows and ensure long-term sustainability.
As businesses move toward a more data-driven and technology-centric approach, investing in a CMMS solutiontailored to their operational needs will be crucial for achieving greater efficiency, compliance, and long-term asset optimization. By leveraging automation, predictive analytics, and mobile capabilities, organizations can create a smarter, more proactive maintenance strategy that delivers sustained growth and operational excellence.
If you find this article useful, why not share it with your hiring manager and C-level suite friends and also leave a nice comment below?
We, at the 9cv9 Research Team, strive to bring the latest and most meaningful data, guides, and statistics to your doorstep.
To get access to top-quality guides, click over to 9cv9 Blog.
People Also Ask
What is a Computerized Maintenance Management System (CMMS)?
A CMMS is software that helps organizations manage maintenance operations, schedule work orders, track assets, and optimize resource usage for improved efficiency.
How does a CMMS work?
A CMMS automates maintenance workflows by tracking equipment data, scheduling preventive maintenance, and generating reports for better decision-making.
What are the key features of a CMMS?
A CMMS includes work order management, asset tracking, preventive maintenance scheduling, inventory control, and reporting tools for data-driven maintenance.
What industries use CMMS software?
CMMS is widely used in manufacturing, healthcare, facilities management, energy, transportation, and other industries that require efficient maintenance operations.
How does CMMS improve asset management?
CMMS centralizes asset information, tracks performance history, schedules maintenance tasks, and reduces downtime, extending the lifespan of equipment.
What is the difference between CMMS and EAM software?
CMMS focuses on maintenance management, while Enterprise Asset Management (EAM) includes broader asset lifecycle management beyond maintenance.
How does CMMS help with preventive maintenance?
CMMS automates preventive maintenance schedules, ensuring timely servicing of equipment to prevent unexpected failures and costly downtime.
What are the benefits of using a CMMS?
A CMMS reduces downtime, improves asset reliability, enhances productivity, ensures regulatory compliance, and lowers maintenance costs.
Can CMMS be integrated with other software?
Yes, CMMS can integrate with ERP, IoT sensors, SCADA systems, and other business software for seamless data exchange and enhanced efficiency.
What is the role of IoT in CMMS?
IoT-enabled CMMS collects real-time equipment data, enabling predictive maintenance and proactive issue resolution before failures occur.
What is the difference between preventive and predictive maintenance?
Preventive maintenance follows a scheduled routine, while predictive maintenance uses data and analytics to anticipate failures before they happen.
How does CMMS help in reducing downtime?
CMMS schedules maintenance proactively, tracks equipment conditions, and ensures repairs are done on time to prevent unexpected breakdowns.
Can CMMS improve workplace safety?
Yes, CMMS ensures compliance with safety regulations, schedules safety inspections, and reduces equipment malfunctions that could cause workplace accidents.
How do businesses implement a CMMS?
Implementation involves selecting the right software, migrating asset data, training staff, configuring workflows, and integrating with existing systems.
What are the challenges in implementing a CMMS?
Challenges include data migration, staff training, resistance to change, software integration complexities, and ensuring proper system adoption.
Is CMMS suitable for small businesses?
Yes, many CMMS solutions offer scalable options, making them ideal for small businesses looking to improve maintenance efficiency and asset management.
How does CMMS improve compliance with regulations?
CMMS keeps records of maintenance activities, schedules inspections, and generates compliance reports for regulatory audits.
What are cloud-based CMMS solutions?
Cloud-based CMMS operates on remote servers, offering flexibility, remote access, automatic updates, and lower upfront costs compared to on-premise systems.
How secure is cloud-based CMMS?
Cloud CMMS providers implement encryption, access controls, and regular security updates to ensure data protection and compliance with industry standards.
Can CMMS track inventory and spare parts?
Yes, CMMS monitors spare parts inventory, automates reordering, and ensures availability of essential components to prevent maintenance delays.
How does CMMS support cost reduction?
CMMS optimizes maintenance schedules, prevents costly breakdowns, reduces labor inefficiencies, and extends asset lifespan, lowering overall expenses.
What types of reports can CMMS generate?
CMMS generates reports on asset performance, maintenance costs, work order history, downtime trends, and compliance metrics for data-driven decision-making.
How long does it take to implement a CMMS?
Implementation time varies based on company size and complexity but typically ranges from a few weeks to several months, including training and data migration.
How does AI enhance CMMS functionality?
AI-driven CMMS predicts failures, automates maintenance schedules, analyzes performance data, and enhances decision-making with machine learning insights.
What is mobile CMMS?
A mobile CMMS is a mobile-friendly solution that allows technicians to access work orders, update maintenance logs, and manage assets from any location.
Can CMMS help with sustainability initiatives?
Yes, CMMS reduces energy waste, optimizes equipment efficiency, minimizes paper usage, and supports sustainability goals through better resource management.
How does CMMS assist in work order management?
CMMS automates work order creation, assigns tasks to technicians, tracks job progress, and maintains a history of completed maintenance activities.
What are the future trends in CMMS?
Future trends include AI-driven predictive maintenance, IoT integration, cloud-based solutions, and enhanced automation for proactive asset management.
How can businesses choose the right CMMS software?
Businesses should consider ease of use, scalability, integration capabilities, mobile access, reporting features, and customer support before selecting a CMMS.